International Conference on Gears 2023
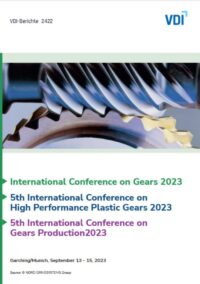
Erscheinungsdatum: 13.09.2023
Reihe: VDI-Berichte
Band Nummer: 2422
Ort: Garching bei München
ISBN: 978-3-18-092422-9
ISSN: 0083-5560
Erscheinungsjahr: 2023
Anzahl Seiten: 1918
Produktart: PDF-Datei
Produktbeschreibung
Foreword
The International Conference on Gears in Garching near Munich, Germany, is an established platform for researchers on and manufacturers of gears and transmission systems. At the 10th issue of the conference in September of 2023, gear experts discussed the latest developments and research results from the powertrain industry and academia.
Given the increasing challenges of climate change and its impacts, acting in compliance with the UN Sustainable Development Goals is mandatory for all engineers today. Gear engineers must consider these objectives in their research and development activities and provide solutions that meet the technical requirements and contribute to achieving the UN goals.
Greenhouse gas (GHG) emission is a primary driver for climate change. Reducing GHG emissions should be an urgent action for the combat against climate change. Therefore, the research on efficiency is assigned a key role. Several contributions in this report discuss the possibilities for further improvement in efficiency from different points of view, like gear design or lubrication. Other subjects of the conferences are Responsible Consumption and Production. Here, enhanced calculation methods of the load-carrying capacity of both steel and highperformance plastic gears are given to reduce the usage of resources. Furthermore, extending the life cycle of gear systems by repairing and reusing them in compliance with this goal is also the subject of expert contributions.
Within this report, you will find the complete arrangement of proceedings of the presentations during the VDI International Conference on Gears 2023. I wish you an instructive and enjoyable reading of this Special Issue, and may it inspire your own work.
On behalf of the program committee.
Your Conference President
Prof. Dr.-Ing. Karsten Stahl
Full Professor, Institute of Machine Elements
Director, Gear Research Center (FZG), Technical University of Munich (TUM) Garching, Germany
Contents
Foreword 1
Keynote session:
Re-X: Recycle | Reuse | Reduce
Increasing Air Travel and the Challenge to Reduce Emissions 3
Efficiency-improvement with low-loss-gears by two different application 13
Tooth root load & carrying capacity
Optimised statistical evaluation for the determination of tooth root endurance strength 19
The consequences of different methodologies for the elaboration of pulsator test results with respect to the load spectrum assessment of gears 33
Tooth Bending Strain Rate Analysis in a Counter Shaft Drivetrain and Implications on Fatigue Strength 53
Damage detection
Investigation of the electrical behavior of a spur gear stage pair by means of impedance measurements 67
Measuring Instantaneous Angular Speed using a Gear Wheel as Material Measure to detect Pitting Damage during an Endurance Test 81
Pitting Detection for Prognostics and Health Management in Gearbox Applications 97
Load capacity
Crack growth based tooth root life prediction model – an influence quantity analysis 109
Experimental Investigation of the load carrying capacity of beveloid gears with optimized flank topography 125
Statistical study of the mesh load factor of planetary gear transmissions affected by inherent manufacturing errors 139
Planetary gears: NVH
Vibration reduction of planetary gear drive using mesh phasing: modelling and experimental validation 157
Influence of Axis Misalignments in Stepped Planetary Gear Stages on the Excitation Behavior – Test Rig Development and Simulative Analysis 175
Design, application, standardization
Review of different calculation approaches for the mean coefficient of friction in ISO 6336 191
Forward Performance-driven Design of Gear Parameters 211
Tooth flank load capacity
Scuffing load carrying capacity of high-speed gears with an isotropic superfinished surface 227
On the Testing of Flank Fracture Calculations Based on 3D-Gears 243
White Etching Cracks (WECs) on gears of E-Axle applications 257
Planetary gears: Load distribution
Parametric system simulation of load sharing in planetary gearboxes 269
Mesh Load Factor in Multiple Planetary Stage Gearboxes 281
Assessing gear mesh misalignment in a parallel gear set by transmission error measurements 291
Load capacity
Review of the definition of the loads for spur and helical gears in standards and handbooks 301
Hybrid models for the simulation of displacements and stresses in lightweight gears 315
Development of Damage-based Accelerated Life Test Code for Gearbox using Genetic Algorithm 329
NVH: Impacts
Acoustical behavior of periodic flank modifications under dynamic operating conditions 341
The Influence of Wheel Body Design on Airborne Noise 357
Impact of manufacturing deviations on the NVH behavior of modern gear design concepts 367
Asymmetric gear geometry
Design optimization of multi-stage gear trains with asymmetric teeth under a broad range of torques by incorporating multibody simulations 383
Comparing the contact characteristics of involute gear/ eccentric cycloidal gear calculated by various loaded tooth contact analysis models 397
Contact simulation of tooth flanks using Isogeometric Analysis 413
Planetary gears: Simulation and lubrication
