Kompass zur Orientierung im digitalen Produktionswandel
Gerade kleinen und mittleren Unternehmen können Workshops helfen, die richtigen Schwerpunkte bei der Umsetzung von Industrie-4.0-Konzepten zu identifizieren.
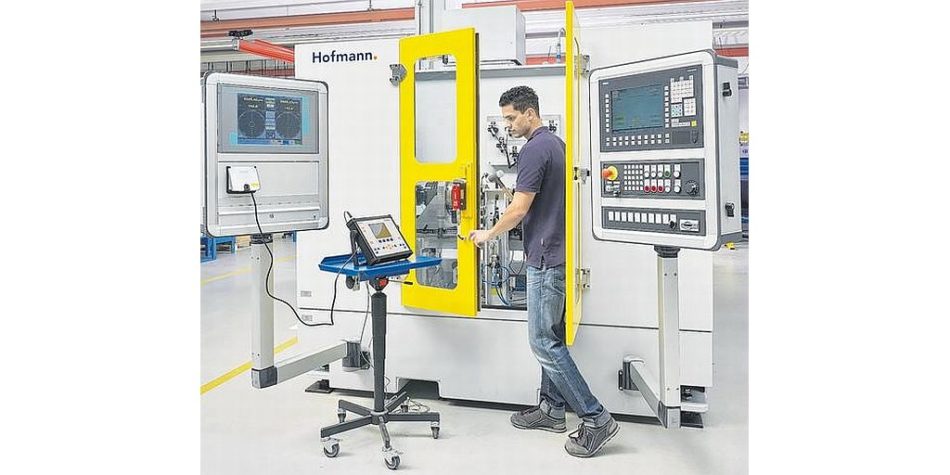
Foto: ProStep/Ralf Kopp
Mittelständische Unternehmen wissen häufig nicht genau, wie sich Industrie 4.0 auf ihre Geschäftsprozesse auswirken wird. Ein Assessment durch externe Berater kann ihnen helfen, den individuellen Reifegrad zu analysieren, Schwachstellen in der IT aufzudecken sowie Potenziale für neue Produkte und Dienstleistungen zu entdecken. „Entscheidend ist, dass diese Strategie immer unternehmensspezifisch an den Unternehmenszielen ausgerichtet ist“, betont Reiner Anderl. Er leitet das Fachgebiet Datenverarbeitung in der Konstruktion (DIK) der TU Darmstadt.
Die Erfassung des Istzustands und Definition des Sollzustands sind die tragenden Säulen eines entsprechenden Assessments, dessen Methodik vom DIK und dem wbk Institut für Produktionstechnik am Karlsruher Institut für Technologie (KIT) entwickelt wurde. Basis dafür ist der praxisnahe VDMA-Leitfaden Industrie 4.0. Die Kompetenz der Unternehmen wird dabei mit einem methodischen Baukasten analysiert, der sowohl den Stand der Produktion, als auch die Ausstattung der Produkte, z. B. hinsichtlich Sensorik, Vernetzung, Datenspeicherung und Monitoring berücksichtigt. Die Analyse ist die Basis, von der aus die zu erreichenden Ziele definiert werden und eine Roadmap mit den wesentlichen Maßnahmen erstellt wird.
Jeder der Methoden-baukästen spezifiziert verschiedene Leistungsstufen für die jeweilige Anwendungsebene. Anhand einheitlicher Kriterien können die Unternehmen somit ihre gegenwärtige Leistungsstufe bestimmen und eine Strategie für die Erreichung höherer Leistungsstufen entwickeln.
„Der Kriterienkatalog erleichtert nicht nur die Bewertung des Industrie-4.0-Reifegrads, sondern auch die Identifizierung von Quick Wins – das heißt von Initiativen, die einen schnellen Return on Invest versprechen“, sagt Anderl. Des Weiteren sind die Ergebnisse der Assessments durch die einheitliche Methodik vergleichbar.
Der Methodenbaukasten, der anfänglich sehr stark auf die Bewertung der technischen Prozesse fokussiert war, wurde inzwischen durch das Projekt „Maturity-Index“ von der Deutschen Akademie der Technikwissenschaften (acatech) weiter entwickelt, Nun werden auch Aspekte wie die Organisationsstruktur und die Führungskultur berücksichtigt.
