Bauen nach dem Lego-Prinzip mit Platten aus Carbonbeton
Ein Haus einfach zusammenstecken – und nach der Nutzung zerlegen, um es wiederzuverwenden? Wie das konkret geht, demonstriert ein Team der Zürcher Hochschule für Angewandte Wissenschaften an einem Gebäude in Winterthur.
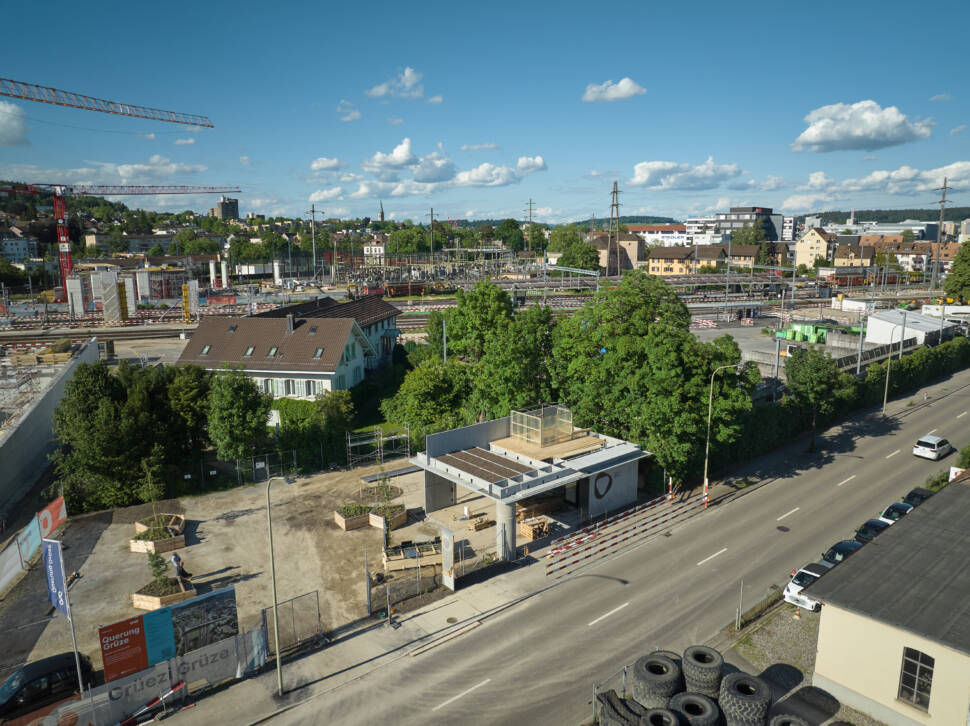
Foto: Valentin Studerus
Inhaltsverzeichnis
Ein Kindertraum wird wahr: Wie damals im Kinderzimmer könnte es künftig auf unseren Baustellen zugehen. Häuser und Gebäude werden dann einfach mit Fertigbauteilen zusammengesteckt und nach der Nutzungsphase rückgebaut und wiederverwendet. Ein Team der Zürcher Hochschule für Angewandte Wissenschaften (ZHAW) hat dafür Carbonbeton-Platten entwickelt und erstmals im Hochbau eingesetzt. Ein weiterer Vorteil: Die filigranen und dennoch belastbaren Fertigelemente kommen mit wesentlich weniger Material aus, was wiederum den CO2-Ausstoß im Bausektor erheblich senkt.
Hier wird Ihnen ein externer Inhalt von youtube.com angezeigt.
Mit der Nutzung des Inhalts stimmen Sie der Datenschutzerklärung
von youtube.com zu.
Modularer Baukasten für den Hochbau
Carbonbeton ist nicht neu. Wohl aber die Fertigbauweise, bei der die einzelnen Bauteile in einer Fabrik vorgefertigt, bearbeitet und zugeschnitten werden. Damit lassen sich Bauwerke auch unabhängig von der Witterung vorbereiten und dann in viel kürzerer Zeit auf der Baustelle zusammenstecken. Ein Vorteil vor allem für städtische Baustellen, betont der ZHAW-Professor Josef Kurath. Darüber hinaus sind Erweiterungsbauten exakter zu planen und vorzubereiten, bevor sie vor Ort montiert werden.
