Produktion des BMW i3 setzt neue Maßstäbe
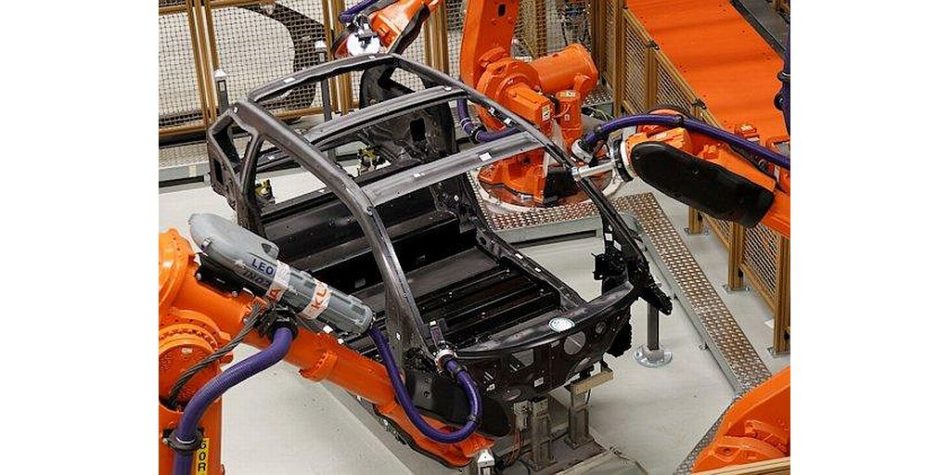
Foto: BMW
Obwohl der schnelle Erfolg am Markt mit dem 35 000 € teuren Stadtautos i3 keinesfalls sicher ist, hat BMW zumindest für die Herstellungs- und Logistikprozesse neue Maßstäbe gesetzt. Der Premiumhersteller produziert das kompakte Elektrofahrzeug seit Mitte September im Leipziger Werk in Serie.
400 Mio. € haben sich Münchner die E-Mobilität bei konsequentem Leichtbau kosten lassen, nun spricht Produktionsvorstand Harald Krüger von einer „technischen Revolution, die Geschichte im Automobilbau schreiben wird“. Denn beim viersitzigen i3 mit etwa 150 km Reichweite konnte nicht nur das Batteriegewicht von etwa 300 kg durch den Einsatz von Kohlenstofffaser-Verbundwerkstoff für die Karosserie, Kunststoffteile für die Außenhaut und einem geschweißten Aluminiumrahmen für das Fahrgestell kompensiert werden.
Diese Werke liefern Komponenten
Das Montagewerk des BMW i3 in Leipzig erhält Baugruppen von verschiedenen anderen Standorten:
-Aus Moses Lake/USA kommen die Kohlenstofffasern, die in einem Joint Venture mit SGL Carbon produziert werden.
-In Wackersdorf werden aus den einzelnen Fasern CFK-Textilien hergestellt.
-Aus Landshut kommen Elektroantriebe.
-In Dingolfingen werden Hochvoltspeicher, Getriebe sowie Aluminium-Chassis gefertigt. CIU
Die neuen Materialien wurden zugleich dafür genutzt, die Abläufe am Band völlig anders zu gestalten als in der klassischen Automobilproduktion. Nach BMW-Angaben reduzieren sich so die Durchlaufzeiten und die Teileanzahl jeweils um rund 50 %.
Während in der Nachbarhalle im Karosseriebau des hier in Leipzig gefertigten X1 mehr als 100 Roboter die Funken sprühen lassen, um die zuvor von der Presse mit enormer Kraft geformten Seitenteile, Böden, Dächer und Traversen zu einem Ganzen zu fügen, geht es in der neuen Halle der i-Reihe geräuscharm und mit sichtlich weniger Energieeinsatz zur Sache. Rund 160 m messen die Klebestreifen einer i3-Karosserie. Nur noch 90 s beträgt die Zeit, bis der neue Kleber Haftung aufbaut und noch bearbeitet werden kann. Nach 90 min ist er bereits ausgehärtet, die rund 150 CFK-Teile zuverlässig verbunden. Sie werden auf jeweils drei Presslinien in Leipzig und Landshut gefertigt.
