Hightech-Spiegel aus dem Tintenstrahl-Drucker
Forschenden aus Karlsruhe ist es gelungen, hocheffiziente Spiegel, sogenannte Bragg-Reflektoren, kostengünstig mithilfe von Nano-Tinten herzustellen. Anwendungsfelder gibt es viele – etwa in Lasertechnik, Werbung und Sensorik.
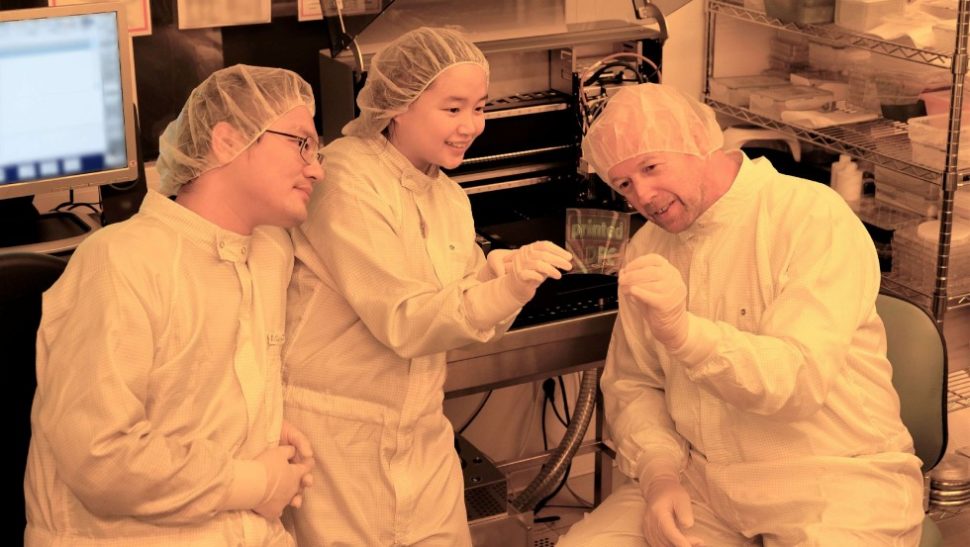
Foto: Jan Fessler/KIT/LTI
Wer glaubt, sich in seinem Badezimmerspiegel in ganzer Schönheit betrachten zu können, irrt. Tatsächlich sieht er nämlich nur gut 90 % seiner strahlenden Pracht. Der Rest des einfallenden Lichts verbleibt im Glas. Bragg-Spiegel sind da deutlich besser: Sie kommen auf eine Reflektivität von annähernd 100 %. Doch das ist nicht alles: je nach Aufbau schaffen sie es, dass ausschließlich solche Lichtfarben reflektiert werden, die vorab ausgewählt wurden – andere Wellenlängen gehen einfach durch. Umgekehrt können die Bauteile auch so konstruiert werden, dass sie nur bestimmte Wellenlängen passieren lassen. Sie fungieren dann als eine Art von Lichtfilter. Hergestellt werden sie bisher in teuren Vakuumanlagen, etwa mittels thermischen Aufdampfens. Forschende am Karlsruher Institut für Technologie (KIT) schaffen das jetzt mit einem Tintenstrahldrucker.