Simulation Study on the Tribological Characteristics in the Meshing Contact in the Context of the Load Carrying Capacity Calculation of Internal Gears with Unbalanced Sliding Conditions 429
Thermal model of a planetary gear set using an isothermal approach 451
Wetting and oil flow analysis of planetary gearboxes using oil flow simulations 467
CFD: Applications
Challenges and possibilities of virtual development of e-axletransmissions 485
Latest advancements in the lubrication simulations of geared systems: a technology ready for industrial applications 499
Lubrication improvement at the HS-IS spline shaft interface of a wind turbine gearbox using the smooth particle hydrodynamic method 519
Planetary gears: Design
Design and analysis of compound stepped planetary gear drives for better transmission performances 537
Evaluation of the effect of the rim thickness on the root stress cycle of helical planet gears with integrated rollers 553
Experimental Investigation of Moving Contact Pattern in Helical Planetary Gearboxes 569
NVH: Analysis
A comparison of time and frequency domain approaches for NVH 583
Investigation of Sound and Vibration Behavior of Cylindrical Gears 599
Validation of an industrial gearbox model for predicting vibro-acoustic behavior 619
Smart gears
Helicopter Drive System Safety Dissertation 633
Smart Gearboxes for a Sustainable and Reliable Industry 645
Effect of Load Cycles on Return Loss and Resistance of Sensor and Antenna Circuits Printed on Plastic Gears 659
NVH
Electromechanical Coupling Modeling and Torsional Vibration Analysis of Helicopter Electric Propulsion System 675
Numerical analysis of bevel gear transmission acoustic emission using a 3D gear contact force model within a multibody system dynamics simulation environment 689
Experimental Investigation of Influence of Indexing Errors on Gear Rattling 703
Lubrication
Lubricant Free Transmissions for the food industry – A Comparison 715
Analysis of Load Cycles and Local Wear of Dry and Solid-Lubricated Gears 727
Considerations on Lubrication of High-Speed Rotating Gear (First Report) 741
Efficiency and friction
Gear friction coefficient estimation using directional parameter under ATF lubricated condition 753
Effect of LOL conditions under high velocity and high injection temperatures 763
Influence of Surface and Material Technologies on Loss of Lubrication Performance of Gears 779
Efficiency: Gearbox
On the reduction of windage power losses in gears by the modification of tooth geometry 785
Efficient concepts for high ratio angular gearboxes 801
Holistic Sustainability-Assessment of Gearboxes 815
Bevel and hypoid gears
The relevance of pinion deflection and twisting for loaded tooth contact analysis of high reduction hypoid gears 829
The effect of pinion axial positioning on noise and transmission error of face hobbed and face milled bevel gears 839
Exploration of trade-offs between NVH and efficiency in bevel gear design 853
Strength: Bevel, hypoid & worm gears
Transferability of the scuffing load capacity of gear oils determined on spur gears to hypoid gears 881
Fatigue testing of large sized bevel gears 897
Calculation method for wear of steel-bronze rolling-sliding contacts relating to worm gears 907
Design geometry
Local load capacity analysis for the design of a balanced flank modification for cylindrical gears according to bevel gear procedures 927
Analysis of new tooth profile design based on the biomimetics principles 945
Analysis of the tip interference in low gear ratio internal spur gears with profile modification 957
Efficiency & friction
Simulation-based optimization of gearing efficiency using thin coatings 975
Gearbox efficiency of eDrives: correlation between measurement and calculation of load-dependent torque losses 985
Effects of Surface Engineering on the Efficiency of Involute HelicalGears – An Experimental Investigation 995
Digitalization of the product development process
Digitalization of the Gear Development Process – Chances, Benefits and Risks 1017
Opportunities arising from digital twins in gear development 1027
Poster Exhibition
Modelling and Analysis of the Effect of Root Modification on Load Sharing and Stress Values on Spur Gears 1039
LUBGEAR – Experimental Campaign for Aviation Gears in Loss-ofLubrication 1063
PVD Deposition of Nb-MoS2 Coatings on Gear Carburized Steel 1071
Improvement of the transmission efficiency in electric vehicles by using double staggered helical gears with shortened teeth 1083
Analytical Method for Calculating the Nominal Tooth Root Stress in Worm Gear Shafts 1091
Developing CAE solutions for Robotics gears: Cycloidal and Strain Wave Gear Drives 1111
The effect of working surface deviation on transmission error in helical gears 1125
A study on the efficiency prediction of a gear bearing drive by means of mathematical modelling 1135
Backlash optimization via compatible gear couples on the assembly lines for planetary gearboxes 1147
Classifying plastic beveloid gear quality considering manufacturing errors 1159
Investigation of the electrical impedance of the gear mesh of helical gears in an industrial gearbox 1173
Development of Optimal Design Program for Macro-Geometry of Planetary Gear Set using Multi-Objective Optimization Algorithm 1181
A concept for comparison of new and aged lubricants in transmissions of electric vehicles and a method of oil aging on a test rig 1195
Parameter Based Definition of Eccentric Cycloid Gearings 1207
Model based NVH design: e-bike application 1229
Effect of overlap ratio on gear dynamic behavior and noise level 1239
