Qualität entsteht in der Entwicklung
Wie Ingenieure und Qualitätsexperten zusammenwachsen.
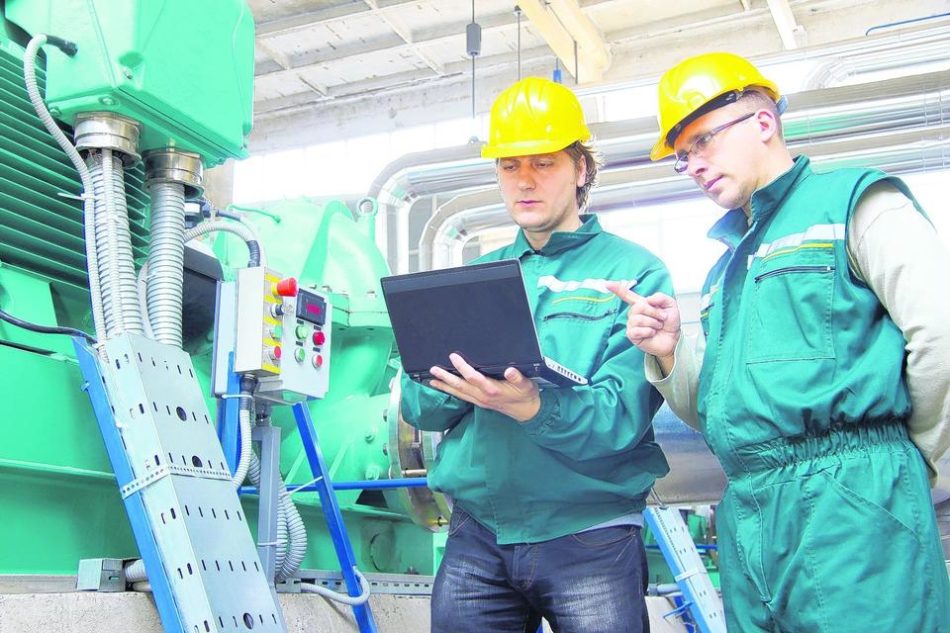
Foto: panthermedia.net/branex
Wer sich bei der Entwicklung von Produkten und Prozessen mit Qualität beschäftigt, spart in der Herstellungsphase Zeit und Kosten. Quality by Design (QbD) steht in der Medizintechnik, bei Autozulieferern und Kunststoffexperten hoch im Kurs. Um die Null-Fehler-Quote zu schaffen, braucht es Mitarbeiter mit technischem Verständnis und akribischem Blick für Details.
Wenn beim Verpackungshersteller Gerresheimer Glasröhren zu Ampullen oder kleinen Medizinfläschchen geformt werden, haben Ingenieure genauso wie Qualitätsexperten ihre Finger im Spiel. „Es gibt eine Vielzahl von Knackpunkten, an denen Qualitätsmängel auftreten können“, sagt Senior Direktor und Qualitätschef Volker Rekowski. Das fängt beim Ausgangsprodukt an, einer Glasröhre, die das Düsseldorfer Unternehmen bei Zulieferern einkauft. Verformungen, Einschlüsse oder Verfärbungen im Glas können das spätere Produkt genauso beeinflussen, wie kleinste Temperaturschwankungen im Verarbeitungsvorgang.
Natürlich müssen beim Zulieferer für Medizin, Kosmetik und Pharma Verpackungen steril abgeliefert werden. Mit speziellen Verformungsprozessen wird bei Gerresheimer mit möglichst wenig mechanischem Kontakt geschnitten, geschmolzen und geformt. Die 3 cm bis 10 cm langen Glasbehälter werden nach der Herstellung gesintert, also durch einen 600 °C heißen Ofen geführt, in dem sich das Material nach dem Verformen bei 1600 °C entspannt.
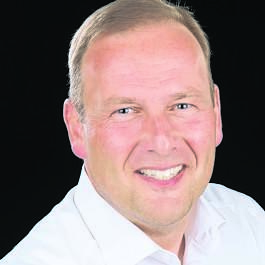
„In Branchen wie Medizintechnik und Automotive ist die Qualität des Produkts und der Prozesse erfolgsentscheidend für ein Unternehmen“, sagt Martin Felch, Auditor für verschiedene ISO-Normen und Geschäftsführer der Iso-Project Felch GmbH. Hier geht es nicht ausschließlich um den wirtschaftlichen Vorteil, wenn weniger Ausschuss anfällt, oder Rückrufe vermieden werden. „Wenn Unternehmen die gesetzlichen Bestimmungen hinsichtlich qualitätsrelevanter Spezifikationen nicht einhalten, droht ihnen der wirtschaftliche Ruin“, sagt der Berater mit mehr als 20 Jahren praktischer Erfahrung in der industriellen Fertigung. Etwa, wenn Medizinprodukte wegen Fehlern vom Markt genommen werden müssen, überleben das manche Hersteller nicht.
„Wir arbeiten mit Toleranzen im Bereich von zehntel Millimetern“, erklärt Rekowski von Gerresheimer. Der 47-Jährige ist promovierter Chemiker mit viel Industrieerfahrung. Schon früh kam er zum Qualitätsmanagement, wo er bis heute einen wichtigen Faktor für den Erfolg seiner Firma und die hohe Kundenzufriedenheit sieht.
Um die Qualitätsanforderungen der Hersteller, aber auch der Kunden und schließlich der Endverbraucher zu erfüllen, dreht Gerresheimer an jeder Stellschraube. Stichwort Patienten- und Produktsicherheit. „Ein wichtiger Faktor sind gut ausgebildete Mitarbeiter“, sagt der Qualitätsexperte. Das sind vor allem die Ingenieure, die die Maschinen justieren, die Prozesse entwickeln und die Produktion überwachen. Aber auch die Mitarbeiter an der Anlage müssen Know-how und einen guten Blick für das Detail beweisen.
Kleine Glaspartikel etwa, die beim Schneiden abspringen, dürfen weder am Glas haften bleiben noch ins Innere gelangen. „Wir haben deshalb einen Schneidprozess mit unseren Entwicklungsingenieuren realisiert, bei dem möglichst wenig Splitter entstehen.“
Rekowski hält nichts davon, Qualität im Nachhinein in einen Vorgang „hineinzuinspizieren“. Vielmehr setzt das Verpackungsunternehmen schon bei Anlagendesign und -entwicklung auf zuverlässige und reproduzierbare Prozesse. Anlagen, Produkte und Fertigungsschritte sind bei Gerresheimer streng validiert. Das heißt, sie werden intern, extern oder durch den Kunden regelmäßig überprüft und optimiert.
Bewertet er die Produktion von Unternehmen, schaut sich Qualitätsexperte Felch verschiedene Kennzahlen an. Der Prozessfähigkeitsindex CpK ist so eine. Sie gibt Aufschluss über die Fehlerhäufigkeit pro Million gefertigter Teile. Dieser Wert sollte mindestens 1,33 betragen. „Ideal ist es außerdem, wenn ein Hersteller innerhalb seines standardisierten Prozesses auf kleine Abweichungen, z. B. im Material, reagieren kann“, sagt der Berater, der oft gerufen wird, wenn das Audit nicht bestanden wurde oder ein Produkt vom Markt zu verschwinden droht. Ein Richtwert, an dem sich Verpackungsunternehmen orientieren können, ist die DIN EN ISO 13485:2016. Den Ansatz, nicht nur auf perfekt justierte Technik zu setzen, findet der Ingenieur und Betriebswirt gut: „Letztlich ist ein Prozess nur so gut wie die Menschen, die ihn steuern.“