Gleitlager aus dem 3-D-Drucker
Wie viel Potenzial in additiven Fertigungsverfahren steckt, zeigt der Kunststoffteilehersteller Igus. Der Entwickler und Produzent von Energieketten und Gleitlagern aus verschleißfesten Kunststoffen nutzt die Technik nicht nur, um Prototypen herzustellen. Er bietet sie seit Kurzem seinen Kunden auch als Service an. Außerdem vertreiben die Kölner ihre tribologischen Werkstoffe inzwischen auch für 3-D-Drucker.
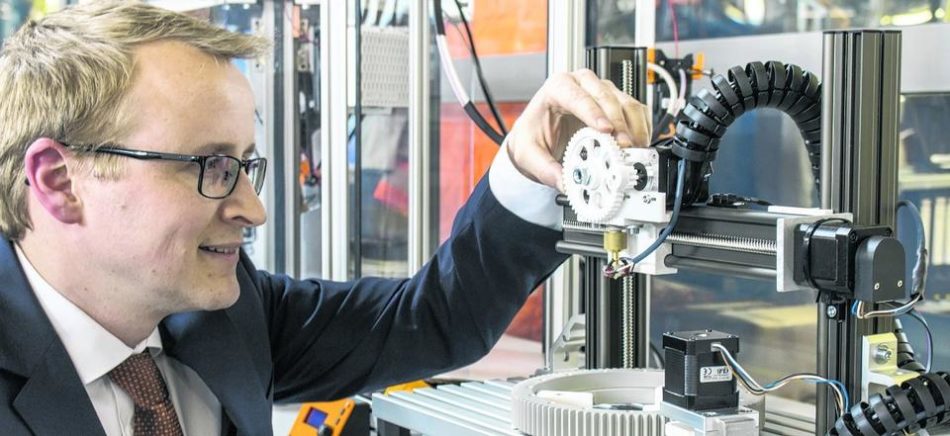
Foto: Igus
Noch stehen die 3-D-Drucker, die Igus nach und nach angeschafft hat, eher unscheinbar am Rande der Fabrikhalle am Standort Köln-Lind. Doch das könnte sich schnell ändern. Davon ist Tom Krause überzeugt. Der Maschinenbauingenieur hat bei Igus den Einsatz des 3-D-Drucks vorangetrieben. „Immer mehr Unternehmen erkennen die Vorteile der additiven Fertigungstechnik“, sagt Krause. „Und mit unserem Druckservice können sie die neue Technik nutzen und testen, ohne selbst in Maschinen investieren zu müssen.“
Auf dem Markt für Gleitlager aus verschleißfesten Kunststoffen ist Igus nicht allein. Wettbewerber sind u. a. GGB Bearing Technology, Heilbronn, Schaeffler Technologies, Herzogenaurach, oder SKF, Schweinfurt.
3-D-Druck als Service ist ein Trend. Seit Kurzem ist auch das US-Unternehmen Proto Labs in seiner Niederlassung in Mosbach dabei. Bei dem Stereolithografieverfahren wird ein punktgenauer Ultraviolettlaser eingesetzt, der die Oberfläche von flüssigem Duroplast verfestigt. Proto Labs plant, 2016 zwei weitere Verfahren – das selektive Lasersintern (SLS) sowie das Lasersintern direkt auf Metall (DMLS) – anzubieten.
Aber auch im Hinblick auf die eigene Produktion gewinnen die 3-D-Drucker bei Igus an Bedeutung. Für den Tribo-Spezialisten gehört eine hohe Verfügbarkeit seiner über 100 000 Kunststoffprodukte zur Geschäftsstrategie. „97 % unserer Bauteile können wir innerhalb von 24 Stunden ausliefern“, so Frank Blase, Chef des Familienunternehmens. Möglich machen das mehr als 250 Spritzgießmaschinen in Köln-Lind. „Mit der Investition in die additive Fertigung können wir nun auch sehr spezielle Kundenwünsche realisieren“, so der Geschäftsführer.
