Corona: Der Stoff, aus dem die Masken sind
In Troisdorf produziert die Firma Innovatec einen heiß begehrten Stoff – das Meltblown-Vlies, Herzstück aller medizinischen Masken. Ein Smartphone-Rundgang vor Ort.

Foto:Innovatec
Pünktlich um 10 Uhr klingelt es. „Annehmen?“, fragt Facetime, der Videotelefoniedienst von Apple. Klar, annehmen. Und dann erscheint ein freundliches Gesicht mit herabhängender Maske auf dem Bildschirm. Daniel Krumme, Geschäftsführer der Firma Innovatec, hält sein Smartphone ganz ruhig. Der Himmel in Troisdorf, zwischen Bonn und Köln, ist strahlend blau an diesem Montagmorgen. Noch steht Krumme vor der Halle, in der die Firma einen der zurzeit begehrtesten Produkte der Welt herstellt: Meltblown-Vlies – der Stoff aus dem die Masken sind.
Es ist das Troisdorfer Fasergebilde, das – eingebettet in andere Vliese – verhindern soll, dass bei den grün-weißen OP-Masken oder den höherwertigen Halbmodellen, den FFP-Masken (Filtering Face Piece), Bakterien und Viren ein- oder ausdringen. Jeder, der in diesen Tagen eine medizinische Maske trägt, kennt die Krux: Zum einen soll viel anhaften und nichts zu Nase und Mund gelangen, zum anderen sollen die Träger auch noch Luft bekommen. Krumme lacht: „Das ist genau unser Know-how. Das machen wir seit 20 Jahren.“
Mit dem Smartphone dabei
Auf unserem Weg in die Produktionshalle geht es vorbei an größeren und weniger großen Rollen, die hier im Trockenverladebereich lagern. Dann erkenne ich Teile von Anlagen. „Ich zeig Ihnen jetzt mal, wo der Prozess beginnt.“ Krumme erklimmt einige Treppenstufen. Es geht in den ersten Stock der rund 12 m hohen Anlage. Ein lautes, surrendes Geräusch begleitet uns.
„Können Sie mich hören? Sehen Sie das? Das ist der Extruder.“ Ich höre Krumme nicht mehr. Das Handybild gleitet über ein paar geknickte Rohre im Vordergrund. Es ruckelt leicht. Und ich brülle: „Wo ist der Extruder?“
Dann verstehe ich wieder. Hier wird aus den Silos Polypropylen angesaugt, erklärt Krumme. An dieser Stelle im ersten Stock kommen auch die Additive im Dosierer hinzu. Welche? Das wird nicht verraten. Sie sind ein entscheidendes Qualitäts- und Alleinstellungsmerkmal jedes Produzenten. Nur so viel: Additive machen das Vlies hydrophob, also wasserabweisend, antistatisch und sie mindern Gerüche. Über Rohre geht es dann zum Extruder, wo das Polymergemisch bei durchschnittlich 275 °C aufgeschmolzen wird.
Wie in der Spaghettipresse
Krumme nimmt mich auf dem Smartphone mit ins Erdgeschoss. Hier landet auch die Schmelze. Es ist einfach zu laut, Verständigung unmöglich. Über eine sogenannte Spinpumpe wird die Schmelze über die Breite der Anlage an feine Düsen verteilt. Sobald sie die Düsen verlässt, wird sie über einen Heißluftstrom mit 800 km/h nach unten verstreckt. „Sie können sich das wie bei einer Spaghettipresse vorstellen. Würden Sie dann mit einem Föhn von oben nach unten gehen und das mit 800 km/h, dann würden die Nudeln sehr dünn werden“, wird mir der Geschäftsführer später berichten.
Mit bloßem Auge ist es nicht zu erkennen. Alles geht einfach zu schnell. In Zeitlupe würde ich sehen, dass es im sogenannten Spinnraum Polymerfäden rieselt, Filamente, siebenmal dünner als ein menschliches Haar. Völlig wirr legen sich die Fäden auf einem Siebband ab. Eine weiße hauchdünne Fläche, die aussieht wie eine Folie, entsteht: das Meltblown-Vlies.
