SmartFactory KL: Das wurde auf dem Innovationstag vorgestellt
Noch immer tun sich Unternehmen mit der Vernetzung ihrer Produktionsanlagen schwer. Was ihnen das Leben leichter machen kann, war jetzt Thema beim Innovationstag der SmartFactory KL in Kaiserslautern.
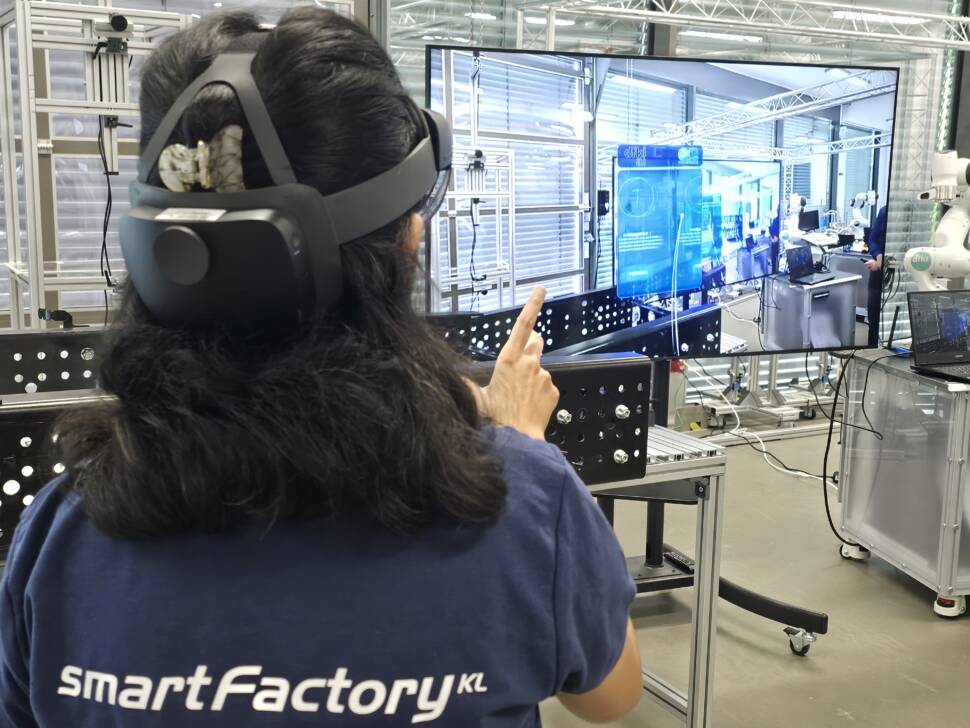
Foto: M. Ciupek
Wie sehr sich die Grundidee der smarten Fabrik weiterentwickelt hat, ist an kaum einem anderen Ort deutlicher zu erkennen als in Kaiserslautern. Bei der Eröffnung der SmartFactory vor 19 Jahren hatte kaum jemand eine Vorstellung von den Potenzialen der Digitalisierung in der Industrie. Beim Innovationstag in dieser Woche wurde es hingegen schon sehr konkret. Auch Partner und Gästen haben dazugelernt und kommen inzwischen mit sehr konkreten Vorstellungen.
Bevor der Begriff Industrie 4.0 geprägt wurde, ging es am Standort des Deutschen Forschungszentrums für Künstliche Intelligenz (DFKI) darum, Grundlagen für die modulare Automatisierung mit Komponenten unterschiedlicher Hersteller zu schaffen. „Wir haben festgestellt, dass es nicht bei Digitalisierung und cyber-physischen Systemen bleibt. Es geht um die Anwendung und vor allem um ganz neue Strukturen der Produktion“, sagt der heutige Vorstandsvorsitzende der SmartFactory KL (SFKL), Martin Ruskowski. Von den auf dem Papier erarbeiteten Konzepten autonomer Produktionseinheiten habe man inzwischen vieles umgesetzt. Deswegen blicken er und sein Team inzwischen weiter nach vorne.
Konkreter wird der Wandel beispielsweise durch den Einsatz von digitalen Zwillingen, künstlicher Intelligenz (KI), digitaler Dienste sowie durch die vereinfachte Interaktion zwischen Mensch und Maschine. Trotzdem möchte Ruskowski nichts von einem neuen Trend zu Industrie 5.0 wissen. „Industrie 4.0 ist das Zeitalter, in dem wir leben. Das Production Level 4 ist das, was wir dazu inhaltlich erarbeiten wollen.“ Seine These: Industrie 4.0 ist deutsch, deshalb mache man jetzt Industrie 5.0, um weiter zu sein als die Deutschen. Inhaltlich basiere das weiterhin auf der Grundidee von DFKI-Professor Wolfgang Wahlster. „Auf die Diskussion wollen wir uns deshalb nicht einlassen“, so Ruskowski.
