Industrie 4.0 braucht auch in den USA Zeit
Glaubt man US-IT-Konzernen, geht die Vernetzung der deutschen Industrie so langsam voran, dass die Idee der Industrie 4.0 nun eher von ihnen umgesetzt wird. Laut einer Studie der Unternehmensberatung PricewaterhouseCoopers investieren allerdings vergleichsweise wenige US-Fertiger in neue Sensortechnologien, nur wenige mehr nutzen das Internetprotokoll in ihren Werken. Auch in den USA sind es einzelne Unternehmen, die als Vorreiter auftreten.

Foto: Rockwell Automation
Das industrielle Internet soll die USA bei der Re-Industrialisierung vorwärtsbringen. Ähnlich, wie sich Deutschland durch Industrie 4.0 Vorteile im globalen Wettbewerb erhofft. Doch auch bei US-Industriefertigern wird deutlich, dass die Umsetzung Zeit braucht.
Was nicht daran liegt, dass die Thematik dort gänzlich unbekannt wäre. Es gibt ähnliche Aktivitäten wie in Deutschland: „Connected Enterprise“ oder „Smarter Manufacturing“ sind die gängigeren US-Bezeichnungen für die neuen Technologien im Bereich der Maschinenvernetzung und der cyber-physischen Systeme.
Bislang allerdings ist das Interesse eher mäßig. Zu diesem Ergebnis kommt eine aktuelle PwC-Untersuchung im Auftrag des US-Manufacturing-Instituts. Die USA liegen demnach abgeschlagen hinter den anderen nationalen Hightechindustrien zurück. Beispielsweise investieren nur 18 % der US-Produktionsbetriebe in neue Sensortechnologien. Damit liegen die USA nach Asien (24 %), Lateinamerika (23 %), Afrika (22 %) und Europa (19 %) auf dem fünften Platz.
Ein weiteres Indiz für die zögerlichen Aktivitäten der US-Hersteller in Richtung digitaler Vernetzung ist der Einsatz des Internetprotokolls. Nur 24 % nutzen derzeit dieses Kommunikationsprotokoll auch auf der Fertigungsebene. Weitere 31 % gaben an, noch nicht einmal entsprechende Einführungspläne dafür zu haben.
Ganz deutlich wird die reservierte Haltung bei der Frage nach der Relevanz des Internets der Dinge und den dafür benötigten Netzstrukturen. Nur 34 % halten diese technologische Entwicklung für wichtig und immerhin 6 % für überhaupt nicht wichtig.
Doch es gibt Ausnahmen. General Electric hat schon vor drei Jahren angekündigt, dass der Konzern 1,5 Mrd. $ in ein „Industrial Internet“ investieren will. Ein Teil dieser Investitionen ging in das 18 000 m2 große Batteriewerk in Schenectady, im US-Staat New York. Dort wurden 10 000 internetfähige Smart-Sensors installiert, die alle Produktionsabläufe in Echtzeit erfassen und sie zur weiteren Auswertung direkt an zentrale Server melden. Die aufbereiteten Informationen stehen dann mittels WLAN allen Mitarbeitern auf entsprechenden iPads zur Verfügung.
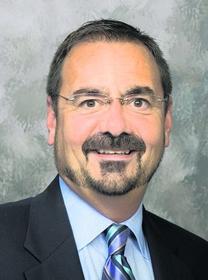
Auch beim Industrieausrüster Rockwell Automation hat man schon vor Jahren die Weichen in Richtung „Connected Enterprise“ gestellt. „Wir begannen bereits 2008 mit unseren ersten Überlegungen für eine vernetzte Fertigungsinfrastruktur. Vier Punkte wollten wir damit verbessern: mehr Flexibilität bei kundenspezifischen Aufträgen, weniger Risiko in der Lieferkette, geringere Lagerbestände und eine höhere Produktivität“, sagt Vice President John Nesi.