Das Verfahren zur Fertigung dieses besonderen Stoffes folgt einem einfachen Grundsatz der Filtration: Eine möglichst große Fläche soll auf einem möglichst kleinen Raum erzeugt werden. Hier werden Filamente versponnen, die so fein sind, dass sie aufgrund ihrer Anzahl und Menge auf dem engen Raum eine enorm große Oberfläche anbieten, auf der Bakterien und Viren anhaften können. „Das ist einer der feinsten Vliesstoffe, der im kommerziellen Prozess in großen Tonnagen hergestellt werden kann.“ Wie viele Anlagen in der Troisdorfer Halle stehen, auch das möchte Krumme nicht verraten.
Und, wo sind die Menschen im Prozess?
Wem zuliebe setzt Krumme eine Maske auf, als er durch die Produktion führt? Er dreht das Smartphone und zeigt uns, dass hier tatsächlich nicht nur Maschinen, sondern auch Menschen arbeiten. Sie stehen am Leitstand, überwachen die Prozessparameter, sie nehmen die Rollen ab. Wenn ein Wickel fertig ist, muss Platz gemacht werden für den nächsten. „Wir rechnen mit 1,5 Menschen pro Anlage.“
Ein paar Tage vor dem Smartphone-Rundgang: Der Sicherheitsabstand von 1,5 m zwischen Daniel Krumme und seinem Chef, dem Eigentümer Christian Klöber, ist kaum einzuhalten. Die Videokonferenz zeigt das deutlich. Aber, das geben beide lächelnd zu: „Wir sind ja auch gegenseitige Bezugspersonen.“ Die Vertrautheit ist spürbar – auch über mehr als 100 km Telefonleitung hinweg.
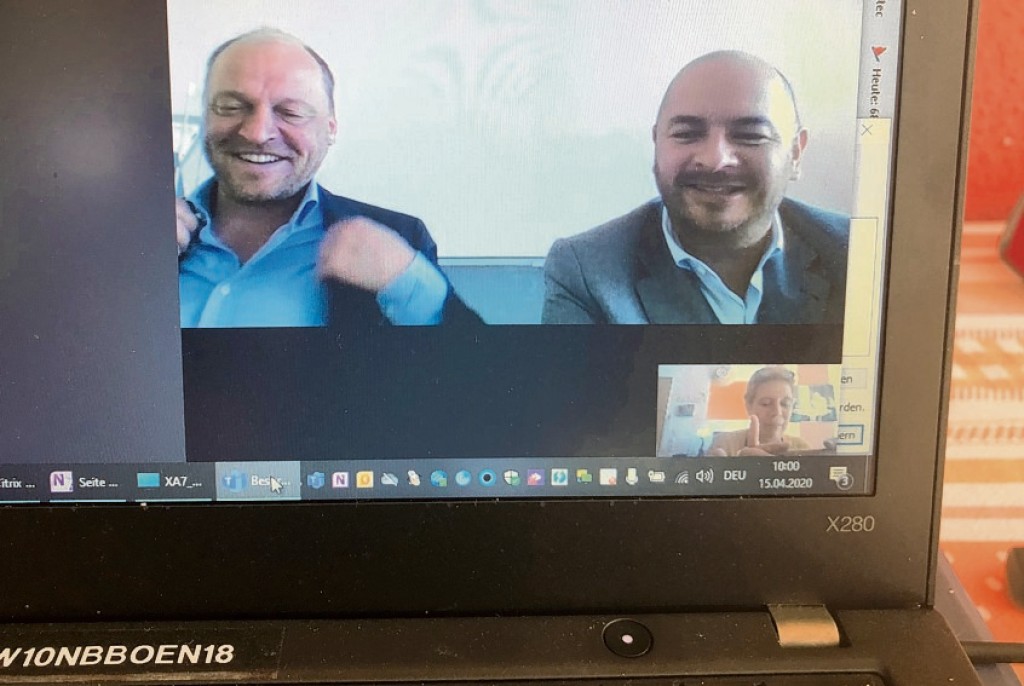
„Wir sind ein deutsches Familienunternehmen“, tut Klöber kund, mit lässig geöffnetem Hemdkragen. Diese beiden Herren krempeln lieber die Ärmel hoch, statt Schlips zu tragen. Innovatec hat rund 100 Mitarbeiter. Mit zur „Familie“ gehört das Schwesterunternehmen Granulat 2000, das ein paar Minuten entfernt von der Innovatec residiert. Es ist auf Granulate und Additive spezialisiert und natürlich ein wichtiger Zulieferer. „Kunststoff ist unser Zuhause“, so wirbt Klöber und strahlt übers ganze Gesicht.