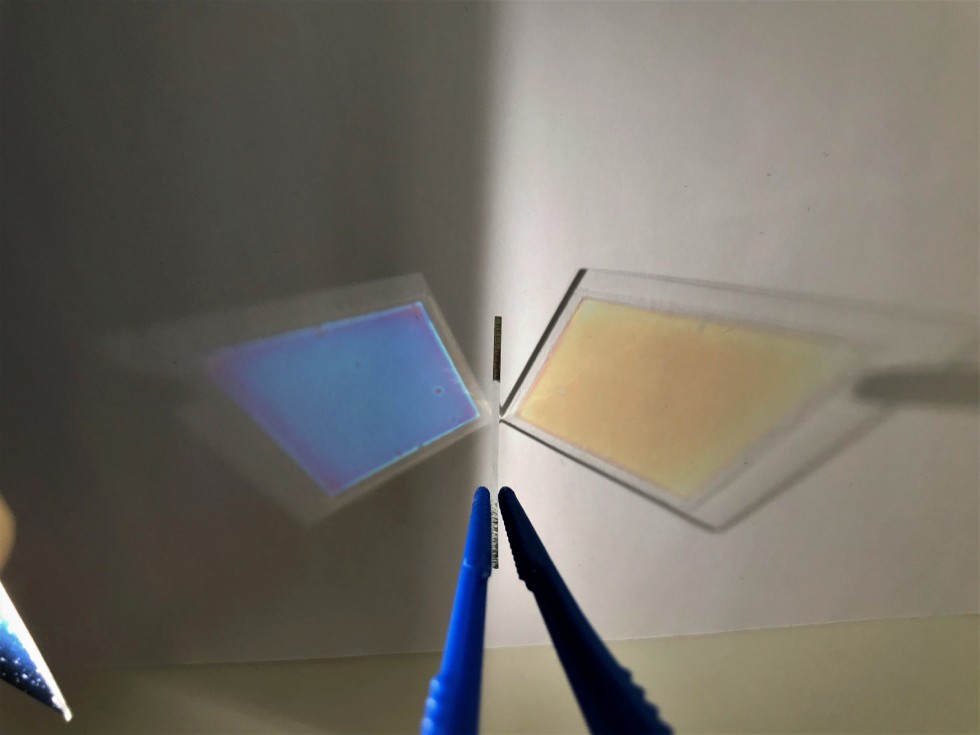
Wie ist das möglich? Zum besseren Verständnis erläutert Teamleiter Uli Lemmer zunächst den Aufbau und die Funktion von (Bragg-)Spiegeln: „Licht wird immer dann reflektiert, wenn es auf eine Grenzschicht trifft, die zwischen zwei Materialien mit unterschiedlichem Brechungsindex liegt.“ Im Alltag könne das jeder an simplen Fensterscheiben beobachten. Material 1 wäre in diesem Fall die Umgebungsluft, Material 2 wäre das Glas. Schon hier käme es zu schwachen Reflektionen. Der Großteil des Lichts gehe aber durch die Scheibe hindurch.
Die Zauberformel: „konstruktive Interferenz“
„Bragg-Spiegel bestehen aus etlichen Materialschichten“, so der Direktor des Lichttechnischen Instituts am KIT. „Sie haben also entsprechend viele Grenzschichten. Die Kunst ist nun, die einzelnen Materialschichten exakt so dick auszuführen, dass alle Lichtwellen einer bestimmten Frequenz, die an den einzelnen Grenzschichten reflektiert werden, konstruktiv interferieren.“
Vereinfacht ausgedrückt: Alle „Wellenberge“ und „Wellentäler“ der reflektierten Lichtfarbe sollen sich überlagern – egal aus welcher Tiefe des Spiegels sie kommen. Dabei gilt: Je mehr Grenzschichten aufgebaut werden, desto weniger Licht geht im Spiegelinneren verloren – desto höher ist also die Spiegelungsrate. „Schon bei zwanzig Schichten erreichen wir eine Reflektivität von über 99 %“, so der Optoelektroniker.
Üblich sind Schichtstärken zwischen 50 nm und 130 nm
Die einzelnen Materialschichten müssen sehr dünn sein. Genaugenommen sollte ihre optische Weglänge etwa einem Viertel der Wellenlänge des zu reflektierenden Lichts entsprechen. „Üblich sind also Schichtstärken zwischen 50 nm und 130 nm“, so der Professor. „Wenn rotes Licht reflektiert werden soll, dann müssen die Schichten also etwas dicker sein als bei blauem Licht.“
Zum Aufbau der flachen Schichten nutzen die Forschenden einen Tintenstrahldrucker. „Er arbeitet im Prinzip genau wie die Desktopgeräte in Büros – nur präziser“, erklärt Lemmer. „Wir setzen auf ein piezo-gesteuertes Drop-on-Demand-Verfahren.“ Die Tintenausbringungsmenge sei also auch auf kleiner Fläche sehr genau definierbar.