Die Herstellung von CFK-Teilen galt in der Serienproduktion bislang als Neuland mit einem hohen Anteil manueller Tätigkeiten. Seit gut zehn Jahren arbeitet BMW an solchen Prozessen und hat bereits einzelne Komponenten für den Bau für Sportfahrzeuge eingesetzt, wie Krüger berichtet. Doch erst mit der Großserie habe man jetzt ein Verfahren zur Einsatzreife gebracht, bei dem die Formung und der Zuschnitt der Gewebematten automatisiert und die thermische Aushärtung der Harze deutlich beschleunigt werden konnten. „Wir haben den Zeitaufwand um den Faktor 30 reduzieren können, das macht den Einsatz wirtschaftlich“, so Krüger.
Notwendige Durchlässe werden nun per Wasserstrahlschneider zum großen Teil erst am Band in die CFK-Teile eingefügt, etwa für das Sonnendach. „Das spart wie die neue Lackierung erheblich Zeit und Aufwand, weil wir die Teile nicht mehr mit einer klassischen Großpresse herstellen und dann lagern und vor dem Lack montieren müssen“, berichtet Produktionsleiter Helmut Schramm. Bisher etwa wurde die Karosserie nach dem Rohbau zunächst in einem Tauchbad lackiert, was mehrere Arbeitsgänge und Trocknungszeiten erforderte. Somit läuft ein i3 deutlich kostengünstiger vom Band und benötigt dafür nur 20 h. Das ist etwa die Hälfte der Zeit der klassischen Fertigung. Allerdings erkauft sich der Automobilhersteller den Vorteil durch weniger Variantenreichtum im Vergleich zu anderen BMW-Modellen.
Die Fertigungstiefe des neuen i3 in Leipzig ist dabei gering, BMW-Produktionsvorstand Harald Krüger spricht von rund 15 %. Die Aluminiumrahmen werden z. B. im Werk Dingolfing gefertigt. Auch die Elektromotoren kommen nicht etwa aus dem Kompetenzzentrum für Elektroantriebe, sondern aus Dingolfing. Die komplette Entwicklung bleibt auf das Münchner Zentrum konzentriert. Die Anlieferung erfolgt über die für BMW schnellste und kostengünstigste Variante, sagt Krüger. So soll ein Teil der Zulieferungen mit Lang-Lkw geschehen. Die Fahrtstrecke aus Bayern nach Leipzig ist dafür freigegeben.
Auch die Ansiedlung eines Produktionswerkes für Lithium-Batterien, um das sich sowohl Leipzig als auch Halle beworben hatten, ist derzeit nicht in Sicht – wohl auch, weil die Produktionszahlen des i3 zunächst nicht sehr hoch eingeschätzt werden. Konkrete Zahlen nennt Krüger hier nicht. Einen Anhaltspunkt liefern allerdings die Produktionsmengen von CFK-Fasern im US-amerikanischen Werk Moses Lake von etwa 3000 t im nächsten Jahr. Eine CFK-Zelle wiegt etwa ein Drittel eines Stahlrohbaus, also 100 kg, sagt Krüger. Allerdings sind dann bereits die schweren Harze enthalten.
Sollte jedoch die Nachfrage nicht die Erwartungen bei BMW erfüllen, hätte das neue Werk ein großes Problem: Das Band ist völlig getrennt von der bisherigen Produktion, wo inzwischen rund 750 Autos pro Tag gefertigt werden. Für einen Austausch von weniger mit stärker nachgefragten Modellen taugt die neue Fabrik vorerst also nicht, zumal der i8 ein recht exklusiver Sportwagen ist, der schon preislich nicht für den Massenmarkt gedacht sein dürfte. Dass die Zahlenreihe zwischen 3 und 8 noch viele unbesetzte Positionen hat, lässt aber auch dieses Problem eher als zeitweilig erscheinen. „Wir sehen die Elektromobilität mit einer großen Zuversicht, aber es ist kein Sprint“, sagte Krüger. Es wird eher ein Marathon. M. SCHULZE