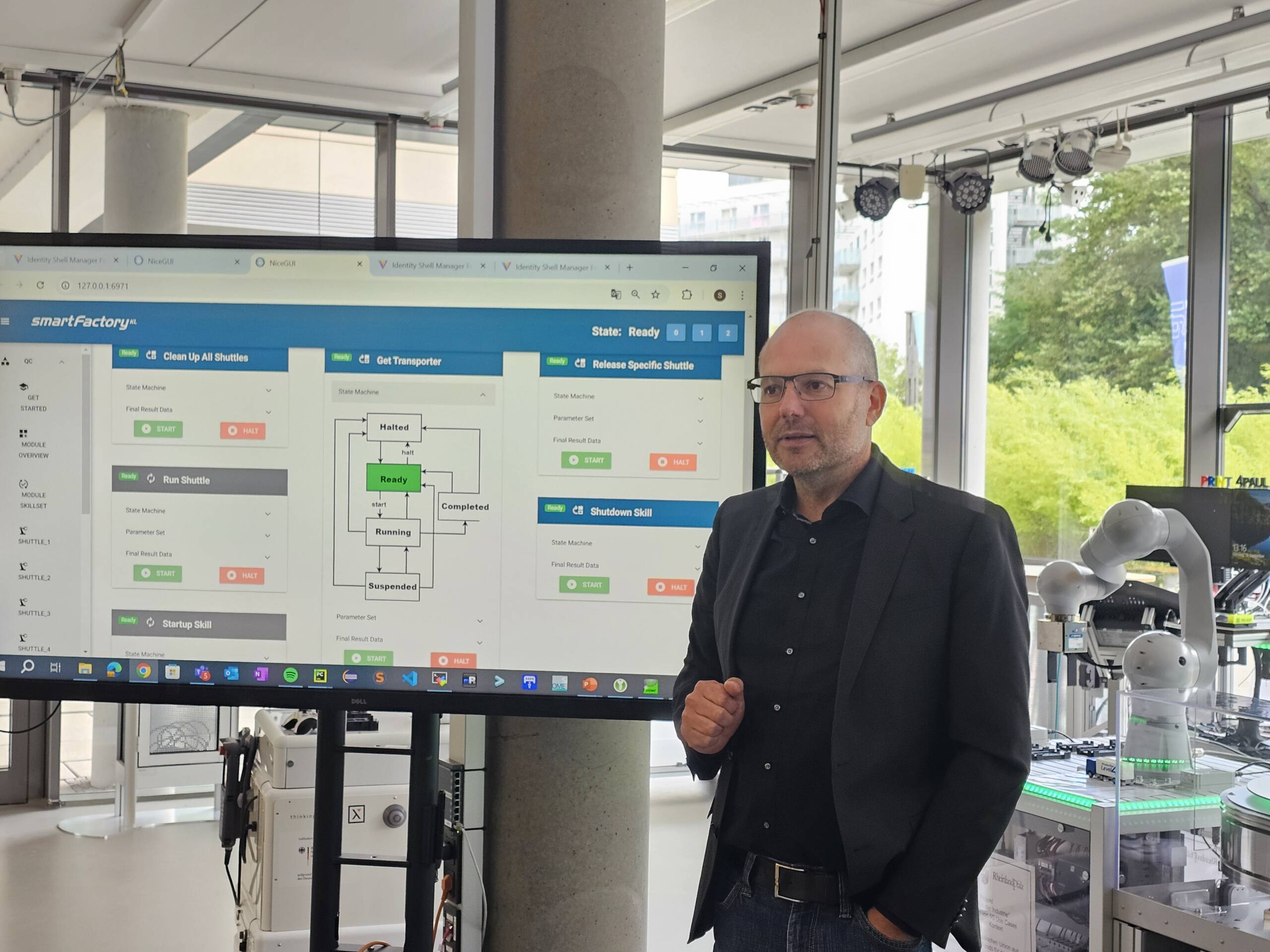
Folge des demografischen Wandels: Produktion braucht Systeme, die weniger menschlichen Eingriff erfordern
Mit Blick auf eine immer älter werdende Bevölkerung kommt der Produktionsexperte zum Ergebnis: „Wir brauchen Systeme, die in der Lage sind, mit immer weniger Menschen arbeiten zu können.“ Wie die Technik Menschen künftig unterstützen kann, das verdeutlichen inzwischen mehrere Demonstratoren der SFKL. Die arbeiten weit vernetzt über Datenräume verteilt in den Räumen des DFKI und der Technischen Universität Kaiserslautern.