Die Tinten bestehen aus einem Lösungsmittel, in das Partikel mit einem Durchmesser von weniger als 10 nm dispergiert sind. „Bei unserem ersten Spiegel nutzten wir als Material 1 Titandioxid, wie man es aus weißer Wandfarbe kennt“, so der Karlsruher. „Als Material 2 kam Polymethylmethacrylat zum Einsatz – besser bekannt als Plexiglas.“
Besonders kniffelig war nach Angaben des Wissenschaftlers das Erzeugen einer sauberen Grenzschicht: „Zwischen den letzten Tropfen von Material 1 und den ersten Tropfen von Material 2 darf es niemals eine Vermengung geben.“ Gelöst wurde dieses Problem mit einer UV-Flashbelichtung. Sie sorgt für eine schnelle Vernetzung der ausgebrachten Polymere.
Genutzt werden Bragg-Spiegel bisher u. a. in Kamerasystemen, Sensoren und Mikroskopen. Besonders oft findet man sie auch dort, wo Laserstrahlung eingesetzt wird. Hier kämen normale Spiegel nämlich schnell an ihre Grenzen. Hintergrund: Zuviel der hohen Lichtenergie bliebe in ihrem Inneren, statt reflektiert zu werden – lokale Zerstörung durch Überhitzung wäre die Folge.
Die Trümpfe der additiven Fertigung werden ausgespielt
Die gedruckten Spiegel erweitern das bisherige Einsatzspektrum: „Wir können die einzelnen Schichtdicken exakt bestimmen und problemlos variieren. Die Reflektivität und Durchlässigkeit kann also individuell eingestellt werden“, so Lemmer. „Dabei spielt es verfahrensbedingt keine Rolle, ob wir lediglich einen Spiegel oder gleich 1000 Exemplare herstellen.“ Bei der Formwahl gebe es keine Limitierungen.
