Werkzeuge mit KI und Lasertechnik reparieren
Fraunhofer-Forschende haben eine KI entwickelt, die den Prozess des Laserauftragschweißens steuert. Um die Verschleißfestigkeit der gefertigten Bauteile zu erhöhen, werden Wolframkarbidpartikel in die Schmelzzone eingeblasen.
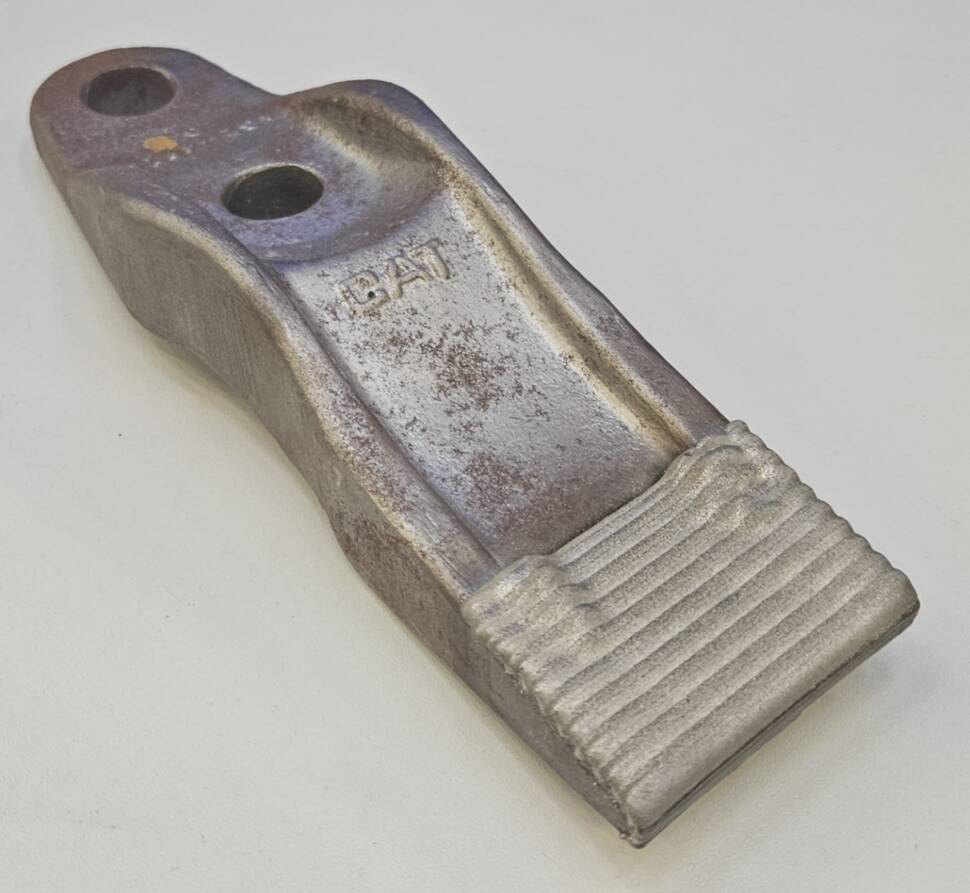
Foto: Fraunhofer ILT
Werkzeuge, die beispielsweise im Bergbau genutzt werden, unterliegen einem enormen Verschleiß. Baggerschaufeln mit verschlissenen Zähnen oder stumpf gewordene Meißel werden in der Regel eingeschmolzen und durch neue ersetzt. Das ist teuer und nicht ressourcenschonend.
Eine Alternative hierzu ist das Laserauftragschweißen (Laser Material Deposition, LMD). Dabei wird Metallpulver in ein laserinduziertes Schmelzbad geschossen. Schichtweise entstehen so neue Bauteile – oder bestehende Werkzeuge werden repariert. Beispielsweise lässt sich die ursprüngliche Kontur eines abgeschliffenen Baggerzahns oder einer Bohrkrone exakt wieder herstellen.
