Mehr Power für Direkt- Diodenlaser
Direkt-Diodenlaser sind energieeffizient. Doch für industrielle Einsätze sind sie oft noch zu schwach. Forscher bemühen sich daher um eine Leistungssteigerung. So auch im Förderprojekt „BrightLas“. In den letzten drei Jahren haben darin zehn Unternehmen, zwei Hochschulen und ein Forschungsinstitut modulare Direkt-Diodenlaser für die Oberflächenbearbeitung realisiert, die kleiner sind als ein Schuhkarton.

Foto: Scansonic
„Nur im eigenen Saft kochen ist nie gut“, sagt Nils Kirstaedter. Als Geschäftsführer der Berliner Lumics GmbH setzt er darum konsequent auf Forschungskooperationen mit Hochschulen und anderen Unternehmen. So auch im Projekt „BrightLas“. Gefördert im Programm „Innovative regionale Wachstumskerne“ des Bundesforschungsministeriums hat Lumics darin mit einem Dutzend Partnern aus der Region Berlin-Brandenburg drei Jahre lang das Ziel verfolgt, Diodenlaser für die industrielle Oberflächenbearbeitung fit zu machen.
Bislang reicht die Leistung der günstigen und energieeffizienten Dioden noch nicht für die Oberflächenbearbeitung von Metallen und anderen harten Werkstoffen. Die Energie muss deshalb aufwendig konvertiert werden. Als Folge sind Industrielaser so groß wie Kühlschränke, übertragen das Licht über lange Fasern auf bewegliche Roboterarme und benötigen das Dreifache der Energie, die zur Oberflächenbearbeitung tatsächlich gebraucht wird. Bei Leistungen um 10 kW, die oft im Dreischichtbetrieb abgerufen werden, schlägt sich das in enormen Stromkosten nieder.
„BrightLas“ war angetreten, um die Konvertierung in Festkörpern und die Übertragung über Fasern überflüssig zu machen. Dafür wollten die Partner die robusten, langlebigen und preiswerten Diodensysteme auf Schuhkartongröße bringen – damit sie sich direkt auf Bearbeitungsmaschinen oder Roboterarme montieren lassen. Zudem hatten sich die zehn Unternehmen, zwei Unis und das Ferdinand-Braun-Institut für Höchstfrequenztechnik in dem Projekt das Ziel gesetzt, die Leistung marktüblicher Laserdioden um satte 50 % zu steigern.
Nicht alle Pläne sind laut Projektsprecher Kirstaedter aufgegangen. „Die Systeme sind zwar kleiner als ein Schuhkarton, doch die 50 % Leistungssteigerung haben sich als zu hoch gesetztes Ziel erwiesen“, berichtet er. Das Potenzial sei da. Noch allerdings stehe der Nachweis aus, dass die Hochleistungsdioden die nötige Lebensdauer erreichen. Tausende Stunden dauern solche Tests. „Das zieht die Entwicklungsdauer in die Länge“, erklärt er.
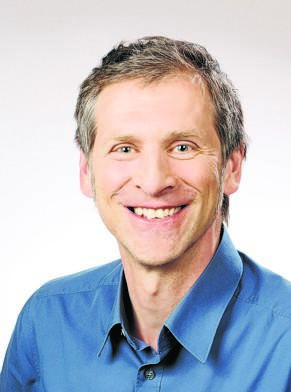
Knackpunkt für die Lebensdauer ist die Abführung der Wärme aus den Systemen – eine Problematik, die nicht nur der weiteren Leistungssteigerung von Laserdioden im Wege steht, sondern auch Entwicklern von Computerprozessoren Kopfzerbrechen bereitet. Das Forschungsprojekt hat in dieser Frage positive und negative Erkenntnisse geliefert. So erweisen sich Hochleistungswärmesenken aus Kupfer-Diamant, welche die Firma Cicor Microelectronics beisteuerte, wider Erwarten als ungeeignet. Sie dehnten sich zu stark aus und ließen die Laserdioden reißen. Besser lief es mit Silberloten im Nanomaßstab, die Forscher der TU Berlin als Wärmesenken entwickelt haben. Sogar so gut, dass Lumics und andere Laserhersteller die Lote gern serienmäßig einsetzen würden. „Denn damit lassen sich Wärmesenken um Faktor 3 kleiner realisieren“, berichtet Kirstaedter. Für die Forscher war die positive Resonanz der Anstoß, ein Spin-off zu gründen. Unter dem Namen Nano-Join gehen sie nun die Vermarktung ihrer Silbersinterpasten an.
