Redox-Flow-Batterien zum Sparpreis
Redox-Flow-Batterien eignen sich als Stromspeichertechnik hervorragend, um größere Mengen regenerativer Energien zu speichern. In der Praxis ist dies jedoch eher ein Nischenmarkt, auch weil die Anlagen vergleichsweise teuer sind. Forschende des Fraunhofer-Instituts für Umwelt-, Sicherheits- und Energietechnik (Umsicht) haben jetzt den Stack vollständig re-designt und konnten so Materialeinsatz und Kosten massiv senken. Dafür hat das Team gestern einen der drei Joseph-von-Fraunhofer-Preise in diesem Jahr erhalten.
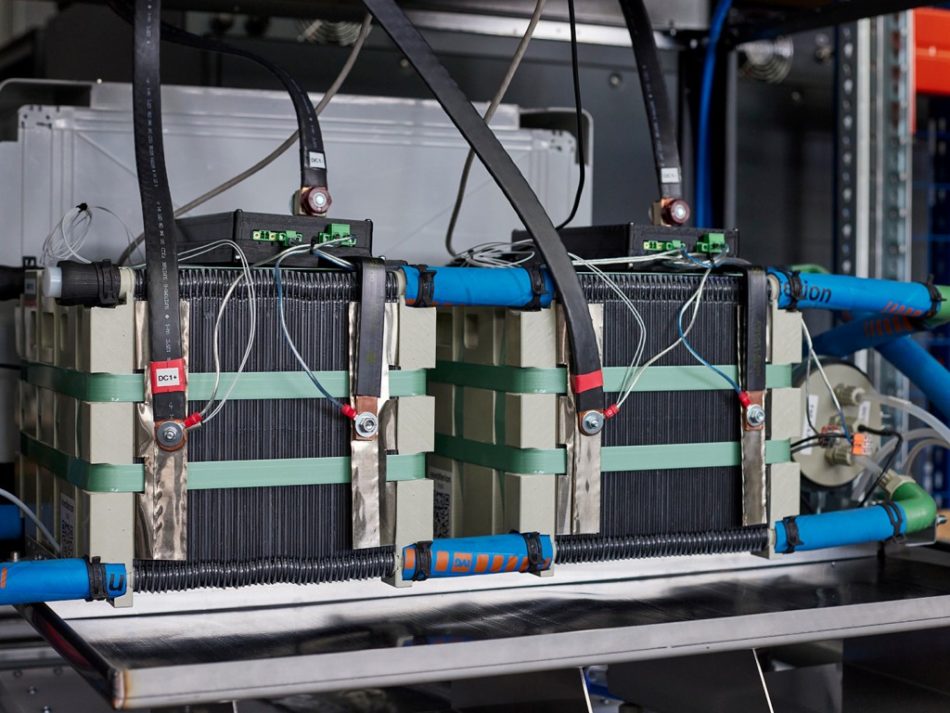
Foto: Fraunhofer/Piotr Banczerowski
Der Bedarf an Stromspeichern steigt mit dem Voranschreiten der Energiewende. Eine der Optionen neben der mittlerweile als Massenmarkt etablierten Lithium-Ionen-Technologie sind Redox-Flow-Batterien. Diese gelten als zyklenstabil – ihre Kapazität nimmt also auch nach Tausenden Zyklen nicht merklich ab. Zudem besteht keine Brandgefahr: Dies hatte vor Jahren zu einer Qualitätsdiskussion im Bereich von Lithium-Ionen-Hausspeichern zum Anschluss an Photovoltaik-Dachanlagen geführt. Zudem lassen sie sich in puncto Leistung und Kapazität auf den Bedarf auslegen und es gibt Umweltvorteile im Sinne einer Kreislaufwirtschaft: Es braucht keine kritischen Materialien, ihre Elektrolyte können, so die Fraunhofer-Gesellschaft „vollständig zurückgewonnen werden“.