Markt- und Technologieführer
Und dann wird er ernst: „Bezogen auf den Ausstoß von Meltblown-Vliesstoffen sind wir mit Abstand Markt- und Technologieführer – und das weltweit.“ Auch in China gebe es keinen, der als Einzelunternehmen mehr Anlagen in Betrieb habe. „Marktbegleiter“ – die Konkurrenz also – wie die fränkische Firma Sandler seien ursprünglich aus anderen Bereichen wie der Hygienebinden- oder Papierproduktion gekommen. Sicher, Meltblown ist eine Nische, aber die Innovatec hat sich voll auf dieses Segment spezialisiert.
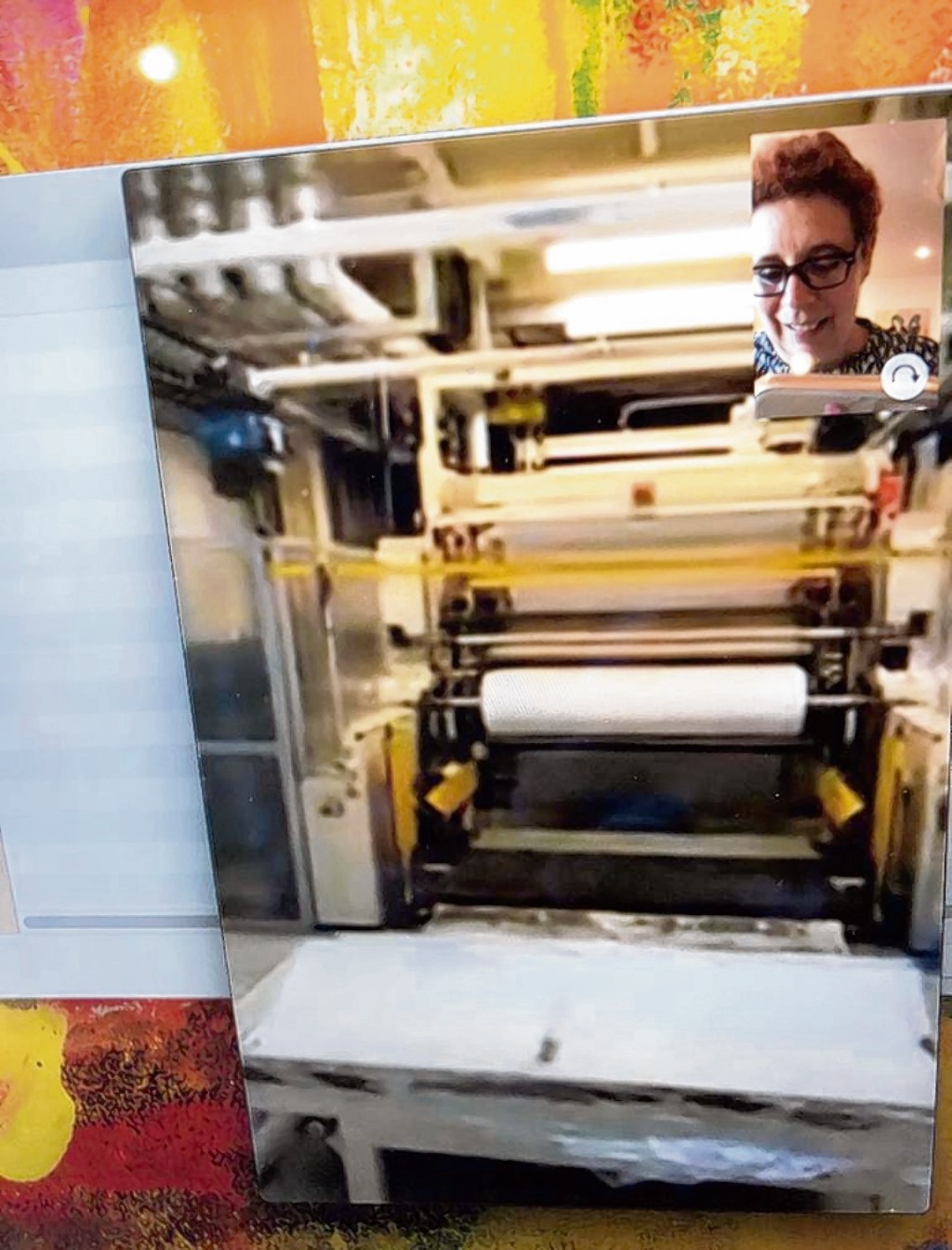
Schließlich wird der Stoff nicht nur für Masken eingesetzt, sondern auch für Unterspannbahnen im Bau, für Staubsaugerfilter, Blutfilter und Pflaster genutzt. Als die Ölplattform Deepwater Horizon in Brand geriet und sich ein riesiger Ölteppich im Golf von Mexiko bildete, waren es Meltblown-Vliese, die das Öl aufsaugten. Polypropylenvlies hat die Eigenschaft, Öl aufzunehmen und Wasser abzuweisen. „Wir können natürlich auch diesen Kunden nicht absagen, wir haben Verpflichtungen“, sagt Klöber.
Von Troisdorf in die Welt