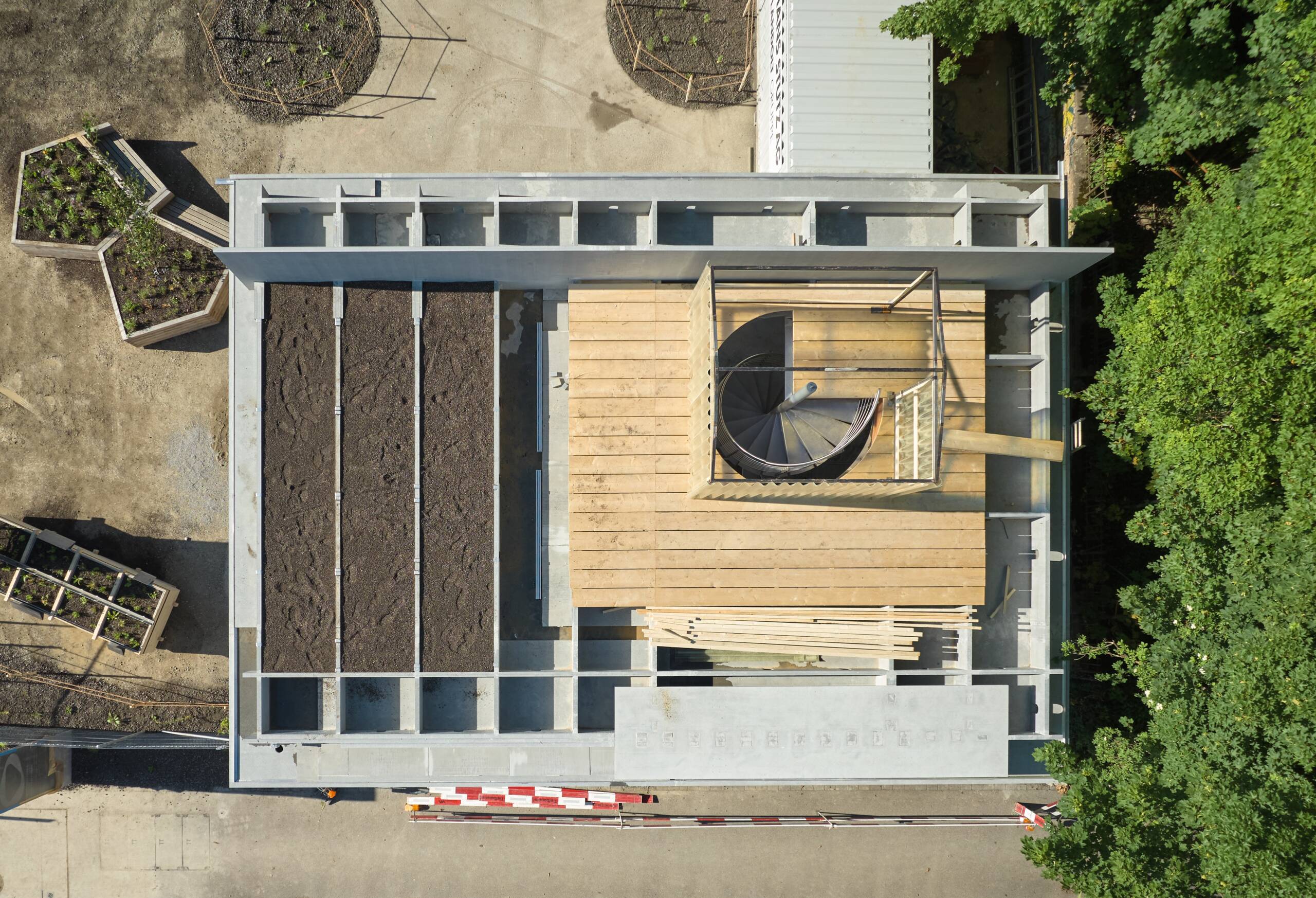
Ähnliches gilt für den Rückbau: Dieser soll laut den Wissenschaftlern mit wenig Aufwand gelingen. Die Betonplatten, die der Baustoffproduzent Holcim über ein neuartiges Sharing-Modell bereitstellt, können dann für ein anderes Bauwerk wiederverwendet werden. Wo beim Abriss eines herkömmlichen Gebäudes etwa 90 % des Beton nicht direkt nutzbar sind, ist es beim neuen Bausystem genau umgekehrt: Rund 90 % des Materials und der im Bauteil steckenden Wertschöpfung können wiederverwendet werden. Da Zement immerhin für 8 % der weltweiten Treibhausgasemissionen verantwortlich ist, wird hier das Potenzial dieser Bauweise für den Klimaschutz schnell deutlich.