Was bisher fehlt, ist der Massenmarkt. Redox-Flow-Batterien, so viel ist klar, sind eine gute Lösung für größere Strommengen Also geht es nicht um den Einsatz in Pkw oder im Haussegment. Aber in Gewerbe und Industrie täte sich ein attraktiver Wachstumsmarkt auf – wenn denn diese Technologie bisher nicht so teuer wäre.

Christian Doetsch und Lukas Kopietz vom Fraunhofer-Institut für Umwelt-, Sicherheits- und Energietechnik (Umsicht) sowie Thorsten Seipp von der Volterion GmbH & Co. KG erhielten gestern einen von drei Joseph-von-Fraunhofer-Preisen 2021 (s. Kasten), weil sie dieses Problem nachhaltig lösen konnten.
Redox-Flow-Technik bald kompakter, preiswerter und leichter
Die drei Preisträger haben die Herstellungsweise des zentralen elektrisch leitfähigen Kunststoffs neu konzipiert, sodass dieser flexibel bleibt und sich verschweißen lässt. Und dieses neuartige Verfahren hat erhebliche Auswirkungen auf die Redox-Flow-Batterien. „Der entwickelte Stack, das Herzstück einer jeden Redox-Flow-Batterie, ist von den Materialkosten her 40 % günstiger, auch die Produktionskosten konnten deutlich gesenkt werden. Der Stack wiegt 80 % weniger als ein herkömmlicher Stack und ist nur etwa halb so groß“, fasst Doetsch zusammen. Vermarktet wird der Stack vom Spin-off Volterion.
Üblicherweise bestehen die Stacks aus 160 gestapelten Komponenten, die mit einer Vielzahl von Schrauben und massiven Metallplatten zusammengehalten und mit zahlreichen Dichtungen abgedichtet werden. Ein Teil dieser Komponenten wird spritzgegossen und ist aufgrund der für den Spritzguss notwendigen hohen Drücke und Temperaturen spröde wie eine Bleistiftmine. Um dies zu umgehen, verwendet das Forscherteam zwar ähnliche Ausgangsstoffe, also Grafite und Ruße, ging aber auf andere Art und Weise an den Prozess heran: Pelletförmiger Kunststoff wird auf bis zu -80 °C gekühlt, zu Pulver zermahlen und mit 80 Gewichtsprozent Grafit gemischt. Das entstehende Pulver schickt das Forscherteam durch ein System aus mehreren Walzen mit verschiedenen Temperaturen und Geschwindigkeiten, dort wird es kurz aufgeschmolzen, geknetet, zu einer „Endlos-Platte“ gewalzt und schließlich aufgerollt.
Preiswürdiger Batteriestack ohne Schrauben und Dichtungen
„Das neue Material erhält dabei thermoplastische Eigenschaften, es ist also biegsam und verschweißbar, obwohl der Kunststoff nur einen Anteil von 20 % hat“, erläutert Kopietz. Der Stack kommt somit ohne eine einzige Dichtung aus, auch Schrauben sind überflüssig – die Zellen werden einfach miteinander verschweißt. Ein weiterer Vorteil: Über diese Methode lassen sich Bipolarplatten nicht nur deutlich schneller und damit kostengünstiger herstellen, es gibt auch keine Größenbegrenzung mehr. Bipolarplatten mit bis zu mehreren Quadratmetern sind problemlos möglich.
Der kostensenkende Schritt war die Entwicklung eines kontinuierlichen Produktionsverfahrens: das Pulver-zu-Rolle-Verfahren, in dem sich die Bipolarplatten als Endlos-Rolle fertigen lassen. Auf diese Weise lassen sich sehr dünne Platten herstellen. Ist die Plattendicke beim Spritzgießen produktionsbedingt auf mehrere Millimeter begrenzt, kann sie beim Pulver-zu-Rolle-Verfahren zwischen 0,1 mm und 0,4 mm dünn werden. Es ist also deutlich weniger Material notwendig, was den Preis wiederum senkt und leichtere kompaktere Stacks ermöglicht.