Lernen in der Endlosschleife
Der Haushaltsgerätehersteller Miele produziert immer kleinere Chargen einer ständig wachsenden Zahl von Gerätevarianten. Um Chaos vorzubeugen, erprobt das Unternehmen nun in seiner Dampfgarer-Fertigung Apps, die den Monteuren und Reparateuren helfen sollen, schneller zu lernen und weniger Fehler zu machen. Ein Werksbesuch.

Foto: Miele
Mittwochmorgen, Frühschicht bei Miele im ostwestfälischen Bünde. Der Monteur Alexander Rieke beugt sich über einen halbfertigen Dampfgarer, der auf einem fahrbaren Werkzeugtisch liegt. Er greift zwei Schienen aus einer Kiste und setzt sie in die passenden Führungen.
Rieke bearbeitet den Dampfgarer schon seit 20 min. und ist wohl noch weitere 20 min beschäftigt. Schritt für Schritt montiert der gelernte Rettungssanitäter das Gerät. Hat er einen Arbeitsgang beendet, schiebt er den Werkzeugtisch ein bisschen weiter im Montage-U und beginnt den nächsten. Und manchmal – zwischen den einzelnen Arbeitsschritten – zögert er ganz kurz und blickt dann fragend auf einen Tablet-PC, der an dem Werkzeugtisch angebracht ist. Noch sitzen nicht alle Handgriffe sicher, Alexander Rieke ist erst seit vier Wochen im Unternehmen.
Die Szene in der Miele-Montage ist auf den ersten Blick nicht außergewöhnlich. Was soll schon Besonderes daran sein, dass Werker in der Fertigung mit Tablets arbeiten? Eher wäre es in einer modernen Fabrik überraschend, wenn sie darauf verzichteten.
In diesem Fall steckt mehr dahinter. Die Dampfgarer-Montage ist Teil des vom Bundesforschungsministerium geförderten Projektes SmartF-IT, eines der ersten Projekte zur Industrie 4.0. In den kommenden Wochen wollen die Projektpartner, darunter die TU Darmstadt und das Deutsche Forschungszentrum für Künstliche Intelligenz (DFKI), ihre Ergebnisse vorstellen.
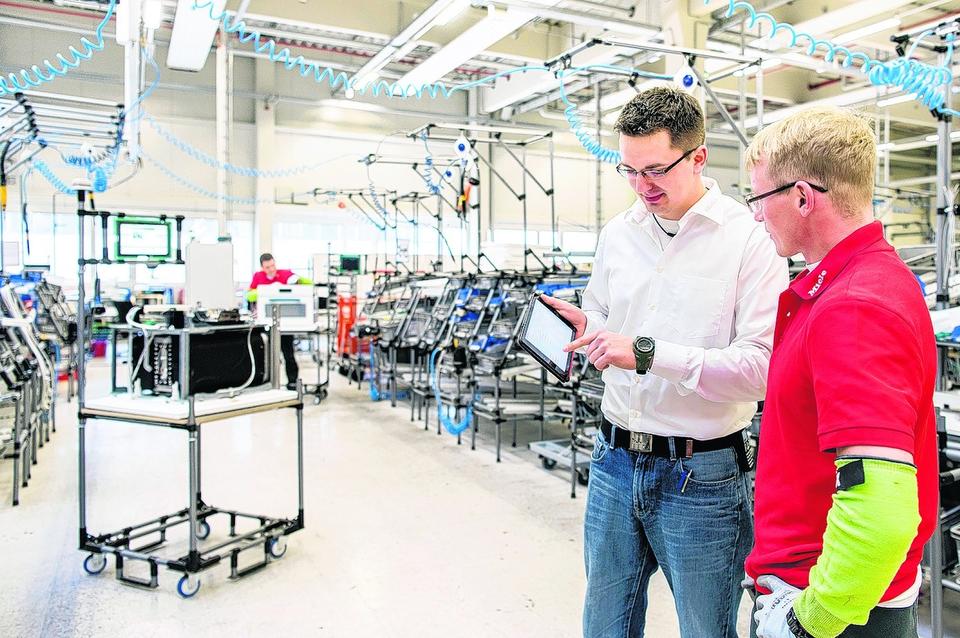
Aus zwei Gründen lohnt es, sich diese Ergebnisse und das Beispiel Miele näher anzuschauen. Erstens geht es hier in Bünde darum, Mitarbeiter zu befähigen, eine rapide steigende Zahl von Gerätevarianten zu montieren. Das ist schließlich das zentrale Versprechen der Industrie 4.0, der Produktionsweise der Zukunft: mit den Methoden und zu den Kosten der Massenfertigung eines Tages Unikate herzustellen. Der Weg dahin ist bereits eingeschlagen: Die Losgrößen sinken.
