Mit Schallgeschwindigkeit zum Bauteil
Beim Kaltgasspritzen werden Metallpartikel so stark beschleunigt, dass sie sich beim Aufprall verformen und aneinander haften.

Foto: Impact Innovations
Das Internetvideo des australischen Start-ups „Spee3D“ ist ziemlich cool. Die präsentierte Technik ist es auch: Es geht um Kaltgasspritzen. Der Zuschauer sieht einen Mann in eine Werkshalle schleichen. Er vergewissert sich, dass er unbeobachtet ist. Heimlich erweckt er eine große Maschine zum Leben. Auf ihrem Display wählt er eine CAD-Datei aus. Sofort setzt sich ein Roboterarm zu mitreißender Musik in Bewegung. An dessen Ende ist ein Platte montiert. Auf ihr wächst nun, wie von Geisterhand, ein Metallkörper heran. Er hat die Grobstruktur eines Golfschlägerkopfes. Nach wenigen Minuten ist das Kupferteil fertig. In einem Bearbeitungszentrum bekommt es den letzten Schliff. Fertig! Der Mann lächelt – und locht locker ein.
Was die Australier damit sagen wollen: Ihre Maschine kann in kürzester Zeit massive Metallteile erschaffen – ohne dass eine Sand- oder Gussform nötig wäre. Es müsse auch nicht – unter hohem Material und Energieaufwand – aus dem Vollen gefräst werden.
Geschäftsführer und Mitgründer Byron Kennedy erläutert Details des Verfahrens: „Es stammt ursprünglich aus dem Militärbereich. US-Soldaten nutzten es schon vor zehn Jahren, um Reparaturen an ihren Fahrzeugen durchzuführen.“ Beispielsweise seien gealterte Getriebegehäuse zunächst von Rost befreit und anschließend mittels manuell geführter Kaltgaspistole neu beschichtet worden. „Das Funktionsprinzip des Werkzeugs ist relativ simpel: Im Inneren wird ein Prozessgas aufgeheizt und durch Expansion in einer Lavaldüse auf Überschallgeschwindigkeit beschleunigt. In diesen Gasstrom werden Metallpartikel eingebracht.“ Sobald sie auf eine Oberfläche träfen, würden sie sich verformen und eine fest haftende Schicht bilden – ohne zuvor aufgeschmolzen worden zu sein. Daher der Begriff „Kaltgasspritzen“.
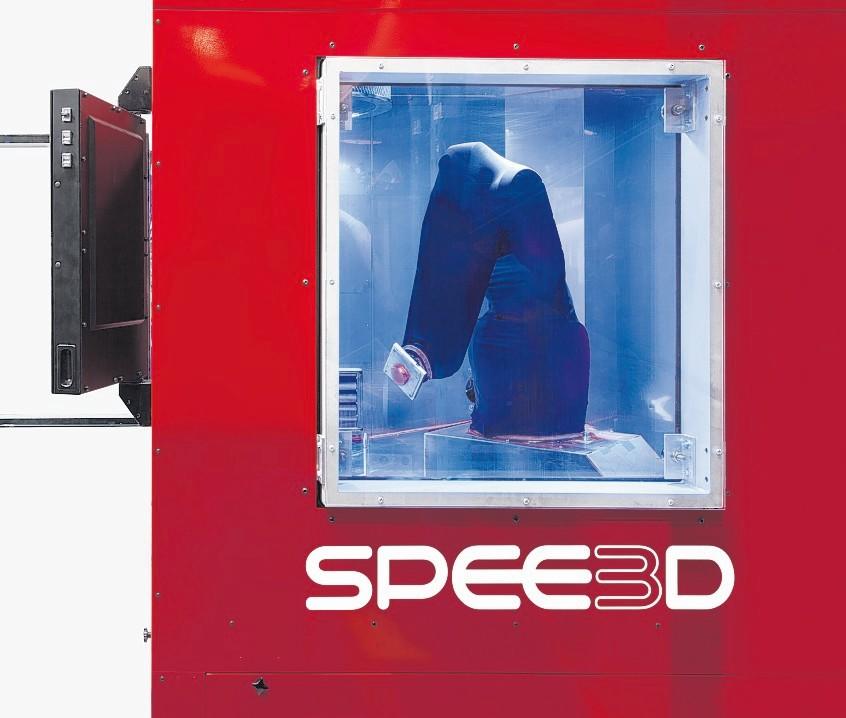
„Was bisher keinen anderen Unternehmen gelang, ist der gezielte Aufbau von dreidimensionalen Teilen“, behauptet Kennedy. „Dank unserer Software ist das nun aber problemlos möglich. Sie übersetzt 3D-CAD-Daten in Armbewegungen eines Sechs-Achs-Roboters.“ Die Maschine führe also eine Bauplattform präzise über die Mündung der Düse. „Schicht für Schicht entsteht so das Bauteil.“ Die Dichte betrage mindestens 98 %.
Aktuell verarbeitet der 3-D-Drucker der Australier nur Kupfer und Aluminium. Hier sind die Parameter vergleichsweise einfach zu beherrschen. Bei dem Leichtmetall genügt beispielsweise eine Prozesstemperatur von 450 °C, 30 bar Druck und eine Partikelgeschwindigkeit von 660 m/s.