„Außerdem können wir Muster drucken“, so der Professor. „Eine Materialschicht kann also an der einen Stelle höher sein als an der anderen.“ Ergebnis sei ein Spektrometer. „Wir haben somit ein Werkzeug, mit dem vergleichsweise einfach Hyperspektralkameras gebaut werden können.“ Sie böten sowohl eine räumliche als auch eine spektrale Auflösung. „Sowas lässt sich mit Aufdampfen oder Sputtern nur schwer herstellen.“
Großflächige Reklame, energieeffizient leuchtend
Eine weitere Besonderheit: „Neben Glas können wir auch Kunststoffe bedrucken, etwa PET-Folien“, erklärt der 58-Jährige. „Es lassen sich also mechanisch flexible Spiegel herstellen.“ Deren Größe sei skalierbar. „Möglich ist eine Rolle-zu-Rolle-Produktion. Die Druckfläche kann dabei auf viele Quadratmeter ausgedehnt werden.“
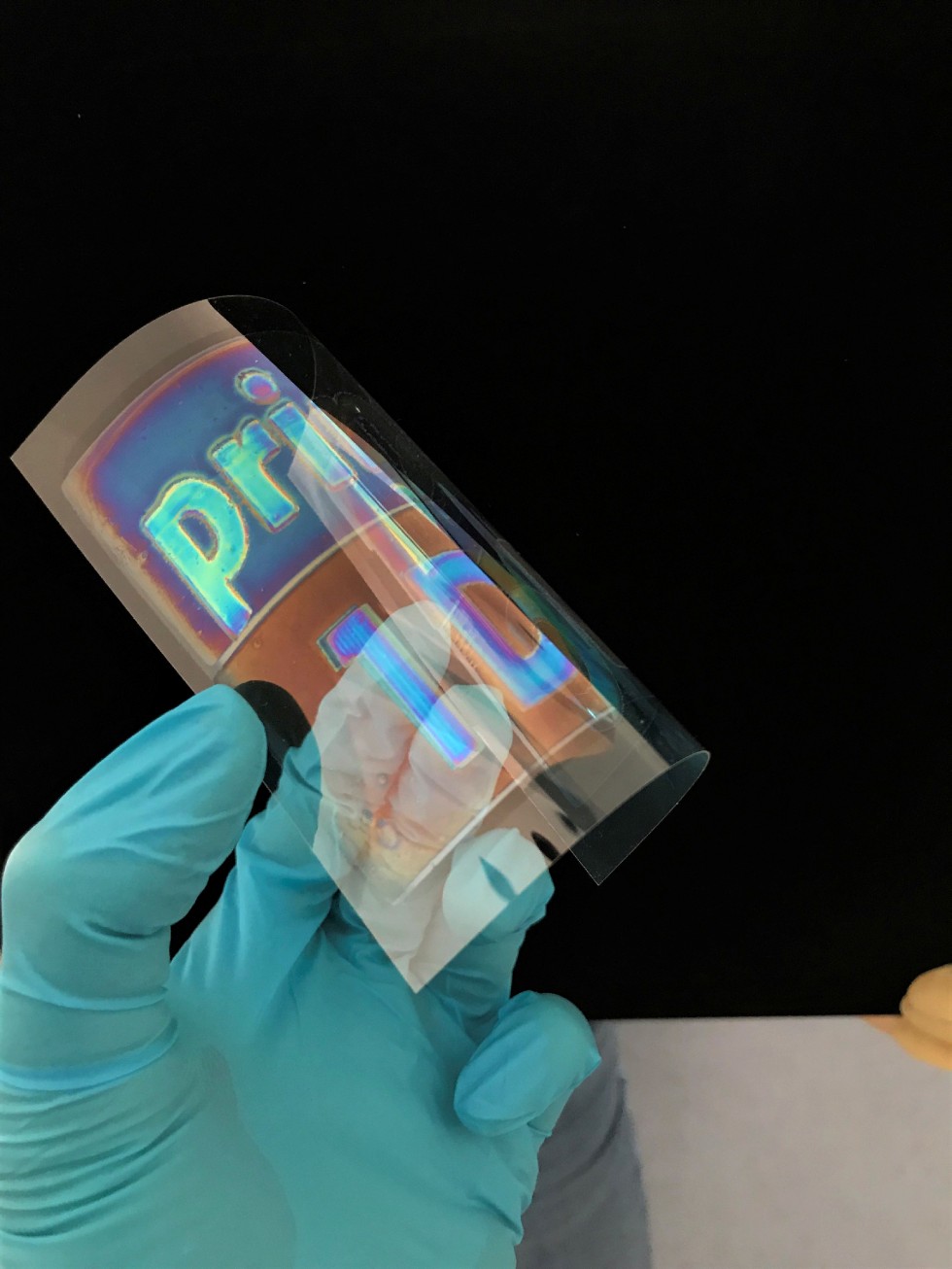
In der Praxis könnten solche „Riesenspiegel“, die am Tag in schillernden Farben leuchten, u. a. für Info- oder Werbedisplays genutzt werden. „Es ließen damit auch großflächige Photovoltaikanlagen bekleben, ohne dass zu viel Licht absorbiert wird“, so Lemmer. „Die reflektierte Farbe ist frei wählbar. Wenn Sie beispielsweise das VDI-blau an Ihrer Bürofassade wünschen: kein Problem!“
Deutschlands größter schwimmender Solarpark
Wie groß ist der Markt für die gedruckten Spiegel? Und wie werden die Schichtdicken berechnet? Antworten auf diese und weitere Fragen (sowie das gesamte Interview) hören Sie in der 49. Folge des Podcasts „Druckwelle“.
Hier wird Ihnen ein externer Inhalt von Podigee angezeigt.
Mit der Nutzung des Inhalts stimmen Sie der Datenschutzerklärung
von youtube.com zu.