Und zweitens ändert sich im Zuge dessen die Fabrikarbeit selbst von Grund auf. Die Menschen in den Fabriken werden in Zukunft die ungeheure Variantenvielfalt, die sie herstellen sollen, nur noch bewältigen können, wenn ihnen Computer beim Lernen helfen.
Bei Miele geschieht das mit einer Reihe von Apps, auf die die Mitarbeiter – Monteure, Reparateure und Teamleiter – mit Tablets zugreifen. Drei Jahre hat das Unternehmen gemeinsam mit den Projektpartnern in die Entwicklung gesteckt. Parallel zur mit Apps ausgestatteten Fertigung läuft der Betrieb nach konventionellem Muster: Miele sammelt Daten, um beide Systeme miteinander vergleichen zu können.
Das mag zunächst nach hohem Aufwand klingen, könnte aber den Unterschied machen zwischen geordneter Produktion und Chaos. „Mit Software-Unterstützung finden sich unsere Mitarbeiter signifikant schneller ein als ohne“, sagt Werksleiter Uwe Brunkhorst. „Wir wollen die Fehlerquote und die Anlernkosten jeweils um 30 % bis 40 % senken.“
Miele reagiert mit den Apps auf die immer stärker wachsende Zahl an unterschiedlichen Varianten, die – je nach Kundenwunsch – hier gefertigt werden. Einbau- oder Druckdampfgarer, Dampfgarer mit Mikrowelle, Dampfgarer mit Backofen und mehr. Dazu unterschiedliche Kabel und Stecker für die USA, für Großbritannien, für Westafrika – je nachdem, in welches Land das Gerät geliefert werden soll .
Heute verlassen die Dampfgarer in exakt 337 Ausprägungen das Werk in Bünde. In kurzer Zeit soll sich diese Zahl verdreifachen. Ähnliches vollzieht sich in der Automobilindustrie, im Maschinenbau und wo immer Online-Konfiguratoren angeboten werden. Ein Häkchen beim Autokauf: Blauer Lack. Ein zweites: Ledersitze. Kunden können immer mehr Einfluss nehmen, wie Produkte aussehen.
Die Apps in Bünde haben eines gemeinsam: Sie zielen auf die Lernkurve ab. Je steiler sie ausfällt, desto besser. Die „Werker-App“ für die Monteure zum Beispiel funktioniert so: In einer Datenbank sind zu jedem Montageschritt Hilfen hinterlegt. Das können Fotos sein, Texte oder kurze Videos. Die „Werker-App“ stellt dem Monteur die aktuell relevanten Informationen zur Verfügung. „Wenn ich während der Montage nicht weiter weiß, orientiere ich mich an den Fotos, die mir die App zur Verfügung stellt“, sagt Alexander Rieke.
Dafür ist der Werkzeugtisch mit einem Funk-Transponder versehen. Jedem Ort im Montage-U ist ein Arbeitsgang zugeordnet. Das bedeutet, dass die App über das „Hallen-GPS“, ein WLAN-Ortungssystem, genau feststellen kann, mit welchem Montageschritt sich Alexander Rieke in diesem Moment beschäftigt. Ungefähr so wie bei einem Handbuch, bei dem immer die richtige Seite aufgeschlagen ist.
Die App ist personalisiert: Sie kennt also den Monteur Alexander Rieke sehr gut und berücksichtigt seine Fähigkeiten. In einer Datenbank ist hinterlegt, wie oft er welches Gerät bereits hergestellt hat. Je mehr Erfahrung er sammelt, desto weniger Bilder bekommt er gezeigt. Bis er schließlich kaum noch hinschauen muss.
