Fraunhofer-Forscher verkürzt den Weg zum fertigen Bauteil
Neun einfache Zeichen sollen helfen, einige der zahlreichen Prozessschritte von der ersten Skizze bis zum fertigen Bauteil einzusparen. Einstellungen an der Maschine entfallen.

Foto: Fraunhofer IPA/Rainer Bez
Zwischen der ersten Skizze und dem fertigen Bauteil liegen stets zahlreiche fehleranfällige Prozessschritte und viel Arbeitszeit: Zunächst wird seitens der Konstruktion ein dreidimensionales CAD-Modell angefertigt. Daraus leitet der Mitarbeitende dann eine zweidimensionale technische Zeichnung ab und ergänzt sie um zusätzliche Angaben: Toleranzen, Passungen, Parallelitäten, die Rauigkeit der Oberfläche und dergleichen mehr. CAD-Modell und technische Zeichnung werden dann dem Fertiger übergeben. Dieser nimmt bei einfachen Bauteilen die entsprechenden Einstellungen direkt an der Maschine vor.
Bei komplexeren Geometrien hingegen empfiehlt es sich, die Daten in eine CAM-Software zu laden, die daraus dann automatisiert Maschinenbefehle generiert. Welche Fräser und Bohrer geeignet sind, um das Rohmaterial zu bearbeiten und wie das Rohteil am besten eingespannt werden muss, muss der Fertiger aber selber entscheiden.
Lösung vom Fraunhofer IPA ersetzt CAD-Modell durch eine Nomenklatur
Tobias Herrmann von der Abteilung Leichtbautechnologien am Fraunhofer-Institut für Produktionstechnik und Automatisierung IPA hat nun einen Weg gefunden, wie in Konstruktion und Fertigung einige dieser vielen Prozessschritte eingespart werden können. CAD-Modell und technische Zeichnung werden dabei ersetzt durch eine Nomenklatur aus neun grundlegenden Zeichen, mit denen alles angegeben werden kann, was eine Fräsmaschine umsetzen soll. Diese Zeichen schreibt eine Werkerin oder ein Werker mit einem Stift direkt auf das Rohmaterial: R5 steht zum Beispiel für eine Rundung mit einem Radius von 5 mm, F20 für eine 20 mm breite Fase oder E10 für eine Ausfräsung von 10 mm, deren exakte Form und Abmessung anhand von Linien auf dem Rohmaterial vorgegeben sind.
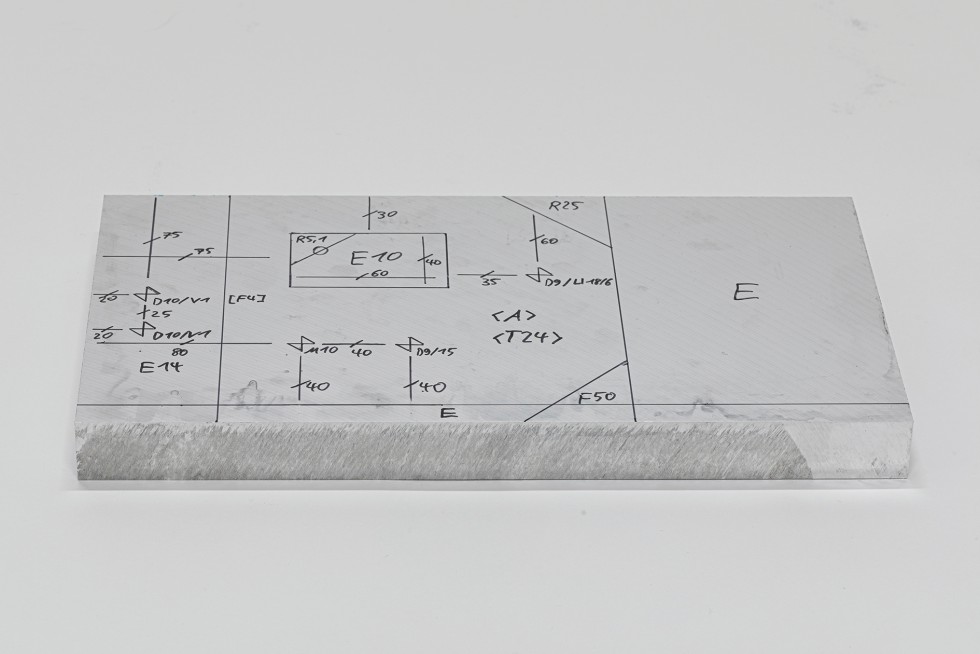
Hinzu kommen neun Konventionen – etwa dass beim Zeichnen von Konturen und Features nur Linien in einem Winkel von 0°, 45° oder 90° zulässig sind, oder dass sich der Werkstücknullpunkt aus Sicht des Maschinenbedieners immer in der linken oberen Ecke befindet.
EasyCNC: Scanner erfasst Bauteil bevor Software den NC-Code erstellt
Ist das Rohmaterial beschriftet und eingespannt, wird es von einem Laserscanner abgetastet. Dabei wird zunächst ein Grobscan durchgeführt, um Bauteilposition und Größe zu bestimmen. Anschließend folgt ein Feinscan, bei dem die Markierungen auf dem Bauteil erfasst werden. Gibt es dabei Probleme, etwa durch Verschmutzungen auf dem Bauteil, reinigt die Fräsmaschine das Rohmaterial selbstständig und scannt es dann erneut ab.