Wie beispielsweise digitale Zwillinge dazu eingesetzt werden, die Montage von Lkw zu verbessern, zeigen die bisherigen Erkenntnisse des Forschungsprojekts Twin4Trucks. Hier werden standardisierte Daten aus den Verwaltungsschalen der Komponenten und Datenräume genutzt. Zur Übertragung kommen u. a. die Funktechnologien 5G und UWB (Ultrabreitband) sowie Verfahren der künstlichen Intelligenz zum Einsatz. Für die smarte Unterstützung der Beschäftigten werden beispielsweise Betriebsmittel wie Schraubwerkzeuge lokalisiert und Schraubprozesse dokumentiert. Das ist aufgrund der Nachweispflichten für die Hersteller nötig. Gleichzeitig gilt es, bei den Fahrzeugrahmen mit ihren zahlreichen vorgebohrten Löchern immer wieder neue Varianten zu beachten.
Projektpartner Daimler Truck nutzt die Technologien in der praxisnahen Laborumgebung. Das Projektteam kann damit Tests durchführen, die in der Fabrik die Abläufe stören würden. Gleichzeitig ist laut den Forschenden durch die Nachbildung der realen Arbeitsumgebung eine schnelle Übertragung der Forschungsergebnisse in die Praxis möglich. Die staatliche Förderung senke zudem die Einstiegshürde, solche Projekte durchzuführen.
Daimler Truck trainiert KI-Modelle für die Qualitätssicherung
Trainiert werden beispielsweise KI-Modelle für die Qualitätssicherung, wie sie künftig im Daimler-Werk in Wörth eingesetzt werden sollen. Bisher geht dort am Ende der Montage noch ein Mensch um den Rahmen und prüft alle Schrauben manuell. Das soll durch ein sogenanntes Q-Tor überflüssig werden, durch das der Rahmen fährt. Kameras erkennen dabei, ob Bauteile an der richtigen Stelle sind und Schraubenköpfe richtig am Rahmen abschließen. Bei Abweichungen signalisiert das System dem Personal, wo nachgeprüft werden muss. Damit verbunden ist beispielsweise der digitale Service, bei dem Drehmomente vom Schraubwerkzeug direkt bewertet und im Datenraum dokumentiert werden.
Weil in der Produktion von Daimler Truck nach Unternehmensangaben aktuell nur wenige Fehler passieren, nutzt das Team zum Training der KI einen Trick: Bilder von Montagesituationen an Fahrzeugmodellen werden virtuell erstellt. Trainingsdaten werden damit automatisch generiert und als gut bzw. schlecht gekennzeichnet.
Nach jetzigem Entwicklungsstand bekommt das Personal dann auf einem kleinen digitalen Gerät (PDA) angezeigt, worauf im jeweiligen Abschnitt zu achten ist. Zukunftsmusik ist dagegen noch der Einsatz von Mixed-Reality-Brillen. Das System bekommt dazu über die Verwaltungsschalen Informationen sowohl zu den Bauteilen als auch zu den Werkzeugen. Die werden im Einsatzbereich lokalisiert. Die Werkerin (s. Betragsbild) erhält dann passende Informationen direkt in ihrem Sichtbereich.
Mensch-Roboter-Interaktion: Wie KI die Sicherheit bei Cobots verbessern kann
Eine andere Art der Mensch-Maschine-Interaktion erlauben Cobots. Damit diese Leichtbauroboter gefahrlos nebeneinander und neben Menschen arbeiten können, gilt es bei der Bahnplanung einiges zu berücksichtigen. Gleichzeitig soll die Programmierung möglichst einfach sein. Das wird am Projekt „kollaborative und kooperative Robotikplattform – KoKoBot“ deutlich. Kameras erfassen hier Objekte und Menschen. Die Theorie ist einfach: Wird eine Gefahr erkannt, wird der Roboter langsamer oder stoppt ganz.
