E-Mobilität: Fahren am physikalischen Limit
Vier Sachsen erreichen mit gedruckten Motorspulen beeindruckende Leistungsdaten. Entwicklern klassischer E-Antriebe versprechen sie einen beschleunigten Prototypenbau.
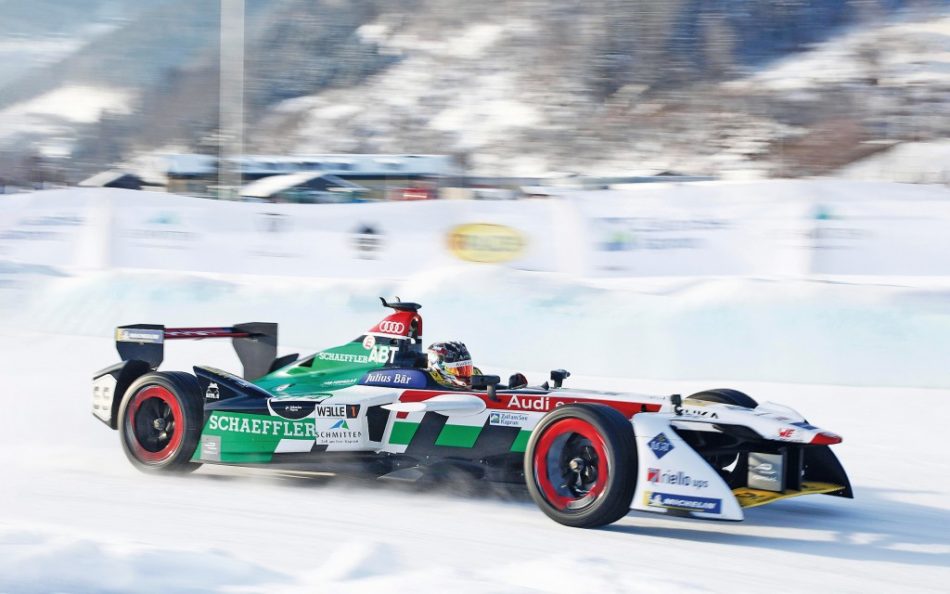
Foto: ddp images/imageBROKER/Jörn Friederich
An der Spitze der Evolution von E-Motoren stehen die Aggregate in Formel-E-Boliden. Ihre Leistungsdaten werden seit Jahren von findigen Ingenieuren nach oben geschraubt. Ausgerechnet hier will die Additive Drives GmbH aus Halsbrücke mithalten. Dabei sind die Sachsen erst vergangene Woche an den Start gegangen. Geschäftsführer Jakob Jung gibt sich trotzdem optimistisch.
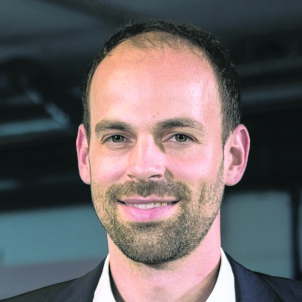
Gleichzeitig will der bescheidene Gründer niemanden brüskieren. Er vermeidet jeden direkten Vergleich mit den Profiteams aus dem Rennzirkus. „Die arbeiten ja auch viel im Geheimen“, sagt er leise – gerade so, als müsse er die Wettbewerber in Schutz nehmen. Aber eine markante Aussage wagt der promovierte Mechatroniker dann doch: „Besser als wir sind die garantiert nicht. Denn wir holen das physikalische Optimum aus dem Motor heraus.“
Kupferfüllfaktor im Stator erhöht
Möglich macht das die additive Fertigung. „Sie erlaubt es uns, den Kupferfüllfaktor im Stator maßgeblich zu erhöhen.“ Bei orthozyklischen Runddrahtwicklungen (s. Grafik unten) seien Werte von 40 % bis 45 % der Standard. „Wir erreichen spielend 65 %.“ Vorteil: Da sich der elektrische Widerstand proportional zu 1/Kupferfüllfaktor verhält, können die Stromwärmeverluste mit der gedruckten Spule um über 30 % reduziert werden – bei gleichem Drehmoment.