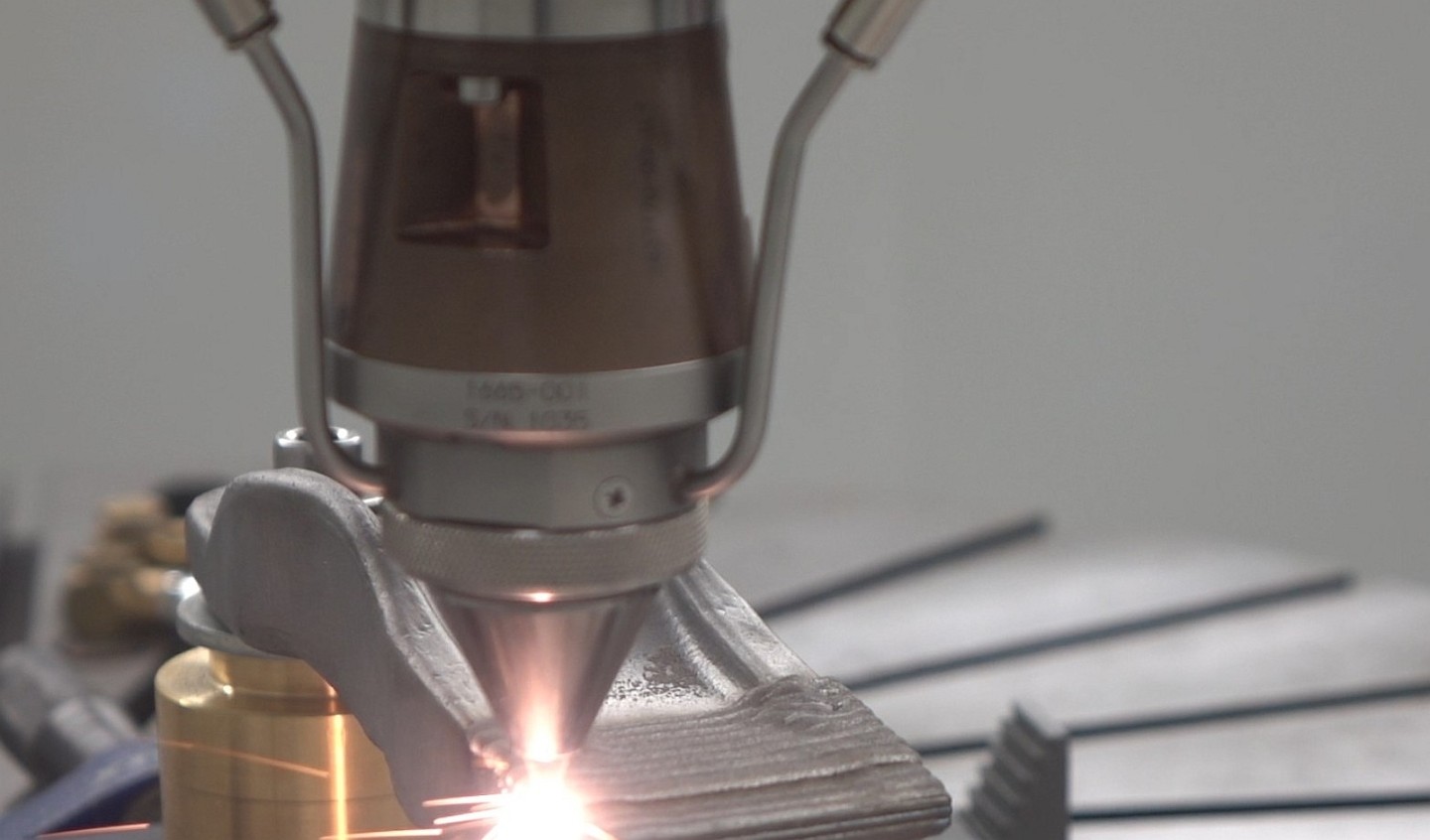
Im Projekt AI-SLAM („Artificial Intelligence Enhancement of Process Sensing for Adaptive Laser Additive Manufacturing“) kombinieren Forschende des Fraunhofer-Instituts für Lasertechnik (ILT) in Aachen die Produktionstechnik mit künstlicher Intelligenz (KI). „Ziel des Projekts war die Automatisierung aller Schritte: von der Aufnahme der Defekte über die Planung der Bahnen und Parameter beim Schweißen bis zur Umsetzung und Qualitätskontrolle“, so Max Zimmermann, Projektleiter Beschichtung LMD und Wärmebehandlung in der Abteilung Laserauftragschweißen am Fraunhofer ILT.