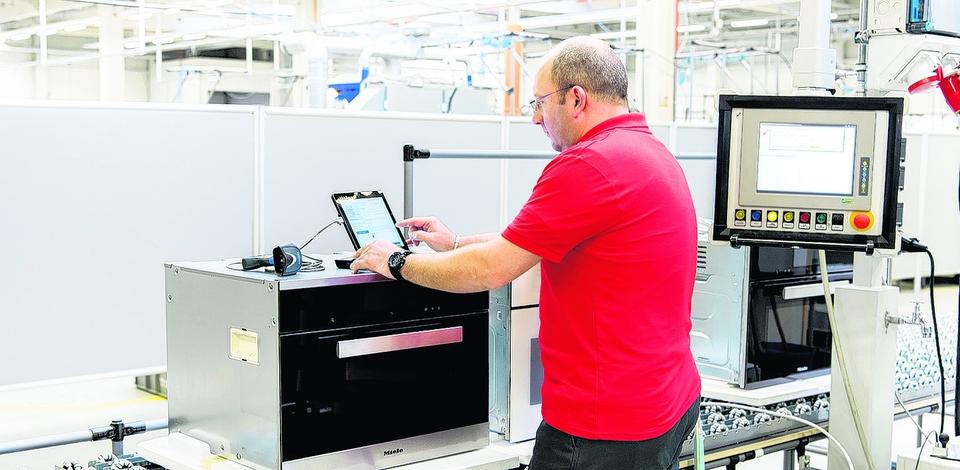
Vor 30 Jahren hätte ein typischer Monteur vielleicht 40 Geräte in der Woche montiert, alle vom selben Typ. Heute sind es immer noch 40, allerdings jeweils fünf Geräte von acht verschiedenen Typen. Und schon bald werden es 40 verschiedene Geräte sein.
Unmöglich, sich bei einer solchen Zahl detailliert zu merken, wann welcher Handgriff zu erfolgen hat. Unvermeidlich, dass sich Fehler einschleichen. „Je höher die Zahl der Varianten, desto mehr Fehler passieren zwangsläufig“, sagt Brunkhorst. Im Werk Bünde beschäftigt Miele deshalb Mitarbeiter, die all jene Geräte reparieren, die in der Qualitätsprüfung nach der Montage Mängel aufgewiesen haben. Auch diese Reparateure nutzen eine App.
Einer von ihnen ist Valentin Späth. Gerade scannt er den Barcode an einem Dampfgarer, der seitlich am Gerät angebracht ist. Auf seinem Tablet-PC liest er den zugehörigen Fehler ab. Für diese Reparatur wird er keine Computeranleitung brauchen, ein Routinefall: „Die App hilft mir vor allem bei komplizierten Fehlern, mit denen ich nicht aus dem Stand fertig werde und deren Behebung sonst viel mehr Zeit beanspruchen würde.“
Stößt Späth auf einen Fehler, der in der Datenbank noch nicht vermerkt ist, trägt er in der App einen neuen Fehler ein. „Ich mache Fotos dazu und schreibe Reparaturhinweise“, sagt der Miele-Mitarbeiter. Auf diese Weise wächst das Wissen unter den Reparateuren. Implizites Wissen, das tief verborgen im Erfahrungsschatz einzelner Menschen verborgen liegt, wird explizit – und damit für andere zugänglich.
Und damit ein durch einen Miele-Mitarbeiter verschuldeter Fehler sich nicht wiederholt, können Valentin Späth und seine Kollegen den Monteuren kleine Hinweise schreiben. Gelangt ein Monteur an eine Stelle, an der er zuvor einen Fehler gemacht hat, erhält er durch die App einen Hinweis, vielleicht ein kleines Foto, wie es richtig auszusehen hat. Gewissermaßen einen Gruß aus der Reparatur. „Früher konnte der Monteur nicht aus seinen Fehlern lernen, weil er gar nicht wusste, dass ihm ein Fehler unterlaufen war“, sagt Rouven Vierfuß, der am Standort Bünde die Arbeitsvorbereitung leitet.
Die Beispiele zeigen: Computergestützte Assistenzsysteme in der Produktion bieten ganz konkrete Vorteile. Und sie könnten in Zukunft unverzichtbar sein. Aber welche Folgen hat das für die Mitarbeiter? Wie verändert sich die menschliche Arbeit?