Meltblown-Vlies für Masken geht von Troisdorf aus in die ganze Welt. Auch wenn eine medizinische Maske einfach aussieht, ihre Fertigung ist nicht trivial. Die Maschinen müssen voll automatisiert mit hohen Taktzahlen laufen. Die Kunst liegt im Verschweißen des Vlieses, aber auch in der späteren Weiterverarbeitung. Denn die Masken kommen in hoher Geschwindigkeit aus der Maschine und müssen ebenso schnell verpackt werden – und das unter Reinraumbedingungen.
Ein Job also für die deutsche Industrie? Sollte man meinen, aber noch liefern die Troisdorfer ihren begehrten Stoff vor allem an Maskenproduzenten aus Portugal, Frankreich sowie Italien und zu kleinen Teilen auch nach China.
Wirtschaftsministerium unterstützt
Medizinische Masken als Massenware werden hierzulande noch nicht produziert. Deutschland war in puncto Schutzkleidung nicht auf die Pandemie vorbereitet. Erst viel zu spät – mit dem Zusammenbruch globaler Lieferketten – wurde erkannt, wie wichtig es ist, Vlies, Masken und Schutzanzüge auch vom heimischen Markt zu beziehen.
Bundeswirtschaftsminister Peter Altmaier erklärte letztes Wochenende, dass er die Produktion von Atemschutzmasken in Deutschland massiv ankurbeln wolle. Vor Wochen hatte er die Förderung von Investitionen in die Meltblown-Vliesproduktion mit rund 40 Mio. € verkündet. Auch Innovatec profitiert davon, aber dazu später.
