Hydraulik bringt Windenergie zum Generator
Wenn große Kräfte und Drehmomente übertragen werden, dann sind oft hydraulische Lösungen im Spiel. Was bei Baumaschinen schon lange üblich ist, könnte auch in Windenergieanlagen funktionieren. Mitsubishi ist dabei, einen ersten Prototypen mit 7 MW und hydrostatischem Getriebe zu errichten. Auch an der RWTH Aachen wird geforscht.
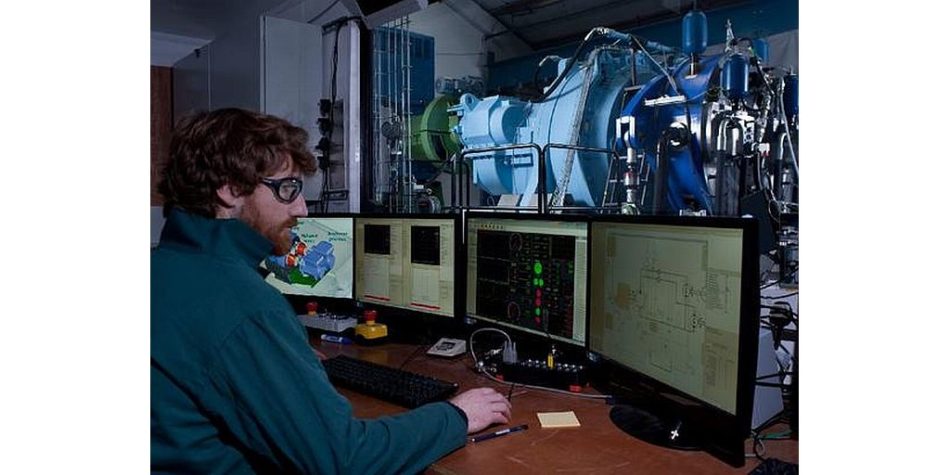
Foto: Control Techniques/Emerson
Fluidtechniker schätzen die Vorzüge der Hydraulik und so wird an hydrostatischen Getrieben für Windenergieanlagen auch schon länger mit unterschiedlicher Intensität getüftelt. Auftrieb versprechen sich die Akteure nun vor allem im Offshorewindgeschäft durch den Wegfall der mechanischen Getriebe und dem reduzierten Bedarf an Leistungselektronik und Stahl. Im Idealfall sollen robuste hydrostatische Antriebe durch einen modularen Aufbau auch die Wartungskosten auf See reduzieren.
In Japan hat Mitsubishi (MHI) 2013 Prototypen mit 2,4 MW und Digital Displacement Transmission errichtet. Im schottischen Hunterston soll nun eine Anlage mit 7 MW folgen. Der Turm hat am Flansch einen Durchmesser von 7,33 m und wird von der Ambau GmbH gefertigt. Die 81,6 m und 32,5 t schweren Rotorblätter kommen von der Berliner Euros Entwicklungsgesellschaft für Windkraftanlagen und wurden auf Rügen gefertigt.
Entwicklungen laufen zudem an der RWTH Aachen, der TU Delft und bei ChapDrive. tt
Zur engeren Wahl gehören bisher mehrhubige Radialkolbenpumpen, die pro Umdrehung ein großes Schluckvolumen erreichen können und direkt vom Rotor angetrieben werden. Dabei wird die mechanische Kraft in einen Hochdruck-Ölvolumenstrom umgewandelt und von Hydromotoren wieder in eine konstante mechanische Leistung für den Antrieb des Generators überführt. Das Drehmoment der Pumpe ergibt sich dabei aus dem Systemdruck und dem eingestellten Verdrängungsvolumen.
Der Schlüssel dazu ist, dass die Motoren oder Pumpen ein variables Schluckvolumen haben müssen und so eine stufenlose Änderung der Übersetzung in unterschiedlichen Lastbereichen ermöglichen. Durch die konstante Drehzahl am Generator würden zum einen Synchronmaschinen reichen und die teuren Frequenzumrichter wegfallen. Auf der Habenseite der hydrostatischen Konzepte stehen außerdem die großen Energiedichten, die hohe Lebensdauer oder kompakte Bauweisen.
Tief im Soll steht allerdings die Effizienz der Energieumwandlung. Sobald die Systeme nicht mehr im optimalen Bereich arbeiten, gehen die Wirkungsgrade im Teillastbereich rapide nach unten. Dieses Optimum betrifft den Druck, die Drehzahl und das Verstellvolumen. Mit einiger Spannung werden daher die Prototypen von Mitsubishi (MHI) erwartet. Eine Maschine soll auf einem Testfeld in Großbritannien errichtet werden und eine andere auf einem schwimmenden Fundament vor der Küste von Fukushima. Der dafür vorgesehene stählerne Halbtaucher wird gerade auf einer Werft in Japan gebaut.
Mit ihrem hydraulischen Antriebsstrang, 7 MW Leistung und einem Rotordurchmesser von 167 m ist die „Sea Angel“ ein Exot unter den neuen Prototypen. „Es ist ein völlig neues hydrostatisches Antriebskonzept“, verspricht Jamie Taylor, Projektmanager von Artemis Intelligent Power. Um die schlechten Wirkungsgrade im Teillastbereich in den Griff zu bekommen, haben die Schotten eine digitale Mehrhubpumpe (Digital Displacement Pump, DDP) entwickelt. Das Unternehmen wurde 2010 von MHI übernommen.