Lesetipp: Hartmetall 3D-gedruckt – Werkzeugbau am Limit
Partner des Vorhabens sind der National Research Council of Canada, die McGill University in Montreal sowie Unternehmen wie der KI-Spezialist Braintoy in Calgary und Apollo Machine and Welding aus Alberta. Auch der Softwareentwickler BCT aus Dortmund ist beteiligt.
Ultrahartes Wolframkarbid verlängert Standzeit
Bei der Reparatur gleitet die Laseroptik in einer vorberechneten Bahn über die Oberfläche des Werkzeugs. Dabei wird Edelstahl bei circa 1300 °C geschmolzen und aufgetragen. Gleichzeitig blasen Düsen Wolframkarbidpartikel darauf. Diese verbinden sich mit dem geschmolzenen Edelstahl und bilden nach dem Abkühlen eine ultraharte Schicht auf dem Werkzeug – sie dient sowohl als Verschleiß- als auch als Korrosionsschutz.
Lesetipp: Wolfram-Teile aus dem Drucker
Eine Herausforderung für das Forschungsteam bestand darin, das optimale Mischungsverhältnis aus Wolframkarbidpartikeln und Stahl zu finden. „Zu viele Partikel machen die Schicht spröde und rissig, bei zu viel Edelstahl ist die Schicht zu weich und schnell wieder abgenutzt“, erklärt Zimmermann. Außerdem muss die Laserleistung so eingestellt sein, dass die Temperatur hoch genug ist, um Stahl zu schmelzen, aber nicht so hoch, dass Wolframkarbidpartikel ebenfalls schmelzen (bei etwa 2900 °C). Denn dann hätten diese ihre Härte verloren. Zahlreiche weitere Parameter kommen hinzu: der Abstand der Düsen zur Oberfläche, die Geschwindigkeit, mit der die Bahnen gezogen werden, die Überlappung der Bahnen, die Laserleistung und vieles mehr. Insgesamt müssen bei der Planung eines Reparaturvorgangs 150 Parameter festgelegt und aufeinander abgestimmt werden.
KI plant und steuert die Reparatur
Für AI-SLAM haben die Fraunhofer-Forschenden deshalb eine mehrstufige KI entwickelt, die diesen komplexen Planungs- und Steuerungsprozess regelt. Im ersten Schritt erfasst ein Linienlaser mithilfe einer CMOS-Kamera (Complementary Metal Oxide Semiconductor) die abgenutzten Konturen des Werkzeugs, beispielsweise eines Baggerzahns. So entsteht ein Abbild der aktuellen Oberflächengeometrie. Dieses wird mit der Kontur des Zahns im Neuzustand abgeglichen, die in der Software hinterlegt ist. Aus der Differenz errechnen sich schließlich Verlauf und Dicke der aufzutragenden Metallschicht. Mittels Kamera erkennt die KI schon während des Beschichtungsvorgangs Abweichungen oder Fehler.
Der Projektpartner BCT hat das KI-Modul der Forschenden in seine Bediensoftware OpenARMS integriert. Diese Software setzt die von der KI empfohlenen Parameter für den Schweißvorgang in Steuerbefehle um. Für das Bedienpersonal entfällt damit das zeitraubende und fehleranfällige Eintippen der Maschinencodes. Braintoy aus Calgary ist für die Machine-Learning-Algorithmen zuständig und stellt die Plattform für die Datenanalyse im LMD-System bereit.
Durch das Zusammenspiel aller Lösungen läuft der Reparaturvorgang fehlerfrei und automatisiert ab. „Der Mensch muss nur noch auf Start drücken“, meint Zimmermann.
Ein Team des Fraunhofer ILT stellt das Projekt AI-SLAM auf der Hannover Messe vom 31. März bis 4. April 2025 vor (Halle 2, Stand B24).
Haben Sie Interesse an weitergehenden Infos aus der Welt der additiven Fertigung? Dann sollten Sie die „Druckwelle“ kennenlernen. Die gibt es in Form eines Podcasts und in Form eines Newsletters – jeweils kostenlos!