Vor allem Gleitlager müssten regelmäßig den speziellen Anforderungen der Kunden angepasst werden, sagt Krause. „Mit den 3-D-Druckern wird der Prozess deutlich verkürzt und die Kunden können die Produkte in der Praxis testen, bevor sie in größeren Stückzahlen gefertigt werden“, so der Maschinenbauingenieur.
Igus beschäftigt sich schon länger mit der alternativen Fertigungstechnik. Zunächst wurden die 3-D-Drucker ausschließlich zur Herstellung von Prototypen und kleinen Serienbauteilen für den eigenen Bedarf eingesetzt. „Meine Kollegen in der Werkstoffentwicklung nutzen die Automaten vor allem, um Prototypen aus selbstentwickelten Tribo-Kunststoffen zu fertigen und diese Bauteile dann anschließend ausgiebig zu testen“, sagt Krause.
Bisher eignen sich drei der rund 40 Igus-Werkstoffe auch für den 3-D-Druck. „Sie ermöglichen es, Teile mit einer deutlich höheren Verschleißfestigkeit zu fertigen, als dies mit dem in der Industrie oft verwendeten Standardwerkstoff ABS (Acrylnitril-Butadien-Styrol) möglich ist“, sagt Krause. Bauteile aus dem eigenen Werkstoff „Iglidur I180-PF“ beispielsweise seien bis zu 50-mal abriebfester als mit ABS gefertigte Teile.
ZAHL DER TRIBO-WERKSTOFFE, DIE DRUCKFÄHIG SIND, SOLL ERWEITERT WERDEN
„Wir arbeiten daran, das Angebot an verschleißfesten Polymeren zu erweitern und hoffen, bereits in wenigen Monaten weitere Sorten anbieten zu können“, so der Produktmanager für den 3-D-Druck.
Der Maschinenpark für die additive Fertigung in der Kölner Fabrik besteht zurzeit aus drei Geräten, die sich vor allem in ihrer Leistungsfähigkeit unterscheiden.
Der „Ultimaker 2“ vom gleichnamigen Hersteller baut auf Basis dünner Filamente feinste Strukturen auf. Die Schichtdicke beträgt lediglich 0,02 mm.
Etwas grober aber dafür schneller arbeitet der „Evolizer“ der österreichischen Firma Evotech. Mit ihm können in kurzer Zeit Prototypen, Anschauungsmodelle oder Kleinserien von Produkten hergestellt werden.
Seit etwa einem halben Jahr sammelt Igus zudem Erfahrungen mit dem „Freeformer“, einer Neuentwicklung des Kunststoffmaschinenbauers Arburg. Die Maschine ist besonders flexibel einsetzbar. Ein weiterer Vorteil besteht darin, dass alle Polymere als Granulat verarbeitet werden können – in der Grundform also, in der Igus mit seinen Spritzgussmaschinen jahrzehntelange Erfahrung hat. Der „Freeformer“ ermöglicht es zudem, ein Produkt mit zwei verschiedenen Kunststoffen auszubauen. Das heißt: Es können mithilfe von Stützmaterial, das sich später auflöst, auch kompliziertere Bauteile gedruckt werden, oder auch Gleitlager, die zunächst aus einem normalen ABS generiert werden und bei denen nur die Gleitflächen mit dem eigenem abriebfesten Tribo-Werkstoff gefertigt werden.
Um die Abwicklung der Fertigung im 3-D-Druck so einfach wie möglich zu gestalten, arbeitet das Unternehmen dran, den Bestellvorgang in seine Webseite zu integrieren. „Kunden können bald die Konstruktionsdaten ihrer Bauteile auf die Homepage laden und die Ermittlung der Preise und Berechnung der Lieferzeiten erfolgt dann automatisch nach einem Mausklick“, erläutert Krause.