Lesetipp: Studie nennt Maßnahmen gegen Cyberangriffe auf CNC-Maschinen
Die erkannten Zeichen werden interpretiert und daraus eine Vektorgrafik abgeleitet. Danach übersetzt eine Software binnen weniger Sekunden die Vektorgrafik in Maschinenbefehle (NC-Code) und erstellt ein Soll-Bauteil als CAD-Modell. In den Maschinenbefehlen enthalten sind nicht nur genaue Angaben darüber, an welcher Stelle die Maschine mit welchem Werkzeug was tun soll, sondern die Software sieht auch Werkzeugwechsel vor. Sie schreibt also vor, an welcher Stelle die Maschine andere Fräser oder Bohrer zu verwenden hat.
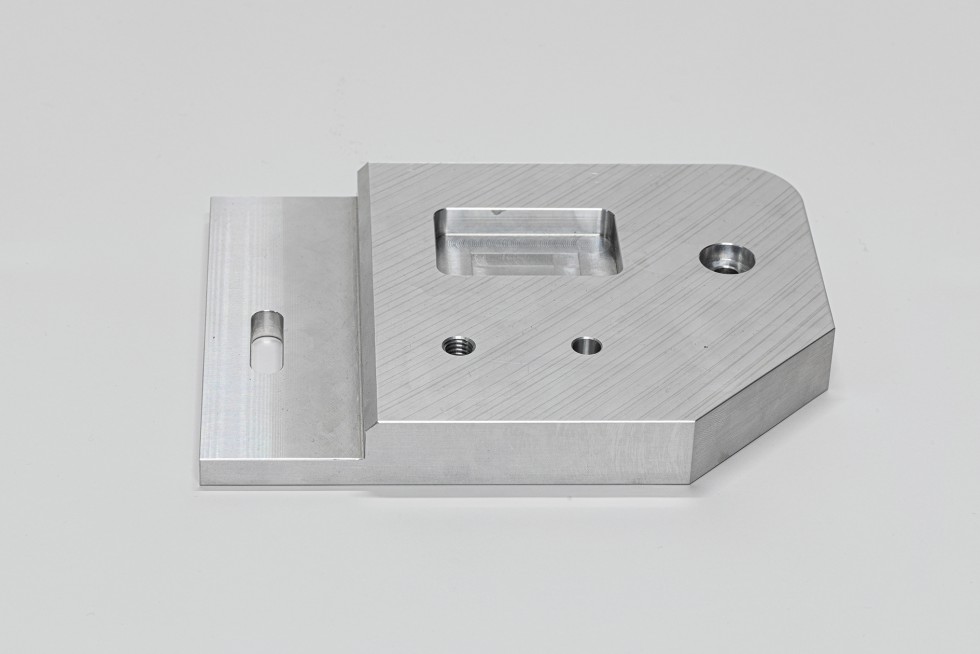
Ist das Rohmaterial bearbeitet, greifen weitere Maßnahmen zur Qualitätssicherung: Zunächst wird das Werkstück automatisch gereinigt, um Staub und Späne zu beseitigen. Danach wird es vom Laserscanner einmal mehr abgetastet und kontrolliert, ob die ermittelte Bauteilformgebung mit dem zuvor berechneten Soll-Bauteil übereinstimmt. Wird dabei festgestellt, dass nicht alle Bearbeitungsschritte ausgeführt wurden, da beispielsweise während der Bearbeitung ein Bohrer gebrochen ist, wird dem Maschinenbediener eine entsprechende Meldung angezeigt. Sobald der Bediener den entsprechenden Bohrer ausgetauscht hat, holt die Fräsmaschine alle Bearbeitungsschritte nach, die sie zuvor nicht korrekt abarbeiten konnte.
Mit diesen Eigenschaften wäre „EasyCNC“, wie Tobias Herrmann seine Entwicklung nennt, nicht nur eine Abkürzung zum fertig bearbeiteten Bauteil, sondern auch ein Mittel gegen den grassierenden Fachkräftemangel. Denn EasyCNC überträgt das Fachwissen erfahrener Konstrukteure und Fertiger in Softwarebefehle. „Das Know-how zur Bearbeitung ist damit nicht mehr in den Köpfen der Konstrukteure und Fertiger, sondern in der Maschine und Software gespeichert“, sagt der Forscher. „Es könnte also künftig auch ungelerntes oder unerfahrenes Personal an den Maschinen eingesetzt werden.“
Zugriff auf Bestandsmaschinen soll eine Zwischensteuerung übernehmen
Bis es soweit ist, sind allerdings noch einige offene Fragen zu klären. Allen voran: Wie bekommt man Zugriff auf alte CNC-Maschinen? Denn Bestandsmaschinen sind oft nicht auf die Digitalisierung ausgelegt. Es ist nicht vorgesehen, dass externe Systeme auf diese zugreifen und ihnen Befehle erteilen. Herrmann versucht nun, die Maschinenbefehle über eine Zwischensteuerung zu beeinflussen. Darüber könnten CNC-Maschinen dann auch auf Netzwerke und Datenbanken zugreifen. Zusätzlich können damit Anleitungen und Anweisungen an den Maschinenbediener weitergegeben werden. Um dies umzusetzen, sind jedoch noch viele Tests zur Maschinenkommunikation und Systemintegration notwendig.
Unterdessen verfeinern Herrmanns Projektpartner bei der EVT Eye Vision Technology GmbH, einem Anbieter von Machine-Vision-Lösungen, ihre Deep-Learning-Algorithmen weiter. Denn die Algorithmen, welche die Linien und Zeichen auf dem Rohteil in Verbindung mit einem von EVT entwickelten Laser-Scanning-System erkennen und klassifizieren, sind essenziell für die weiteren Verarbeitungsschritte. Parallel dazu entwickelt Projektpartner Reuss Maschinenbau GmbH & Co. KG derweil den Prototyp einer Fräsmaschine, in die das Laser-Scanning-System zusammen mit Einrichtungen zur Bauteilreinigung und der zusätzlichen Steuerungsanbindung integriert werden soll. Geplanter Projektabschluss ist der 30. September 2023.