Das Einsatzgebiet der Maschine sieht Kennedy in der Großindustrie. „Wir haben Vorteile dort, wo es um die schnelle und günstige Produktion von einfachen Konstruktionen in geringer bis mittlerer Stückzahl geht.“ Sobald Zehntausende gleicher Teile benötigt würden, sei der Druckguss günstiger.
Die Maschine der 2015 gestarteten Firma kostet 550 000 € oder 15 000 € Monatsmiete. Gegenüber Pulverbettdruckern hat sie laut Kennedy zwei Vorteile: Sie verarbeite einfachstes Standardmetallpulver – die Korngrößenverteilung spiele kaum eine Rolle. Und sie produziere die Teile ungleich schneller – der Golfschlägerkopf sei nach gut 10 min fertig. „Laserschmelzanlagen sind auf fließfähiges, homogenes Spezialmaterial angewiesen und benötigen für Teile oft sehr viele Stunden“, so der 43-Jährige.
Was er nicht sagt: Der Vergleich hinkt ein wenig. Denn das Produkt aus dem Laserdrucker ist endkonturnäher, braucht weniger Nachbearbeitung und hat höherwertige Materialeigenschaften. Außerdem lassen sich im Pulverbett Formen realisieren, die keine Kaltgasdüse der Welt je hinkriegt, etwa innenliegende Leichtbaustrukturen.
Trotzdem hat die Technik ihre Daseinsberechtigung – zumal sie nicht auf die vergleichsweise einfach zu handhabenden Metalle wie Kupfer und Aluminium beschränkt ist. Das beweist die Impact Innovations GmbH aus Haun/Rattenkirchen. Die Bayern treten beim Marketing deutlich zurückhaltender auf. Dabei sind sie den Australiern in einigen Details weit voraus. „Mit unserer Kaltgaspistole verarbeiten wir fast alle Metalle und ihre Legierungen, also etwa auch Stähle und Titan“, erklärt Co-Geschäftsführer Peter Richter. „Ausnahmen sind nur Molybdän und Wolfram.“
Meist seien dazu höhere Temperaturen und mehr Druck nötig. „Statt Luft setzen wir in aller Regel Stickstoff als Prozessgas ein“, erklärt Managementkollege Leonhard Holzgassner. „Es lässt sich leichter komprimieren und verursacht überdies keine Oxidationsprobleme. Wir erhitzen es auf 1100 °C und steigern den Druck auf bis zu 50 bar.“ Der Gasstrom erreiche dann etwa fünffache Schallgeschwindigkeit. Die Partikel seien vor dem Aufschlag mit etwa 1000 m/s unterwegs. „Wenn wir den Stickstoff durch Helium ersetzen, erreicht der Gasstrom sogar 15-fache Schallgeschwindigkeit“, so der 33-Jährige.
Generell gilt: Die Partikelgeschwindigkeit muss dem Spritzmaterial angepasst werden. Sie muss ausreichen, um Trägermaterial und Pulver miteinander zu verbinden. Sie darf aber nicht so hoch sein, dass Substrat abgetragen wird. Impact Innovation liefert seinen Kunden deshalb neben der Pistole auch qualifiziertes Pulver und Prozess-Know-how. Zum Hardwarepaket des 2010 gegründeten Unternehmens zählt außerdem ein Kühlsystem und eine Pulvermanagementeinheit. Die Kosten bewegen sich – je nach Ausstattung – zwischen 160 000 € und 320 000 €.
Was die Bayern nicht liefern ist die Mechanik, die das Werkstück und/oder die Pistole bewegt. Diesbezüglich arbeiten sie mit Herstellern von Robotern und Werkzeugmaschinen zusammen. „Unsere Pistole könnte auch in die Spee3d-Maschine integriert werden“, so Holzgassner. „Oder in handelsübliche 5-Achs-Bearbeitungszentren.“ Die Größe der jeweils gewählten Lösung bestimme die Größe des Bauraums.
Diese Skalierbarkeit sieht Richter als einen wesentlichen Vorteil des 3-D-Kaltgasspritzens. „Nutzer von Pulverbettmaschinen können Teile von maximal 1 m3Volumen herstellen. Wir bieten – je nach Maschinenumgebung – locker ein Vielfaches.“ Auch sei der Materialauftrag ungleich höher. „Bei Edelstahl schaffen wir rund 10 kg pro Stunde“, so der 34-Jährige. Zum Vergleich: Beim Laserschmelzen liegt die Aufbaurate bei durchschnittlich 0,3 kg/h, beim Laserauftragsschweißen bei etwa 4 kg/h. Weiterer Vorteil des Kaltgasspritzens: Da die Partikel nicht aufgeschmolzen werden, bleiben die Spannungen im Bauteil gering. Außerdem lassen sich verschiedene Metalle in einem Bauteil kombinieren.
Der Kundenkreis von Impact Innovations ist groß. Die Technologie findet beispielsweise Einsatz in der Luft- und Raumfahrt, der Elektroindustrie und auch im Haushaltswarenbereich. Richter bringt es auf den Punkt: „Wir machen alles – von Bratpfanne bis Rakete.“