Zunächst einmal zum Positiven. Denn durch den Einsatz von Assistenzsystemen wie der App für die Reparateure steigen die Möglichkeiten zur Partizipation. „Die Werker erhalten in der digitalisierten Fabrik die Chance, Einfluss auf die Arbeit zu nehmen“, sagt der Betriebsrat Daniel Brockmann.
Der Reparaturmitarbeiter Valentin Späth gibt dem Monteur Alexander Rieke direkt Hinweise – mitten im Produktionsprozess. „Apps können einen Rückkanal schaffen“, sagt der Arbeitsforscher Sebastian Schlund vom Fraunhofer-Institut für Arbeitswirtschaft und Organisation IAO in Stuttgart. „Sie können also dem Werker die Möglichkeit bieten, seine Erfahrungen in der Produktion einzubringen – zum Beispiel mithilfe von Fotos oder kurzen Videos.“
Hinzu kommt, dass sinnvoll gestaltete Apps dem Werker Zeit geben. Die Zeit nämlich, die er ohne Assistenzsystem auf der Suche nach einer Antwort auf seine Frage verbracht hätte. „Durch die Reduktion der Suchzeiten, die die meisten Werker als störend empfinden, steigt der Freiraum, um sich in kontinuierlichen Verbesserungsprozessen einzubringen“, sagt der IAO-Wissenschaftler Schlund.
Ein weiterer positiver Effekt für die Werker: Die Komplexität der Arbeitsplätze nimmt zu. Ein Miele-Mitarbeiter baut 40 min lang ein Gerät und er baut viele verschiedene Varianten. „Können die Werker ein breites Spektrum an Geräten montieren, sichert das Arbeit. Dann nämlich, wenn einzelne Montagebereiche automatisiert werden,“ sagt der Betriebsrat Brockmann.
Viele Aspekte der Industrie 4.0 können als Fortschreibung industrieller Automatisierungstechnik begriffen werden. Ein schöner Gedanke ist das, dass nun ausgerechnet Automatisierungstechnik die Werker gegen die negativen Folgen der Automatisierung – Rationalisierung und Stellenabbau nämlich – immunisieren könnte.
Das ist die eine, positive Lesart. Es gibt noch eine zweite, für die Werker bedrohliche. Apps und andere computergestützte Lernsysteme schaffen in den Fabriken zwei Arten von Flexibilität. Einerseits werden die Werker flexibler in dem Sinne, dass sie mehr Arbeitsgänge beherrschen, mehr Varianten herstellen können.
Andererseits werden natürlich auch ihre Arbeitgeber, die produzierenden Unternehmen, flexibler. Systeme wie die „Werker-App“ haben die Aufgabe, den Anlernprozess zu verdichten und ihn in kleine, verständliche Teile zu gliedern. Kleinteilige Schritte, für die ein jahrelanger Erfahrungsschatz nicht mehr nötig ist.
Im Extremfall sind die Zeiten dann vorbei, in denen ein Werker jedes Husten seiner Produktionsanlagen kannte und somit über die Jahre wertvolles Wissen aufbauen konnte. „Wenn die Tätigkeitsprofile gleich bleiben, erhöhen Anlern-Apps die Ersetzbarkeit von Werkern“, warnt der Arbeitsforscher Sebastian Schlund.
Der Extremfall muss nicht eintreten. Aber er ist ein Szenario, für das es bereits Hinweise gibt. „Ich sehe die Gefahr, dass durch Software-Unterstützung Tätigkeiten zu niederschwellig werden“, sagt zum Beispiel der Betriebsrat Brockmann. Trotz andauernden Lernens droht Lernentwöhnung, auch die Vielfalt der Arbeitsgänge bewahrt den Werker dann nicht mehr vor Monotonie.
Wie also können Assistenzsysteme für die Produktion im Sinne guter Arbeit gestaltet werden? Die SmartF-IT-Projektpartner haben erste Erfahrungen bereits gesammelt. Sie haben die Miele-Mitarbeiter früh an der Gestaltung der Apps beteiligt, sie haben die Apps personalisiert und sie haben Rückkanäle eingerichtet, damit die Mitarbeiter ihre Erfahrungen in der Produktion zurückspielen können.
Ob die Arbeit besser oder schlechter wird, muss sich noch zeigen. In jedem Fall zeigt das Beispiel der Dampfgarer-Fertigung in Bünde, dass die Industrie 4.0 die menschliche Arbeit umkrempeln wird.