Tröpfchenweise zum Metallteil – Werkzeugmaschinenbauer steigt mit eigenem Konzept in den Metaldruck ein
Mit dem „Liquid Metal Printing“-Verfahren will der Werkzeugmaschinenhersteller Grob in der additiven Fertigung Fuß fassen. Die Bayern versprechen präzise Bauteile in kurzer Zeit.

Foto: Grob Werke
Das ist gleich doppelt bemerkenswert: Ein Unternehmen, weltweit bekannt für seine spanenden Werkzeugmaschinen, steigt in den 3D-Druck ein – und setzt dabei auf eine fast unbekannte Technologie. Die Rede ist von der Grob-Group aus Mindelheim. Sie hat eine Maschine zum „Liquid Metal Printing“ (LMP) entwickelt.

Wie es zu dieser außergewöhnlichen Paarung kam, weiß Johannes Glasschröder, Teamleiter für additive Fertigung: „Die Automobilindustrie, in der unsere Maschinen vielfach eingesetzt werden, verändert sich gerade massiv. Also haben wir nach zusätzlichen Geschäftsinhalten gesucht. Dabei haben wir mit vielen potenziellen sowie aktuellen Anwendern der additiven Fertigung gesprochen.“ Ergebnis: „Die Nutzer der weit verbreiteten Pulverbetttechnologien beklagten regelmäßig das komplizierte Pulverhandling, die geringen Aufbauraten und das notwendige Spannungsarmglühen.“ Zwar sei die Oberfläche und Endkonturnähe der Bauteile gut, das spiele aber bei vielen Anwendern gar keine große Rolle, da ohnehin stets nachbearbeitet werden müsse – etwa an Funktionsflächen.
Vergleichsweise genau und schnell
„Wer hingegen Bauteile per Auftragsschweißen herstellt, bedauerte in unserer Marktstudie die fehlende Genauigkeit und den sehr großen Nachbearbeitungsaufwand.“ Stets müsse großflächig Metall wieder abgetragen werden. „Daraus haben wir gefolgert, dass das Liquid Metal Printing die richtige Technologie für uns ist“, so Glasschröder.
Das Prinzip des LMP erklärt der promovierte Maschinenbauer so: „Mithilfe eines Druckkopfes erzeugen wir im Drop-on-Demand-Prinzip flüssige Aluminiumtropfen. Diese fallen auf einen x/y-Kreuztisch, der mittels Kugelspindelantrieb verfahren wird.“ Aufbauten in der z-Achse würden möglich durch das Anheben des Druckkopfs.
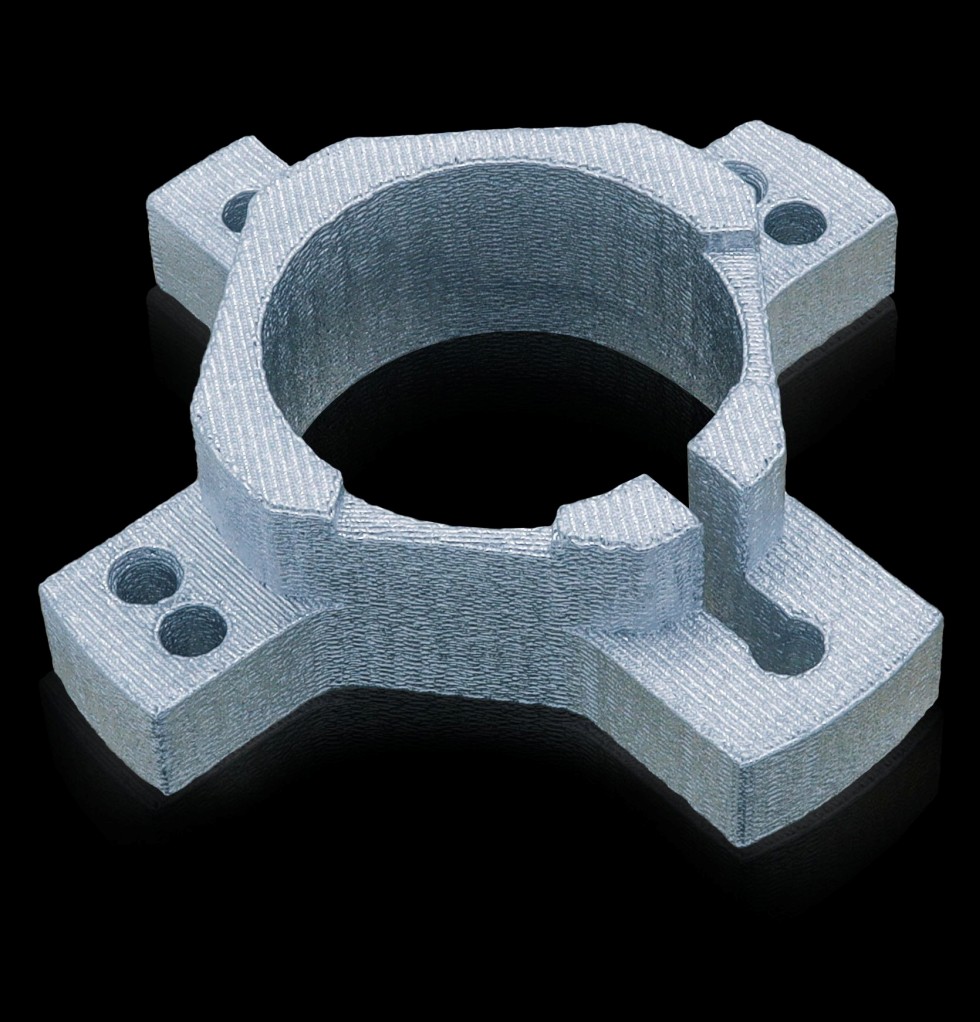
Die Anlage, die sogenannte GMP 300, ist äußerst massiv konstruiert. Hintergrund: Der Kreuztisch muss inklusive Heizung und aufliegendem Bauteil hochdynamisch bewegt werden können, ohne dass es zu Schwingungen kommt. Die inertisierte Baukammer misst 300 mm x 300 mm x 300 mm.
Alles aus der Welt der Technik
Angebot wählen und sofort weiterlesen
- Alle Beiträge auf vdi-nachrichten.com
- Monatlich kündbar
Oder werden Sie VDI-Mitglied und lesen im Rahmen der Mitgliedschaft Vn+.