Industrie druckt digital anders
Statt mit industriellem, inkjetbasiertem Digitaldruck sämtliche analogen Verfahren ersetzen zu wollen, sucht die Branche verstärkt nach originären eigenen Anwendungen.
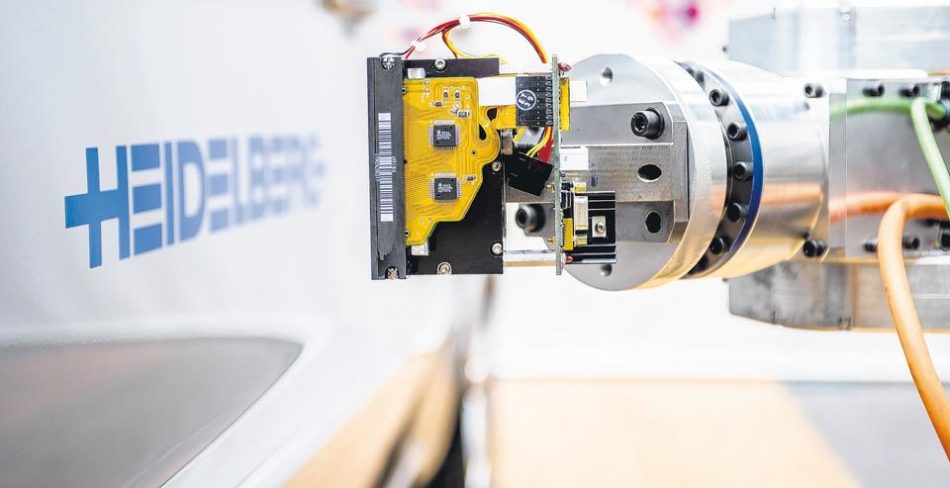
Foto: Heidelberger Druckmaschinen AG
Der digitale Produktionsdruck kommt in die Jahre. Vor rund einem Vierteljahrhundert wurden die ersten Techniken vorgestellt, mit denen Produkte während ihrer industriellen Herstellung bedruckt werden können. Von einem Markt aber kann man erst seit rund zehn Jahren sprechen.
Dabei handelt es sich um ein zartes Pflänzchen, das zwar mit 10 % bis 15 % pro Jahr wächst. Verglichen mit analogen Druckmärkten aber ist die digitale Ernte – in Volumen und Marktdurchdringung gemessen – noch sehr übersichtlich.
Der Bostoner Analyst Mark Hanley, der sich von Beginn an mit dem Thema beschäftigt, führt dafür drei wesentliche Ursachen an. Die erste sind die Märkte selbst: Die Vielzahl der komplexen und unterschiedlichen Fertigungsprozesse, in denen der digitale Tintenstrahldruck eingesetzt werden kann, bedingt ebenso unterschiedliche und meist ganz neu zu entwickelnde spezielle Druckverfahren.
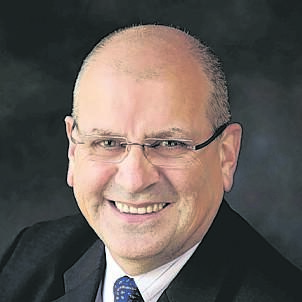
Der zweite Grund sind die Tinten. Hier sei noch viel grundlegende Entwicklungsarbeit nötig, bis passende Funktionsflüssigkeiten zur Verfügung ständen, so Hanley. Hersteller von Fußbällen, Spirituosen, Textilien, Faltschachteln, Babyfläschchen oder Lebensmittelverpackungen haben häufig einen mühsamen Weg vor sich, wenn sie auf digitalen Druck innerhalb ihrer Fertigungslinien umstellen wollen.
Die willigen Hersteller benötigen Hilfe von digitalen Druckprofis, den sogenannten Inkjet-Integratoren. Diese entwickeln bereits vorhandene Techniken mithilfe von Spezialisten für die Komponenten Tinten, Druckköpfe, Software oder Hardware zu einer individuell passenden Lösung weiter. Weltweit gibt es geschätzt jedoch nur rund 450 dieser Spezialisten.
Einer davon ist die Firma MPrint aus Baiersbronn im Nordschwarzwald. Sie hat sich im Jahr 2000 mit Digitaldruck selbstständig gemacht und ist seitdem im Etikettendruck sowie im industriellen Direktdruck tätig. „Es gibt wenig fertige Lösungen. Wir arbeiten nach dem Baukastenprinzip“, sagt Geschäftsführer Michael Morlock.
MPrint kann sich vor Kundenanfragen kaum retten: „Die Aufträge kommen aus fast allen Branchen, vom Uhrenfabrikanten über Weiße-Ware- Hersteller hin zu Werkzeug- oder Gerüstbauern“, so Morlock.
Es seien häufig die Branchenführer, die auf Digital umsteigen wollen und die bereit sind, für die größere Flexibilität und das damit mögliche schnelle Reagieren auf Marktanforderungen zu zahlen, so der MPrint-Chef. Die Mehrkosten können durchaus ein Vielfaches des analogen Drucks betragen, sei es wegen der wesentlich teureren Digitaldruckmaschinen oder auch wegen nötig werdender spezieller Vorbehandlungen des Untergrunds.