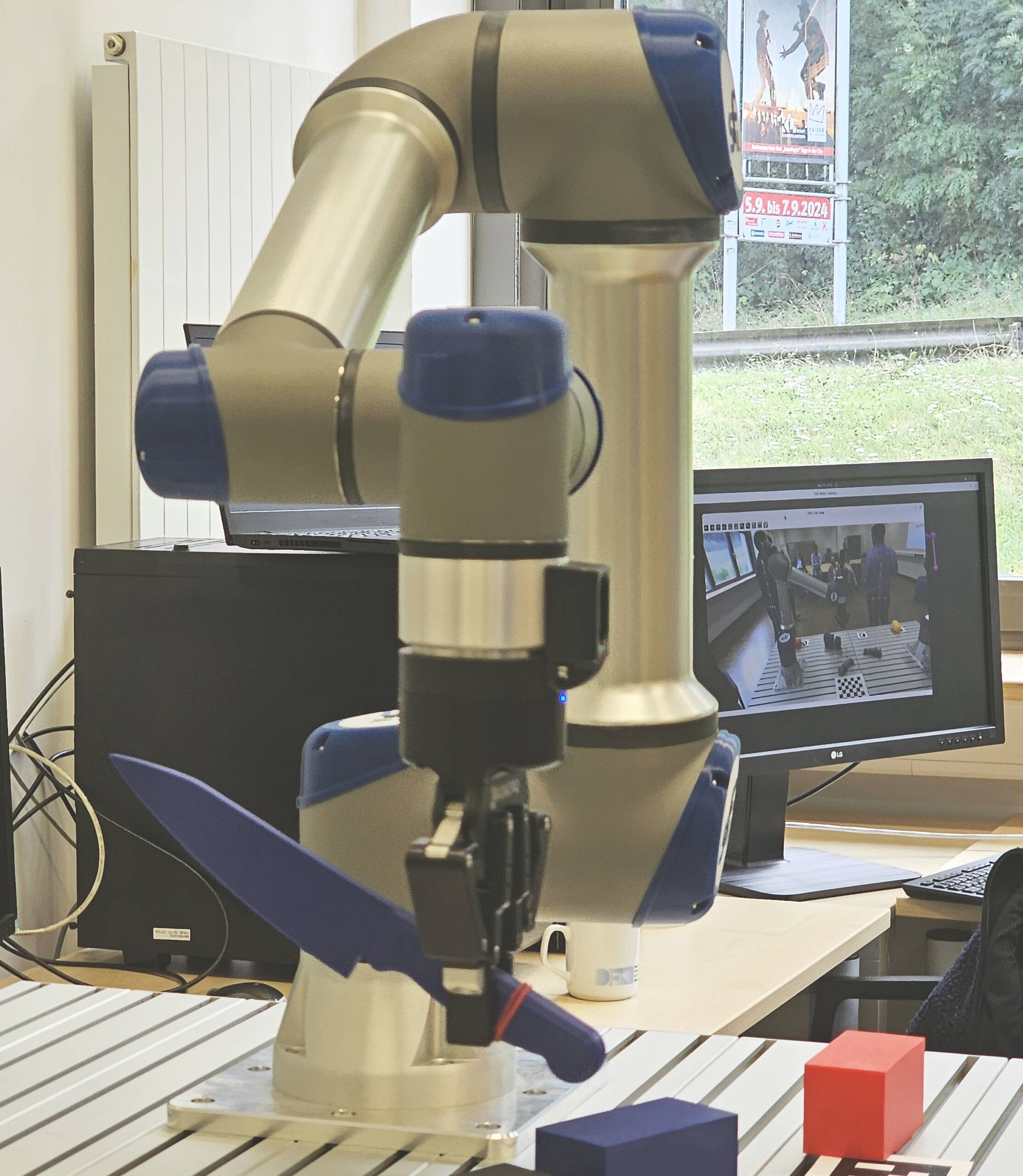
Eine Herausforderung bleibt dabei aber laut Lars Komrowski vom TÜV Hessen die Sicherheitsbewertung. Er macht es mit einem Kunststoffmesser am Greifer des Roboterarms deutlich. „Wenn ich mit dem Rücken zum Roboter stehe, habe ich keine Chance zu reagieren“, macht er deutlich. Trotz Drucksensorik und kurzen Reaktionszeiten könne es dabei zu schweren Verletzungen kommen. Im Idealfall erkenne das System per KI den Menschen und der Roboter hält an oder weicht je nach Programmierung sogar aus. Hier wollen die Wissenschaftler deshalb die Erkennungsquoten verbessern. Denn je nach Kleidung oder Beleuchtung könne es passieren, dass das KI-System Personen nicht erkennt. Die Sicherheitstechnik würde dann versagen.