Kernstück der Lösung ist die direkte Integration der Systeme der Fertigung mit der darüber befindlichen Business-IT. Bei Rockwell spricht man in diesem Zusammenhang einerseits von der Operationsebene (OT) und andererseits von der IT-Ebene. Auf der Operationsebene setzt das Unternehmen seine beiden Produkte Logix und FactoryTalk ein, während die IT-Ebene aus der ERP-Suite von SAP besteht. Beide Welten wurden zwar schon lange genutzt, waren aber nicht integriert.
Für die technische Verbindung ging Rockwell Automation eine Partnerschaft mit dem IT-Netzwerkausrüster Cisco ein, der schon seit geraumer Zeit auf dem Gebiet des industriellen Internets sehr aktiv ist, da man sich dort immense Zuwachsraten erhofft.
Als weiteren Partner holte man sich AT&T ins Boot, das mit seinem weltweiten Telekommunikationsnetz praktisch das Rückgrat für den gesamten Datenaustausch bildet. Von einem interdisziplinären Team wurde dann das „Manufacturing Execution System“ (MES) entwickelt, das heute in 16 Rockwell-Werken im Einsatz ist und von den untersten Maschinendaten bis hinauf zur obersten SAP-Planungsebene eine durchgängige Datenintegration bietet. Viele der Basisdaten werden von smarten Sensoren erfasst, die die Daten drahtlos an entsprechende Zwischenstationen übertragen. Beispielsweise sind einige Drehmomentschlüssel mit entsprechenden Sensoren bestückt, die sofort einen Qualitätsalarm auslösen, sollte ein kritischer Wert überschritten werden.
Bei Rockwell ist man mit den Resultaten hochzufrieden. „Die erzielten Geschäftsvorteile von MES übersteigen unsere kühnsten Erwartungen“, schwärmt Nesi über den Erfolg der neuen IT-Infrastruktur in seinem Unternehmen. So wurde innerhalb von fünf Jahren der Lagerbestandszeitraum von 120 auf 82 Tage abgesenkt und die Liefertreue von 80 % auf 96 % verbessert. Im selben Zeitraum wurden die Vorlaufzeiten um 50 % verkürzt und 3 Mio. $ pro Jahr an Kapitalkosten eingespart.
„Insgesamt verschafft uns die neue Technologie Produktivitätssteigerungen von 4 % bis 5 % jährlich“, lautet Nesis erfreuliches Resümee. Doch er weist deutlich daraufhin, dass diese Verbesserungen nicht nur eine Folge des Technikeinsatzes sind. „Wir haben sehr frühzeitig in dem Projekt gemerkt, dass die neuen vernetzten Möglichkeiten nur dann voll ausgeschöpft werden können, wenn auch das Umfeld entsprechend darauf optimiert wird“, sagt Nesi über die ersten Projektphasen.
Zu den wesentlichsten Änderungen gehörten neue Workflows, einheitliche Terminologien und Datenstrukturen. Heute haben alle mit MES ausgestatten Werke des Unternehmens weltweit die gleichen Bildschirmaufbauten, die gleichen Grafikstrukturen und einheitliche Bezeichnungen.
Da Rockwell aber nicht nur Anwender von Industrieautomation ist, sondern vor allem auch ein Anbieter, steht die gesamte MES-Technologie auch anderen Unternehmen zur Verfügung. Diese Standardsoftware bietet auch die erforderliche Flexibilität, um einen breiteren Bedarf abzudecken. So lässt sich die Rockwell-Software auch mit anderen ERP- oder SCM-Programmen verbinden.
Hinzu kommen noch verschiedene professionelle Consulting-Dienste. „Wir decken das gesamte Spektrum von der Ist-Analyse über die Definition praktikabler Ziele bis hin zur Implementation und Inbetriebnahme ab“, erläutert Nesi das Angebotsspektrum von Rockwell im Bereich Industrie 4.0.