Jetzt sollen auch Anlagen zur Fertigung von sicheren Masken einen staatlichen Investitionszuschuss von bis zu 30 % erhalten. Ziel sei eine Produktion von jährlich bis zu 2,5 Mrd. Stück, sagt Altmaier. Abnahmegarantien bis 2023 inklusive. Vorausgesetzt, die Unternehmen verpflichten sich, mit der Produktion noch in diesem Jahr zu beginnen.
Bis zu 12 Mrd. Masken pro Jahr
„Wenn wir allen Menschen in Deutschland das Arbeiten, Einkaufen und Busfahren mit Mundschutz ermöglichen möchten, brauchen wir zwischen 8 Mrd. und 12 Mrd. Masken pro Jahr“, rechnete der Minister unlängst vor. Gut für das Geschäft der Innovatec? „Das sind so große Mengen, von denen wir in dem Maße gar nicht profitieren können. Das ist einfach nicht machbar“, gesteht Krumme ein. Selbst wenn es jede Menge Fördergelder und Platz gebe. Aber, wenn schon eine Grundversorgung der Krankenhäuser gesichert sei, wäre etwas gewonnen.
Wann also wird es hierzulande Produzenten von Masken in großen Stückzahlen geben? Diese Frage lässt sich am Telefon mit Diethelm Carius, Leiter der Medizintechnik im VDMA, klären. Er ist optimistisch. 13 Unternehmen stünden in den Startlöchern. So will beispielsweise der auf Medizintechnik spezialisierte Anlagenbauer Imstec aus der Nähe von Mainz demnächst FFP2-Masken herstellen. Der Papiermaschinenexperte Winkler + Dünnebier hat sich den OP-Masken verschrieben. Die ersten Pilotanlagen laufen in Deutschland und, so Carius: „Es gibt klare Signale, dass es bald losgehen soll.“ Bald, das dürfte wohl Juni heißen.
Krumme rückt derweil seine Maske zurecht und bestätigt: „Wir haben Zuschriften von Unternehmen, die vom Bund den Zuschlag erhalten haben. Sie montieren jetzt ihre Maschinen und könnten im Juni startbereit sein.“ Das wäre flott und ginge dann gleich in die Millionenstückzahlen. Gängige Maskenautomaten, die auch in Deutschland gebaut werden, schaffen es auf gut 100 Stück pro Minute. In drei Schichten wären das dann mehrere Zehntausend am Tag.
Maskenstoff für Deutschland
Krumme, sein Smartphone und damit ich sind derweil wieder auf dem Firmenhof gelandet. Und wieder gehts ein Stück über das Gelände. Die Troisdorfer haben Glück. Im Herbst letzten Jahres – lange vor der Corona-Krise – haben sie eine weitere Anlage bestellt, auf der sie schon im Juni Meltblown-Vlies produzieren wollen. Maskenstoff speziell für Deutschland.