Vor allem aber sind aus dem Projekt neue, modulare Direkt-Diodenlaser hervorgegangen. So hat Lumics jüngst ein neues 1,6-kW-Modul vorgestellt. Und der Berliner Projektpartner DirectPhotonics Industries (DPI) präsentierte ein 500-W-Modul mit einer Strahlqualität 8 mm Milliradient (mrad), das sich dank integrierter Elektronik einfach zum Multi-Kilowatt-System zusammensetzen lässt. Einsatzgebiete: Schneiden und Schweißen weicher Materialien. Wobei ein weiterer Industriepartner, der Chemnitzer Sondermaschinenbauer Sitec, die Module auch schon für das Schneiden dünner Bleche nutzbar gemacht hat. Eine entsprechende Anlage mit den DPI-Dioden hat Sitec letzten Herbst auf Fachmessen vorgestellt.
Ein weiteres Laserhärtkopfsystem zum Löten und Schweißen von Feinblechen mit Direkt-Dioden haben die Partner Scansonic MI GmbH und Lumics im Projekt entwickelt, wobei diese auch gesellschaftlich miteinander verbunden sind. Scansonic ist seit 2012 größter Anteilseigner von Lumics.
Neben der Leistungserhöhung der Dioden hatten sich die Projektpartner vorgenommen, die Dioden optisch mithilfe des sogenannten „dichten Wellenlängen-Multiplexings“ zu verstärken. Holographisch strukturierte Linsen sollten die Lichtwellen der Einzeldioden exakt übereinander lagern. „Die hohe Komplexität und unsere begrenzten Ressourcen haben uns dazu bewogen, ein vereinfachtes Multiplexing umzusetzen“, so Kirchstaedter. Statt der geplanten dichten Wellenlängenabstände im Sub-Nanometerbereich begnügen sich die Partner mit Abständen der überlagerten Wellen von 25 nm. Dafür sind nicht die ursprünglich geplanten Volumengitter im Einsatz, da deren extrem komplexe Anpassung für das Projekt zu zeitaufwendig war. Im Sinne des Projekterfolgs wählten die Partner eine gröbere Variante, das „Coarse Wavelength Multiplexing“. Auch hier werden Lichtwellen mithilfe exakter Brechungsindexmodulation überlagert. Allerdings sind es aufgrund des um das 100-fache gröberen Rasters weniger Wellen als geplant. Folge: Die Strahlqualität ist wegen der mangelnden Überlagerung geringer als erhofft.
BISHER KONNTE DIE LEISTUNG UM 10 % GESTEIGERT WERDEN
Deshalb und wegen der nur teil-entschärften Problematik der Wärmeabführung war das ambitionierte Ziel von 50 % Leistungssteigerung nicht zu erreichen. „Wir haben 10 % erreicht, wobei Lebensdauertests für leistungsstärkere Systeme laufen“, so Kirstaedter. Der Projektsprecher ist vor dem Hintergrund der letzten drei Jahre sicher, dass es schon in naher Zukunft Direkt-Diodenlaser geben wird, die auch dickere Metalle schneiden und bohren können. „Wir haben gesehen, dass es mit entsprechenden Ressourcen machbar ist“, sagt er. Kompakte Dioden-Strahlquellen für Materialbearbeitungsprozesse, in denen eine Strahldivergenz 25 mm mrad genüge, habe „BrightLas“ bereits hervorgebracht. Für das Härten und Löten von Metallen seien diese ebenso geeignet wie für alle erdenklichen Verfahren zur Bearbeitung von Kunststoffen.
Neben Nano-Join ist zudem eine weitere Gründung aus dem Projekt hervorgegangen: Die aus der TU Berlin ausgegründete Gefertec GmbH. Die Gründer haben sich im Projekt zur Scansonic- Gruppe gefunden, die sich umgehend an ihrem Start-up beteiligt hat. Die junge Firma ist auf additive Fertigung großvolumiger Metallbauteile spezialisiert. Wobei in ihrem Verfahren nicht Laser ein Metallpulver verschmelzen, sondern Draht in einem CNC-Kurzlichtbogenprozess zum Bauteil verschmolzen wird.
„Auch wenn nicht alle Ziele erreicht wurden, haben wir in den drei Jahren einen schönen regionalen Wachstumskern entwickelt“, resümiert Kirstaedter. Auch, weil die Netzwerke zwischen den Partnern tragfähiger geworden seien. Denn das gemeinsame, zielgerichtete Herangehen an Innovationen belebe die Forschung und Entwicklung aller beteiligten Partner.