Die langsam laufende DDP mit einem Volumendurchsatz von 7000 l/min sitzt an der Rotorwelle und hat 168 Kolben. Während die Pumpe mit der Rotordrehzahl angetrieben wird, laufen die Kolben mit 300 Hüben/min. Die dahinter angeordneten Synchrongeneratoren mit jeweils 3,5 MW werden von zwei digitalen Hydromotoren angetrieben, in denen jeweils 36 Kolben stecken. Dabei lassen sich sowohl die Pumpe als auch die Motoren steuern. Zusätzlich ist noch ein hydraulischer Druckspeicher installiert, der beispielsweise Lastspitzen auffängt.
Die besseren Wirkungsgrade werden durch eine digitale Ansteuerung der einzelnen Kolben erreicht. Dafür sitzen auf allen Kolben Mikroprozessoren, die ähnlich wie bei der Einspritzung von Dieselmotoren die Ein- und Auslassventile steuern. „Der optimale Arbeitsbereich liegt zwischen 250 bar und 350 bar. Das Verdrängungsvolumen und der Druck werden automatisch von einem Rechner gesteuert“, erklärt Taylor. „Dafür erhält das System die Sensorsignale von der Welle und kennt so die exakte Position der Kolben. Darüber lassen sich die Zylinder zum richtigen Zeitpunkt ansteuern und das Schluckvolumen sehr schnell verstellen. In Abhängigkeit vom Rotordrehmoment können beide oder nur ein Generator angetrieben werden, was die Verluste weiter begrenzt“, so der Projektmanager.
Wenn z. B. das Schluckvolumen reduziert wird, nimmt das System immer mehr Kolben von der Hochdruckleitung und schließt sie über das Einlassventil an den Niederdruck an. Bei konventionellen Hydraulikmaschinen wird das Verdrängungsvolumen hingegen durch eine Reduzierung des Kolbenschubs erreicht. Weil diese dann weiter unter Druck arbeiten, entstehen Leistungsverluste durch Reibung oder Leckage.
Bei dem System von Artemis laufen die abgeschalteten Kolben hingegen ohne Druck im Leerlauf, was zu den besseren Wirkungsgraden führt. Laut Hersteller ist der Antrieb darauf ausgelegt, jederzeit das vorhandene Drehmoment des Rotors in Energie umzuwandeln. Dafür könne es schon bei einem sehr geringen Schluckvolumen von 1 % den optimalen Arbeitsdruck aufbauen. Zumindest am Teststand hat das Konzept laut Taylor einen Gesamtwirkungsgrad der Pumpe von 94 % erreicht.
Das wäre immer noch ein Verlust von 6 % und mehr als in mechanischen Getrieben verloren geht. Unter anderem die reduzierten Lasten sollen das wieder einspielen. „Im Multimegawattbereich mit sehr großen Rotordurchmessern werden die Planetenstufen sehr stark beansprucht. Beim hydrostatischen Antrieb wird die Last hingegen gleichmäßig übertragen und lässt sich flexibel verteilen. Das ist ein Vorteil“, verdeutlicht Johannes Schmitz vom Institut für fluidtechnische Antriebe und Steuerungen (IFAS) an der RWTH Aachen.
Mit Fördermitteln des Bundesumweltministeriums hatte auch das IFAS in einem zweijährigen Forschungsprojekt ein hydrostatisches Getriebe für Windenergieanlagen entwickelt und einen Teststand mit 1 MW gebaut. Dabei laufen zwei Radialkolbenpumpen mit der Rotordrehzahl und sorgen über Motoren für konstante Umdrehungen am Stromerzeuger. Durch die stufenlose Änderung des Übersetzungsverhältnisses lässt sich dem Rotor zudem die gewünschte Drehzahl aufprägen. „Wir lassen vorne mehr Leistung zu, die nach hinten über den Druck begrenzt wird. So lässt sich die Leistung von 1 MW lange konstant halten und es entstehen keine Überlastungen am Generator“, sagt Schmitz. Das Konzept ist weniger aufwendig als die Lösung von MHI, denn die Steuerung läuft über das verstellbare Schluckvolumen der Hydromotoren. „Die Pumpen fördern nur den Volumenstrom und der Druck entsteht erst an den Motoren. Bei wechselnden oder sehr kleinen Drehmomenten lässt sich die konstante Leistung am Generator nur erreichen, wenn sich das Schluckvolumen reduzieren lässt. Dafür können die Kolben im Block abgeschaltet sowie eine oder beide Pumpen betrieben werden.“
Bei einem maximalen Druck von 350 bar liege der optimale Arbeitsbereich in einer Spanne zwischen 180 bar und 250 bar. Von Welle zu Welle wurde auf dem Teststand ein Gesamtwirkungsgrad von 86 % erreicht. Das liege auch daran, dass es kaum Komponenten gibt und die für den Teststand optimierten Pumpen aus Minenbaggern stammen. In einem Anschlussprojekt, das aus Forschungsmitteln des VDMA finanziert wird, geht es daher nun um die Redundanz und Optimierung der Komponenten. Schmitz weiß: „Die Anforderungen in der Windenergie sind hoch. Wenn an den robusten hydraulischen Systemen doch etwas kaputt geht, dann ist es meist die Elektronik.“