Vom Hersteller ist laut Komrowski meist die Nutzung des Roboters ohne Kontakt zum Menschen abgesichert. Der Anwender ist damit selbst verantwortlich, dass darüber hinaus entsprechende Sicherheitsnormen eingehalten werden. Für eine Situationsbewertung per KI gebe es diese bisher aber noch nicht.
Zuverlässigkeit der KI und der AI Act beschäftigen die Roboterbranche
Selbst nach umfangreichen Tests ist laut dem Fachmann heute immer noch nicht gewährleistet, dass das KI-System in jeder Situation zuverlässig reagiert und nicht irgendwann etwas anderes macht. Mit erklärbarer KI könne man zwar gewisse Kriterien für die Erkennung von Lebewesen heranziehen. Bei Pferdemotiven aus dem Internet fand die KI aber teilweise Analogien, weil sie auf den Bildern ebenfalls vorhandene Trademark-Zeichen mit bewertete. „Der KI war nicht klar, dass das kein relevantes Zeichen ist“, so der TÜV-Experte.
Das EU-Gesetz zur künstlichen Intelligenz (AI Act) habe deshalb nun die Folge, dass verschiedene technische Normen entsprechend überarbeitet werden müssen. Bis Ende dieses Jahres sollen nach Aussage von Komrowski erste Entwürfe dazu vorgestellt werden. Und: Bis Ende 2025 sollen die Normen veröffentlicht werden. Für den Sicherheitsfachmann ist das eine „unglaublich hohe Geschwindigkeit“. Roboterexperten, die sich mit der Normung beschäftigten, müssten sich dazu in Fragen der KI einarbeiten oder Spezialisten hinzuziehen. Deshalb ist für ihn momentan noch offen, wohin die Reise in dem Bereich der Robotik geht.
Datenraum Factory-X soll Service im Maschinenbau automatisieren
Wohin die Reise bei Datenräumen in der Produktion geht, soll dagegen das Projekt Factory-X zügig konkretisieren. Das größte Konsortium im Rahmen der Förderinitiative Manufacturing-X ist ebenfalls in Kaiserslautern angesiedelt. Daran beteiligt sind auch zahlreiche Partner der SmartFactory KL, wie das Maschinenbauunternehmen Trumpf. Das Konsortium hat dazu Anwendungsfälle für Dienstleistungen identifiziert, die für alle Produktionsunternehmen interessant sein sollen.
Im Fokus stehen hier vor allem autonome Dienstleistungsangebote (service operations). Anders als zu den Anfängen des Fernzugriffs auf Maschinen per Modem gibt es heute durch Internettechnologien zusätzliche Optionen, beispielsweise für die Einbindung von Kameradaten. Mit einer zunehmenden Datenmenge lasse sich das aber kaum noch von Menschen beherrschen, deswegen würden die Prozesse nun automatisiert. Der Mensch bekomme nur noch Anomalien gezeigt und könne somit mehrere Maschinen gleichzeitig bedienen. Damit verändere sich der Blick auf den Service, heißt es vom Projektpartner Trumpf.
Konnektivität von Modulen in der Produktion: OPC UA und Verwaltungsschale rücken zusammen
Mit mehreren Produktionsmodulen hat die SmartFactory KL in der Vergangenheit zahlreiche Teilaspekte von Industrie 4.0 greifbar gemacht und Testumgebungen geschaffen. Die sind auch heute noch im Laborbereich der Initiative zu finden. In nächsten Schritt geht es den Wissenschaftlern nun darum, die Konnektivität weiter zu verbessern. Dazu wollen sie die beschreibenden Standards der Verwaltungsschale mit den branchenspezifischen Spezifikationen (Companion Specification) der plattformunabhängigen Netzwerkarchitektur OPC UA (Open Platform Communications United Architecture) nutzen. Schlüssel dazu sind Knotensätze (Nodesets), mit denen die Variablen von einer Vielzahl zusammengehörender Daten leichter verarbeitet werden können. In den Produktionsinseln kommen diese Daten beispielsweise von Steuerungen und Sensoren unterschiedlicher Hersteller mit unterschiedlichen Informationsmodellen. Deshalb dauern Inbetriebnahmen solcher Anlagen entsprechend lang.