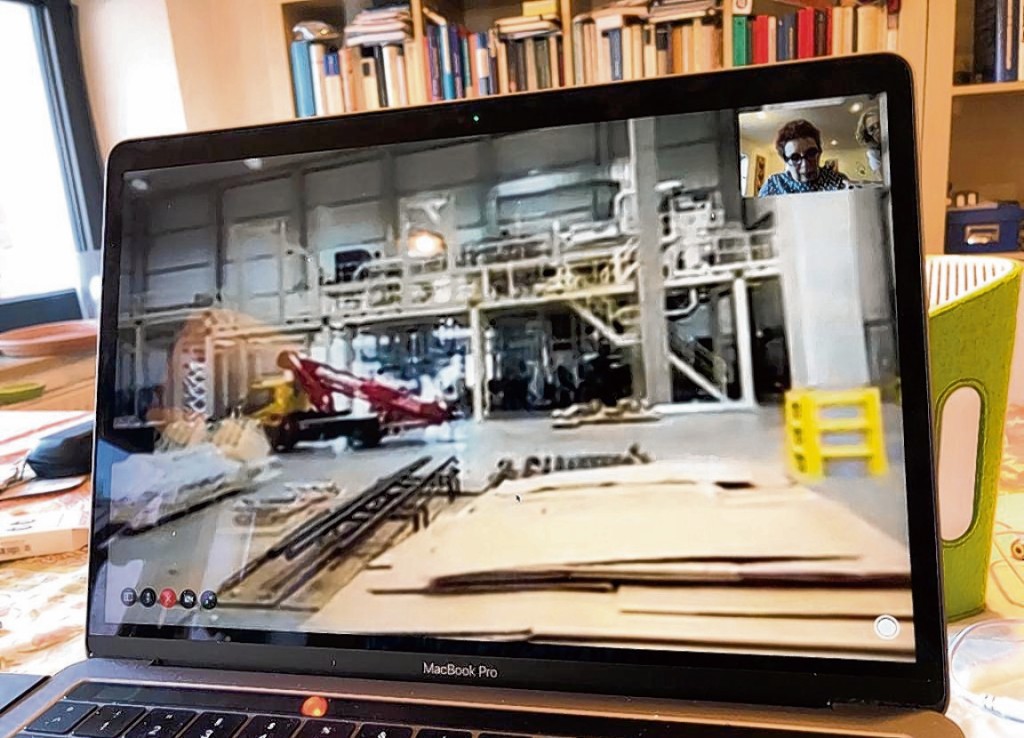
„Das ist alles noch nicht fertig“, erklärt der Geschäftsführer und deutet auf eine neue Halle. Transporter von Handwerkern in allen Farben parken hier. Die Morgensonne blendet und macht Großes ganz klein. So wie die silbernen Silos, die auf der anderen Straßenseite stehen. 30 m hoch, gefüllt mit 50 t Polypropylen. Täglich rollen „Silozüge“ mit neuem Granulat an. Auch die Stromversorgung liegt schon. Krumme filmt einen grauen Kasten. „Meltblown ist ein sehr stromintensiver Prozess.“
Wir treten via Bildschirm gemeinsam in die neue Halle ein. Hier erst werden die Dimensionen sichtbar. Menschen verschwinden, die Autos der Monteure und selbst der große Hebebühnenwagen werden zu Spielzeugfahrzeugen. Der Schwerlaststapler hat gerade einen großen Lüftungskanal auf der Gabel. Noch füllen Montagecontainer der Aufbautrupps und Rohre die Halle. Je nach Bedarf wird auch ein Schwerlastkran in die Halle gefahren, der dann bis zu 10 t schwere Teile auf die Bühnen heben kann.
Maschinen aus Deutschland
Die Maschinenbauer für diese Riesen der Vliesproduktion sitzen in Deutschland. Sie kommen aus Troisdorf – wie die nur ein paar Straßenzüge entfernte Firma Reifenhäuser – und aus Norddeutschland, wo Oerlikon, eine Schweizer Firma, produziert. Von dort stammen auch die zwei neuen Anlagen, die Innovatec jetzt im Zuge der Krise bestellt hat. Sie dürften im Herbst fertig montiert und mit firmeneigenem Know-how gerüstet sein. Mit ihnen profitiert auch der Kunststoffspezialist von der Förderung Altmaiers.
Eine neue Anlage wird im Schnitt 1000 t Meltblown-Vlies im Jahr nur für Mundschutz produzieren. Das reicht allerdings nicht für den deutschen Markt und schon gar nicht für den europäischen. Fest steht, der Bedarf an Masken und damit an Meltblown-Vlies wird weiter steigen. Corona, das Virus, wird uns noch eine Weile beschäftigen – darin sind sich Wissenschaft, Industrie und Politik einig.
Wieder draußen, schwenkt Krumme sein Smartphone zu schnell. Alles wird unscharf. Der leichte Frühlingswind knallt jetzt ins Mikrofon, als er mir zuwinkt. „Auf Wiedersehen, gerne auch mal im realen Leben. Und bleiben Sie gesund!“