„Langfristig wird der digitale Industriedruck sicherlich die dominante, voll integrierte Technik sein. Das erfordert die Entwicklung von neuen Anwendungs- und IT-Systemen, die nur in langfristiger Kooperation mit der Industrie zustande kommen können“, sagt Analyst Hanley. Aktuell dominierten die gut funktionierenden, preisgünstigen und großserientauglichen analogen Druckverfahren. Warum also ins Risiko gehen und aufwendig in neue Druckverfahren investieren?
„Der digitale Industriedruck wird eigene Wege gehen“, sagt Hanley. „Wir sollten uns vom automatischen ‚Analog-wird-Digital‘-Gedanken befreien und der gefühlten Notwendigkeit, alles Alte durch Neues ersetzen zu wollen. Das ist in vielen Fällen nur aufwendig und teuer.“ Dafür aber werde es zunehmend Anwendungen geben, in denen der Digitaldruck analogen Techniken überlegen ist und strategische Vorteile und damit Wertschöpfung verspricht, ist Hanley überzeugt.
Ein Beispiel ist der Markt für Keramikfliesen, der sich innerhalb kurzer Zeit zu einem nahezu 100 %igen Digitaldruckmarkt entwickelt hat. Das digitale Bedrucken von Fliesen ist preisgünstiger und individueller und der Wechsel von Designs schneller möglich. Deshalb wird bereits heute so gut wie keine Keramik mehr mit den schwerfälligeren, analogen Verfahren bemustert.
Ein anderes Beispiel, in dem der digitale Tintenstrahldruck bereits seit Längerem sein volles Potenzial ausschöpft, sind großformatige Verkaufsdisplays. Individuell und schnell produziert beziehungsweise aktualisiert, machen diese Werbemittel heute mit 40 Mrd. $ Jahresumsatz rund die Hälfte des Endkundenabsatzes durch industrielle Drucktechnologien aus.
Anders sieht es bei gedruckter Elektronik aus. Bei diesem Verfahren werden aktive und passive elektronische Bauteile jeglicher Art auf nichtleitende Flächen gedruckt. Speziell in Deutschland sind aufgrund der finanziellen Förderung durch Wirtschaftsministerien und die EU eine Reihe von Unternehmen entstanden. Die verfügbaren Funktionsflüssigkeiten sind aber bislang nur begrenzt für Großserien einsetzbar. Ihre Wettbewerbsfähigkeit muss daher noch unter Beweis gestellt werden.
Im Verpackungsmarkt als größtem Einzelmarkt im Drucksegment mit einem globalen Jahresumsatz von 300 Mrd. $ kann Digitaldruck mit flexiblen Bedruckungen punkten. Sein Anteil liegt bisher jedoch nur bei rund 1 %. Der größte Teil des Marktes funktioniert nach dem Muster maximale Volumina bei niedrigsten Kosten, also analog. Dennoch setzen aktuell Großunternehmen wie HP und Landa auf das Thema.
Dabei sticht ein Teilmarkt für Verpackungen heraus, der einiges Potenzial verspricht. Das individuelle Bedrucken von Werbemitteln hat bereits jetzt ein weltweites Markvolumen von rund 60 Mrd. $ und wächst rasant weiter. Der Direct-to shape-Druck (DTS), bei dem ein Inkjetsystem mit mehreren Achsen dreidimensional auf Dosen oder Flaschen druckt, wird immer wieder gerne als attraktives Vorzeigebeispiel für die Leistungsfähigkeit von Digitaldruck hergezeigt.
DTS ist die schnelle Alternative zum Tampon- oder Siebdruck. „Wenn DTS aber plötzlich eine der kostengünstigsten Verpackungsinnovationen der letzten 40 Jahre – nämlich bedruckte Selbstklebeetiketten – ersetzen soll, ist bei aller Euphorie Vorsicht geboten“, warnt Hanley. „Die anfänglich große unkritische Begeisterung und Vorstellung, dass digitale Verfahren rasch und komplett die analogen Industriedruckprozesse ersetzen würden, macht jetzt einer realistischeren Betrachtung Platz“, stellt der Analyst fest.
Umstellungen von Technologien in Produktionsprozessen brauchen Zeit. Dabei seien Europa und speziell Deutschland aufgeschlossener und fortschrittlicher als die von Großunternehmen geprägten USA, weiß Hanley.
Marcus Timson, der vor vier Jahren mit inprint die erste Fachmesse für industrielle Drucktechnologien veranstaltete, hält Deutschland für ein im Grunde konservatives Land. Die deutsche Industrie aber zeige sich gegenüber dem Thema Industrie 4.0 aufgeschlossen.
Die kleineren und beweglicheren deutschen Mittelständler könnten besser längerfristige Visionen verfolgen als aktionärsgetriebene Großunternehmen mit ihrem quartalsweisen Erfolgsdruck, so Timson. Damit verfüge Deutschland bereits heute über einige der fortschrittlichsten Beispiele im digitalen Industriedruck.