Lesetipp: Platte 2.0 – warum sich Gebäude in Fertigbauweise rechnen
Carbonfasern als Bewehrung langlebiger als Stahl
Die Carbonfasern, die in den Beton eingebettet werden, sind deutlich langlebiger als die übliche Bewehrung aus Stahl. Auch ihre Herstellung ist im Allgemeinen umweltfreundlicher. „Dank der neuen Leichtbauweise in Beton reduzieren wir den CO2-Fußabdruck um den Faktor zwei bis vier und sparen bis zu 75 % Material gegenüber einer herkömmlichen Bauweise“, erläutert Kurath, der auch Mitgründer des ZHAW-Spin-offs CPC ist. Dieses hat die filigranen, belastbaren CPC-Betonplatten (Carbon Prestressed Concrete) entwickelt. „Vorgespannte Carbonfasern und Beton ergänzen sich perfekt. Carbon absorbiert die Zugkräfte und Beton den Druck sowie die quer wirkenden Kräfte.“
CPC-Platten bekommen im Vergleich zu konventionell bewehrten Betonplatten bei Belastung keine Risse und federn unbeschädigt zurück. Ein weiterer Vorteil: Sie sind bei gleicher Tragfähigkeit drei- bis viermal dünner als herkömmliche Materialien. Das größte Potenzial der patentierten CPC-Platten sieht der ZHAW-Bauingenieur darin, dass sie industriell hergestellt sowie maßgeschneidert zugeschnitten werden können und nicht rosten. „Wir können weltweit als Einzige industriell Betonplatten herstellen, die zweiachsig mit Carbonfasern vorgespannt sind.“
Baukasten auf Bestellung mit Carbonplatten aus Deutschland
Zurzeit werden die CPC-Platten im ersten CPC-Werk von Holcim in Essen bei Oldenburg (Niedersachsen) hergestellt. Die Carbonfasern werden vom ZHAW-Spin-off CPC in Döttingen produziert – künftig mit biobasiertem Kohlenstoff aus nachwachsenden Rohstoffen wie Algen oder Cellulose, der ganz ohne Erdöl auskommt. „Die entwickelten Platten sollen künftig auch hierzulande produziert und das neue Bausystem breit im Hochbau eingesetzt werden können – gerade der Schweizer Markt ist dafür prädestiniert“, sagt Josef Kurath.
Lesen Sie auch, wie modulares Bauen an Massivbauten funktioniert
Wichtig für das patentierte Bausystem war auch die Entwicklung der Steckverbindungen der einzelnen Platten. Diese bestehen nur aus den Platten selbst und einem herkömmlichen Mörtel, kommen also ohne Kleber oder Stahlbauteile aus. Nun gilt die weitere Forschungs- und Entwicklungsarbeit der Optimierung für Schall- und Brandschutz sowie der speziellen Konstruktion von erdbebensicheren Gebäudekernen und großflächigen Deckenverbindungen. „Die einzelnen Deckenelemente sollen künftig wie ein Reissversschluss ineinandergreifen, sodass horizontal – ohne zusätzliche Verbindungselemente – fast endlose Ebenen möglich sind.“