Das Produktlebenszyklusmanagement (PLM) ist bei Industrieunternehmen oft Ausgangspunkt für Industrie-4.0-Konzepte. Deshalb hat der Darmstädter ProStep-Verein den Methodenbaukasten um PLM-spezifische Kriterien erweitert. Es wird z. B. hinterfragt, in welcher Form die Produktdaten vorliegen, also ob die 2-D-Zeichnung noch der Master ist oder ein 3-D-Modell und ob die Daten bereits mit einem PLM-System verwaltet werden. Denn nicht nur für die ProStep-Berater gilt die Abschaffung papierbasierter Geschäftsprozesse und der Aufbau durchgängig digitaler Prozessketten als grundlegende Voraussetzungen für Industrie 4.0.
Gerade die IT-Infrastruktur ist bei vielen mittelständischen Unternehmen die größte Achillesferse für die Umsetzung von Industrie-4.0-Initiativen. Das zeigte sich auch bei einem Industrie-4.0-Assessment, das ProStep zusammen mit DIK-Leiter Anderl bei der Hofmann Mess- und Auswuchttechnik in Pfungstadt durchführte. Dort erschwert die heterogene IT-Systemlandschaft an den Stadtorten in Pfungstadt und in den USA den Datenaustausch sowie eine durchgängige Nutzung der digitalen Daten.
Um die IT-Landschaft besser zu integrieren, hat das Unternehmen die Software RuleDesigner als standortübergreifende Produktdatenmanagementlösung eingeführt. Sie wird im nächsten Schritt eng mit einem für den Sondermaschinenbau entwickeltem ERP-System gekoppelt, wie Hofmann-Geschäftsführer Georg Fischer erläutert. Er sieht einen Mangel an bezahlbarer Beratung und IT für den Mittelstand.
Hofmann entwickelt Sondermaschinen für große Automobilhersteller wie Daimler und Volkswagen sowie namhafte Zulieferer. Einer der Erfolgsfaktoren des Mittelständlers ist, dass die Maschinen von Anfang an konsequent modularisiert wurden. Dadurch können Module in größeren Stückzahlen gefertigt werden, was nicht nur die Kosten senkt, sondern vor allem auch die Lieferzeiten deutlich reduziert. „Neben Geschwindigkeit ist Zuverlässigkeit unsere wichtigste Herausforderung“, sagt Fischer.
Für den Wissenschaftler Anderl ist Hofmann ein gutes Beispiel dafür, dass die meisten Unternehmen und gerade auch der Mittelstand mit Industrie 4.0 nicht bei null anfangen. Sondermaschinen sind heute schon mit Rechnern ausgestattet, die Messergebnisse und andere Daten an die Leitrechner in der Produktion kommunizieren.
Mit dem Assessment wollte Fischer auch seine Mannschaft wachrütteln. „Wir haben möglichst viele Mitarbeiter aus verschiedenen Bereichen eingebunden, damit sie sich gegenseitig befruchten, denn Industrie 4.0 geht alle an.“ Das Assessment habe die Mitarbeiter für die Möglichkeiten der Vernetzung sensibilisiert und einen Nährboden für Produkt- und Prozessinnovationen geschaffen.
Wesentlicher Bestandteil des Assessments war ein Kreativworkshop, in dem die Mitarbeiter ihre Ideen für Produkt- und Prozessverbesserungen einbringen konnten. Den Entwicklern kamen dabei viele neue Ideen, wie sie die Maschinen durch die Integration von zusätzlichen Sensoren so intelligent machen können, dass sie sich selbst überwachen, bei drohendem Ausfall eines Verschleißteils dem Produktionsplaner eine Nachricht senden oder das entsprechende Ersatzteil direkt bestellen. „Jetzt müssen wir überlegen, welche neuen Servicemodelle wir unseren Kunden künftig anbieten wollen.“
Nach Fischers positiven Erfahrungen mit der Einbindung der Mitarbeiter in den Workshops, soll das Konzept weiter verfolgt werden. Im nächsten Schritt will das Unternehmen eine Roadmap für die Digitalisierung der Prozesse in Materialwirtschaft, Einkauf und Montage erstellen. Danach will Hofmann auch die kleinen Zulieferer mit rudimentärer IT einbinden, um deren Kompetenz einzubinden. „Sie machen unsere Schnelligkeit und Flexibilität aus“, so Fischer.