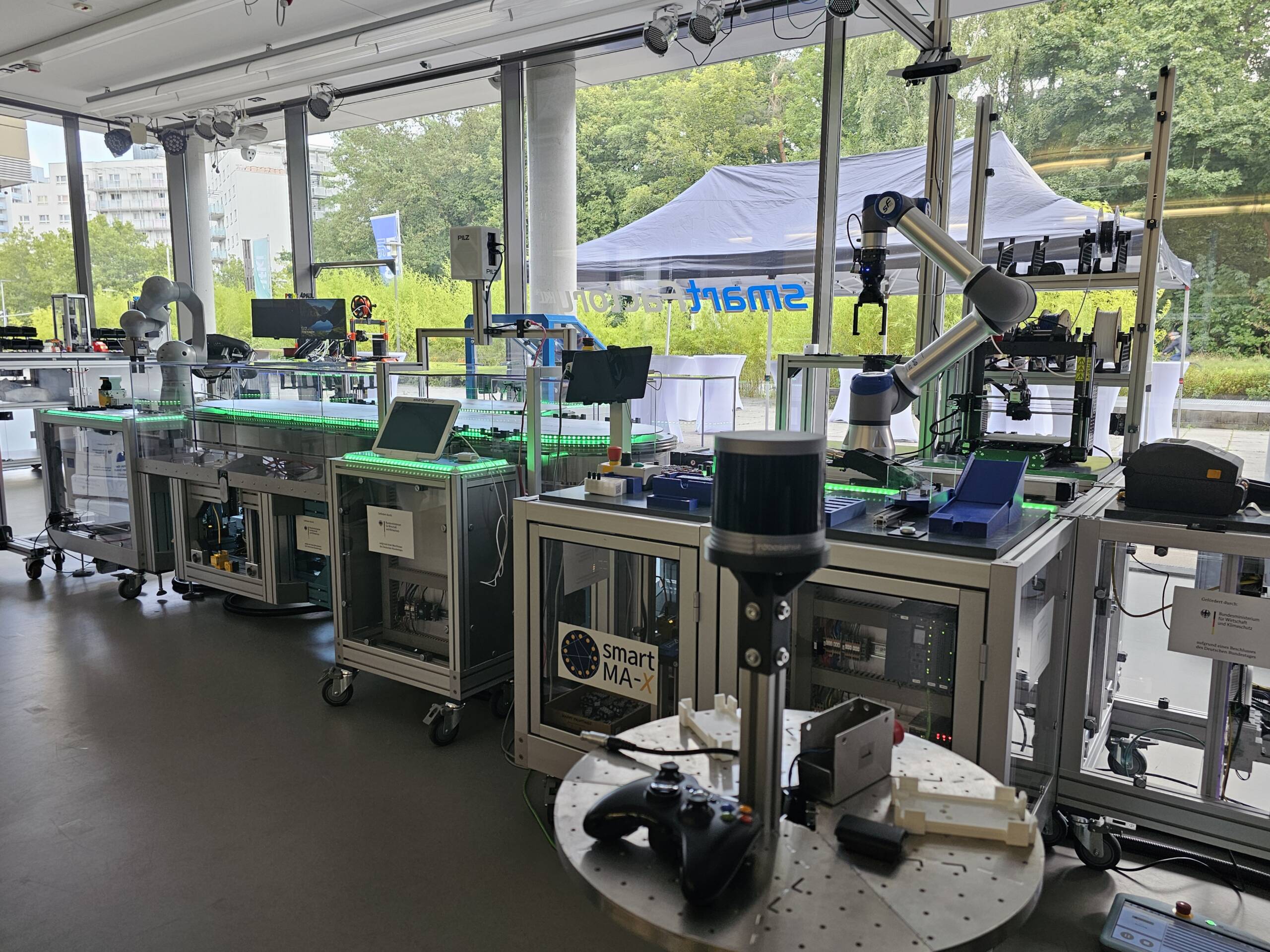
Anwender werden laut Simon Jungbluth, Projektleiter an der SMKL, von interoperablen Standards und deren Submodellen erschlagen. Die Forschenden differenzieren dazu den Teil an echtzeitkritischen Daten direkt an der Maschine und einen weniger zeitkritischen Teil abseits der Maschine. OPC UA wird dabei für die Maschinenebene bevorzugt. Alles, was den Lebenszyklus der Maschine betrifft, befindet sich dagegen auf einer höheren Ebene. Dazu gehören z. B. CAD-Modelle und Werkeranweisungen. Auf der Ebene wird deshalb die Verwaltungsschale genutzt. Dort befinden sich dann auch Daten, die mit anderen Unternehmen geteilt werden sollen.