Influence of misalignment of large cylindrical gears on contact pattern in operation 1257
Gear geometry, size and material influences not captured in ISO 6336 1267
Cross-correlation analysis among tooth profile and helix deviations 1273
A Novel Dynamic Modeling Method of High-Speed Thin-Rimmed Gear Transmission 1279
Sustainability
Recycling of carbon fiber reinforced plastics – State of the Art and Challenges 1287
Advanced biopolymer compounds for technical applications 1297
Tooth root strength
Prediction of tooth root fatigue failure of polymer gears for dry and oil lubricated contact and its comparison to experimentally obtained results 1301
The effect of gear manufacturing quality on the mechanical and thermal state of a plastic gear 1319
Improved Method for Validation of Root Stress in Polymer Gears 1333
Prediction of Gear Fatigue Life Considering Glass Fiber Orientation 1351
Analytical tooth root stress calculation for short fiberreinforced plastic gears 1361
Continuous prestressed reinforcement of plastic gear teeth and its effect on bending strength vs conventional reinforcement 1375
NVH
NVH performance of thermoplastic gears: modelling and measuring 1389
Evaluation of the NVH Characteristics of Gear Drives with Plastic Gears by the Forced Response Analysis 1403
Optimization of the vibrational behavior of ZI crossed helical gears with a plastic wheel and a steel worm 1419
Manufacturing and operating properties
Influence of the injection molding process on the tooth deflection of plastic gears during operation 1435
Plastic Gears: Investigation on Noise and NVH Behavior 1449
New generation in plastic gear technologies 1461
Gear geometry and calculation
A non-restrictive approach of gear geometry calculation for plastic gears 1469
Applicability of classic analytical calculation approaches for the design of plastic gears 1483
Crossed helical gears – simulative studies and experimental results on non-involute geometries 1499
Performance and validation of plastic gears
Evaluation of specialty polymer performances in gear applications and the bias between modeling and testing approaches 1515
Experimental Verification of High-Performance Polymer Gears in an Electric Vehicle Powertrain 1533
Influence of plastic-metal-pairings on the lifetime of gears 1535
Tribology and thermal behavior
Reduction of root and flank temperature using a hybrid polymer-metal rack 1547
In-situ experimental methods for measuring tooth meshing displacements and wear during polymer gear tests using a high-speed camera with microscopy optics 1563
Gear Production 2023
Innovations in gear production
Complete machining of complex transmission parts 1581
Advancing to The Next Level – Cost Efficient Roll-Inspection: Back from End-of-Line NVH to Skiving Process 1591
Software in gear production
Building a software toolchain for automated mass-customization of specific end-use gear unit parts using AM-driven design guidelines 1607
Securing the Quality Chain by the Networking with the Gear Suppliers 1617
Generation Method of Polygonal Shaped Work Pieces Based on Gear Meshing Theory 1631
Additive manufacturing
Spur Gear Teeth Reconstruction via Direct Laser Deposition 1641
Binder Jetting in Gears – Process Design and Tooth Bending Strength for Gears made of 17-4PH 1665
Indirect Selective Laser Sintering: Modeling and analysis of surface densification by shot peening 1681
Materials in gear production
Estimation of brittleness of CCH-steel via measurement of micro-VH and simultaneous FWHM distribution 1699
Investigation of the machinability of different quenched and tempered steels for the alternative process chain of planetary pinions in wind turbine gearboxes 1713
Investigating different nodular graphite irons for the application of gears – a step towards standardization by using reasonable quality
Modeling and tracing of gear manufacturing processes
Gear Skiving with Minimum Twist Errors 1749
The next level of axial forming for a sustainable component and process chain design 1765
Enhancing gear performance through advanced mass finishing and DEM simulation 1777
Gear metrology
Quality inspection of special geometries measured with computed tomography – Evaluation of involute cylindrical gears according to ISO 1328-1 1787
Large gear metrology at PTB 1803
Optimization of product quality and manufacturing processes in real-time with vibration analysis 1821
Sustainability and surface integrity
Tooth Root Burnishing in the Kinematics of Gear Skiving 1829
Surface integrity of 20MnCr5 pinion gears manufactured through laser powder bed fusion 1845
Manufacturing processes
The Magic Cutter – An economical solution for bevel and hypoid gear production based on the modular principle 1859
Application-oriented research on internal generating polishing 1863
Marker-Free, Single Item Traceability in Gear Wheel Production Based on Inherent Surface Patterns 1877
Keywords: verlustarme Getriebe, Risswachstum, Stirnrad, Planeten Getriebe, Lebensdauer Vorhersage, Maschenweite Synchronisierung, Reibungskoeffizient, Lastverteilung, Schmierung, Ölfluss Simulation, schlaues Getriebe, Re-X, low-loss-gears, tooth root load, fatigue strenght, spur gear, crack groth, root life prediction model, planetary gear, mesh phasing, friction coefficient, ISO 6336, E-Axle applications, load distribution, NVH, multi stage gear trains, lubrication, planetary gearbox, meshing contact, oil flow simulation, CFD, smart gear
* Der VDI-Mitgliedsrabatt gilt nur für Privatpersonen