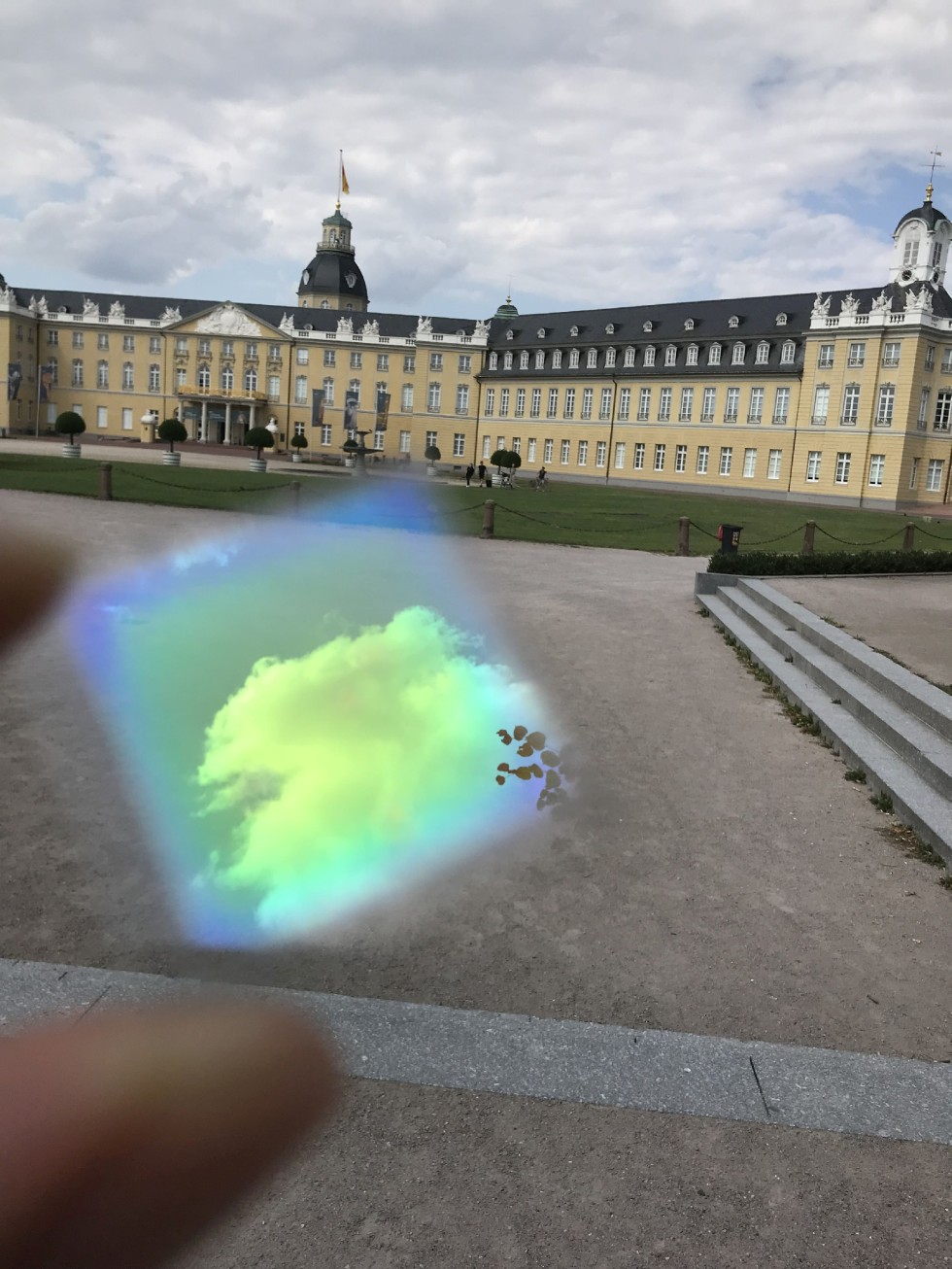