Wie der Aufzug schnell in den Schacht kommt
Manche Menschen haben bereits ein mulmiges Gefühl, wenn sie in einen Aufzug steigen. Das kennen die Roboter nicht, die sich in den leeren Schacht begeben, noch bevor die erste Kabine ihre Arbeit aufnimmt. Sie übernehmen die Vorarbeit, bevor die Aufzüge eingebaut werden.
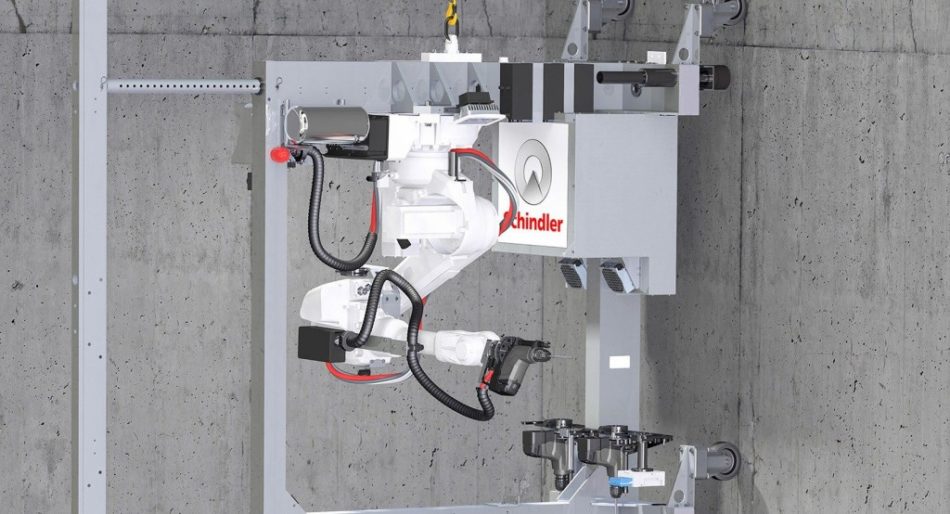
Foto: Schindler Deutschland
Leer, grau und mitunter sehr tief sind die Aufzugschächte in den Hochhäusern der Welt, wenn die Aufzugbauer ihren Job beginnen. Blanker Beton muss dann zunächst mit Bohrungen versehen werden, an denen später die Führungsschienen und andere Teile der Aufzugtechnik montiert werden. Das ist eine monotone Aufgabe und riskant zudem, weil die Arbeitsbedingungen alles andere als leicht sind. Dennoch müssen die Löcher exakt positioniert sein, damit später die Metallteile passgenau montiert werden können. Das ist eine Aufgabe, die mit gleichbleibender Präzision gut durch Automatisierungstechnik gelöst werden kann, dachte sich Aufzughersteller Schindler mit Hauptsitz im schweizerischen Ebikon. Seit kurzem setzt das Unternehmen dafür deshalb Roboter ein.
Robotics Installation System for Elevators nennt der Aufzugbauer die Lösung oder kurz Schindler RISE. Im Grunde handelt es sich dabei um einen über Kopf hängenden Sechsachsroboter, wie man ihn auch aus Fabrikhallen kennt. Dieser ist mit einer Plattform verbunden, die sich an der Wand des Aufzugsschacht bewegen und verankern kann. Das System vermisst dabei automatisch seine Umgebung. Ebene für Ebene arbeitet sich die Plattform an einem Seil hängend dann im Schacht voran, bohrt die notwendigen Löcher in den Beton und setzt die Ankerbolzen zur präzisen Montage der Führungsschienen. Ein Scanner erkennt dabei Stahlbewährungen in den Betonwänden und weitere Sensoren sammeln Parameter beim Einsatz der Roboter. Mittels künstlicher Intelligenz lernen die Maschinen damit, sich immer besser auf die Arbeitsbedingungen anzupassen.
Höhere Sicherheit für Aufzugbauer
Den ersten Prototyp des Robotersystems hat Schindler bereits 2018 vorgestellt. Inzwischen kam die Lösung laut Hersteller bereits in mehreren Gewerbekomplexen und hohen Wohngebäuden in Europa zum Einsatz. Bis zu 107 m Höhe bewältigt das Installationssystem demnach. Das entspricht 37 Etagen. Der Roboter ist dabei so ausgelegt, dass er abwechselnd auf die benötigten Werkzeuge zum Scannen, Bohren und Befestigen der Bolzen in der Betonwand zugreifen kann. Auf einer Etage angelernt, wiederholt die Installationsplattform den Prozess auf allen Ebenen des Aufzugschachtes. Das erhöht die Arbeitssicherheit für die Aufzugbauer, denn sie können die Vorarbeiten aus sicherer Entfernung an einem Monitor überwachen. Statt sich mit staubigen Bohrarbeiten abmühen zu müssen, können sie sich anschließend direkt an die Montage der Führungselemente machen. Dazu steht ihnen eine weitere Plattform zur Verfügung, die sie von einer Arbeitsebene zur nächsten transportiert, bis schließlich die Aufzugkabine eingesetzt werden kann.
Mobile Roboterplattformen im Trend
Auch andere Industriebranchen finden Interesse an mobilen Roboterlösungen. Statt in die Höhe, geht es dabei allerdings auf der Ebene durch Fabriken und Lagerhallen. Meist handelt es sich dabei um Kombinationen aus batteriebetriebenen, mobilen Plattformen und einem Roboterarm. Weil dabei schon einmal Dinge ungeplant im Weg stehen können oder Menschen den Weg der Roboter kreuzen, benötigen solche Systeme zusätzliche Sensorik zur Vermeidung von Kollisionen.
Hersteller solcher Systeme verfolgen unterschiedliche Strategien. Stäubli beispielsweise setzt auf eine Lösung aus einer Hand und nennt ihre Lösung HelMo. Automatisierungsspezialist Pilz bevorzugt dagegen Systemoffenheit und Robotermodule, die über die offene Roboterschnittstelle ROS miteinander sowie Modulen anderer Hersteller kombiniert werden können.