Auf neuen Wegen zum Bauteil
Verfahren, die bisher im Kunststoffbereich genutzt wurden, bringen jetzt auch Stahl & Co. in Form.
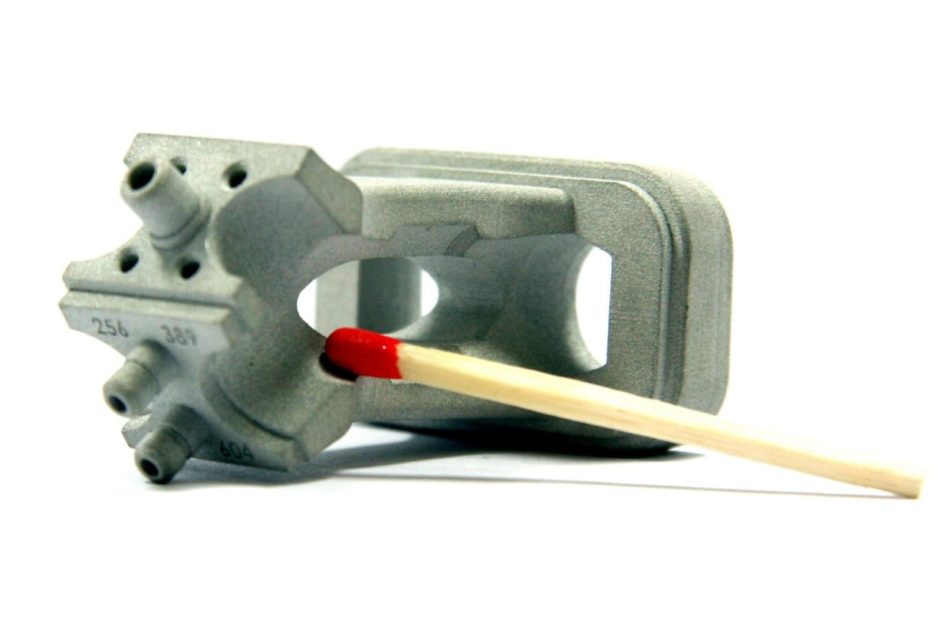
Foto: Metshape
Vorbei sind die Zeiten, in denen das additive Fertigen von Metallteilen finanzkräftigen Firmen und Forschungseinrichtungen vorbehalten war. Es braucht keine schrankgroßen Maschinen mehr, die Laser- oder Elektronenstrahlen unter Schutzgasatmosphäre über ein Pulverbett tanzen lassen. Hohe sechsstellige Investments sind also obsolet. Um Stahl & Co. millimetergenau in Form zu bringen, können heute ein paar Tausend Euro und ein kleines Plätzchen auf dem Schreibtisch genügen. Möglich wird das durch Verfahren, die ursprünglich aus dem Kunststoffbereich kommen.
Am günstigsten wird es für Konstruk‧teure, die bereits einen Schmelzschichtdrucker zu Hause haben. Denen fehlt nur noch ein Kunststofffilament, in das winzige Metallpartikel eingebettet sind. Die BASF 3D Printing Solutions GmbH hat gerade ein solches Material auf den Markt gebracht. 3 kg kosten 460 €. Verarbeitet wird es wie die üblichen Thermoplaste. Neu ist der zweite Produktionsschritt: Das gedruckte Bauteil muss noch gesintert werden. Da der heimische Ofen dafür nicht ausreichend heiß wird, baut die BASF-Tochter gerade ein Netzwerk aus Dienstleistern auf.
Auf gefüllte Filamente setzt auch die US-Firma Markforged. Ihr „Metal X“-Drucker ist zwar nicht mehr desktoptauglich, dafür aber auch für industrielle Anwendungen geeignet. Er bringt mit einem zweiten Extruder automatisch Keramiktrennschichten zwischen Bauteil und etwaige Stützstrukturen aus und erzeugt Schichtstärken bis hinunter auf 50 µm. Inklusive Sinterofen kostet er 195 000 €.
Noch genauer – und mit 240 000 € auch etwas teurer – ist der Drucker des Pforzheimer Start-ups Metshape. Er basiert auf dem LMM-Verfahren (Lithography-based Metal Manufacturing). Dabei wird ein photosensitives Polymer, in dem feinstes Metallpulver gelöst ist, schichtweise mit einem Projektor belichtet. Im Präzisionsmodus ist jede Schicht lediglich 20 µm hoch. Das entstehende Grünteil muss abschließend ebenfalls gesintert werden. Anschließend weisen die Oberflächen einen Mittenrauwert von unter 7 µm auf.
Noch sind laserbasierte Verfahren in der Industrie führend. Aufgrund ihrer vergleichsweise langen Historie – das erste Patent in Deutschland wurde 1995 erteilt – haben sie einen Forschungsvorsprung. Das wird deutlich beim Blick auf die Pulverherstellung und -qualifizierung. Bei Rosswag Engineering, dem ersten TÜV-zertifizierten Hersteller von Metallpulver für die additive Fertigung, wird quasi jedes Partikelchen seziert und optimiert, um die Basis für ein perfektes Bauteil liefern zu können.
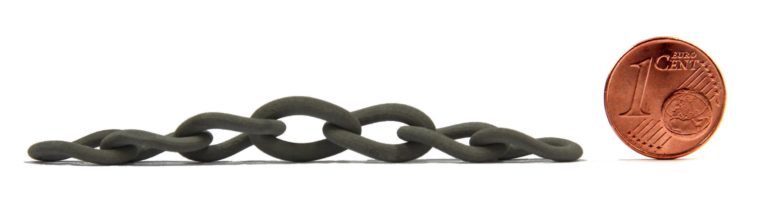