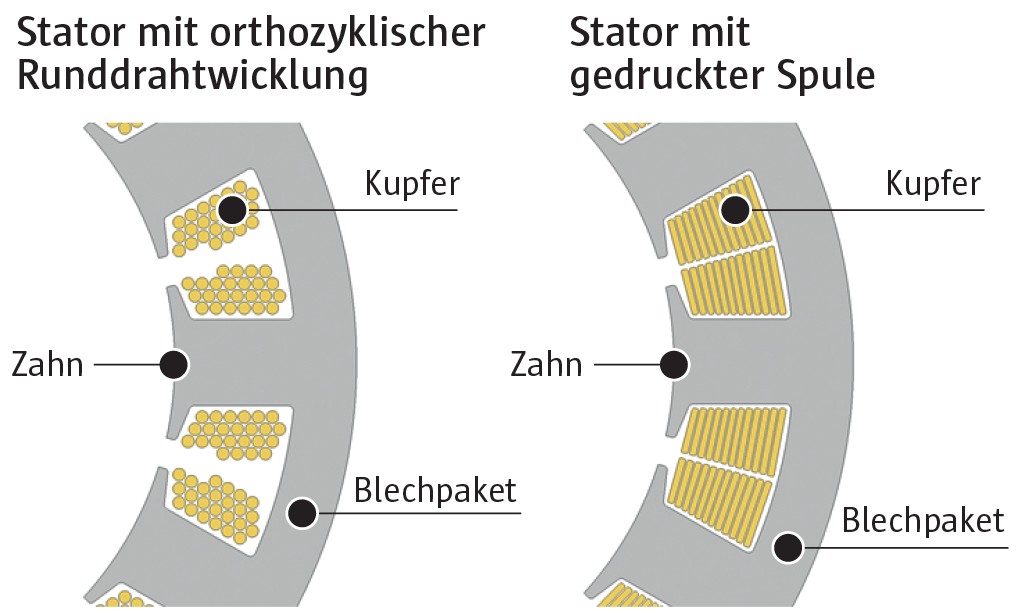
Ein weiterer Vorteil der innovativen Spulengeometrie: Jeder einzelne Leiter liegt direkt am Blechpaket an. Dadurch werden Hotspots, wie sie in Außenbereichen konventioneller Wicklungen auftreten, vermieden. „Das erlaubt höhere Stromdichten, also ein höheres Drehmoment“, so Jung. „Und dazu müssen Gehäuse und Kühlung nicht mal umgestaltet werden.“
Deutlich mehr Drehmoment
Mithilfe der gedruckten Spule kann obendrein dem sogenannten Proximityeffekt begegnet werden. Er beschreibt das Phänomen, dass der Strom bei Frequenzen jenseits der 500 Hz – also im oberen Drehzahlbereich – nicht mehr gleichmäßig über den Leiter verteilt fließt. Stattdessen wird er in Richtung Nutöffnung und an die Leiteraußenseiten gedrängt. „Hier können wir entgegenwirken, indem wir die Leiterquerschnitte in Richtung Nutöffnung flacher gestalten. Dadurch wird der Strom sozusagen auf den Querschnitt gezwängt.“
In Summe ergeben die einzelnen Vorteile ein um rund 45 % erhöhtes Drehmoment. Sollten Leistungslimits vorgegeben sein, wie im Motorsport, kann dieser Vorteil genutzt werden, um den Motor kompakter zu gestalten. „Denn das Drehmoment eines E-Motors ist proportional zu seinem Volumen“, erläutert Jung.
Motor kompakter und leichter gestalten
Die Gestaltungsfreiheit des 3-D-Drucks kann auch für die Wickelköpfe ausgenutzt werden. Das sind die Teile der Spule, die aus den Stirnseiten des Blechpakets herausragen. Sie erzeugen keinerlei Drehmoment. „Wir können sie also ebenfalls verkleinern und so den Motor noch mal kompakter und leichter gestalten“, erklärt Jung. „Ein Problem mit zu engen Biegeradien haben wir dabei nicht“, so der 36-Jährige. „Denn bei uns wird nichts gebogen.“
Gedruckt werden die Spulen auf einer modifizierten Laserschmelzanlage eines etablierten Herstellers. Die Belichtungsstrategie sieht dabei einen Abstand von etwa 100 µm zwischen einzelnen Windungen vor. Dieser Wert bemisst sich an der späteren Isolierschichtdicke, welche wiederum abhängig ist von der Versorgungsspannung.
Nach dem Drucken wird die Spule zunächst im Rahmen eines elektrolytischen Prozesses gereinigt. „Sie wird dadurch spiegelglatt“, so Jung. „So werden Teilentladungen bei hohen Spannungen eingedämmt.“
Isoliert wird das Kupferbauteil abschließend mithilfe einer Vakuumform. „Die Luft wird abgesaugt und durch Elektroisolierharz ersetzt“, erklärt Jung. „Lufteinschlüsse werden dadurch vermieden und die thermische Anbindung optimiert.“
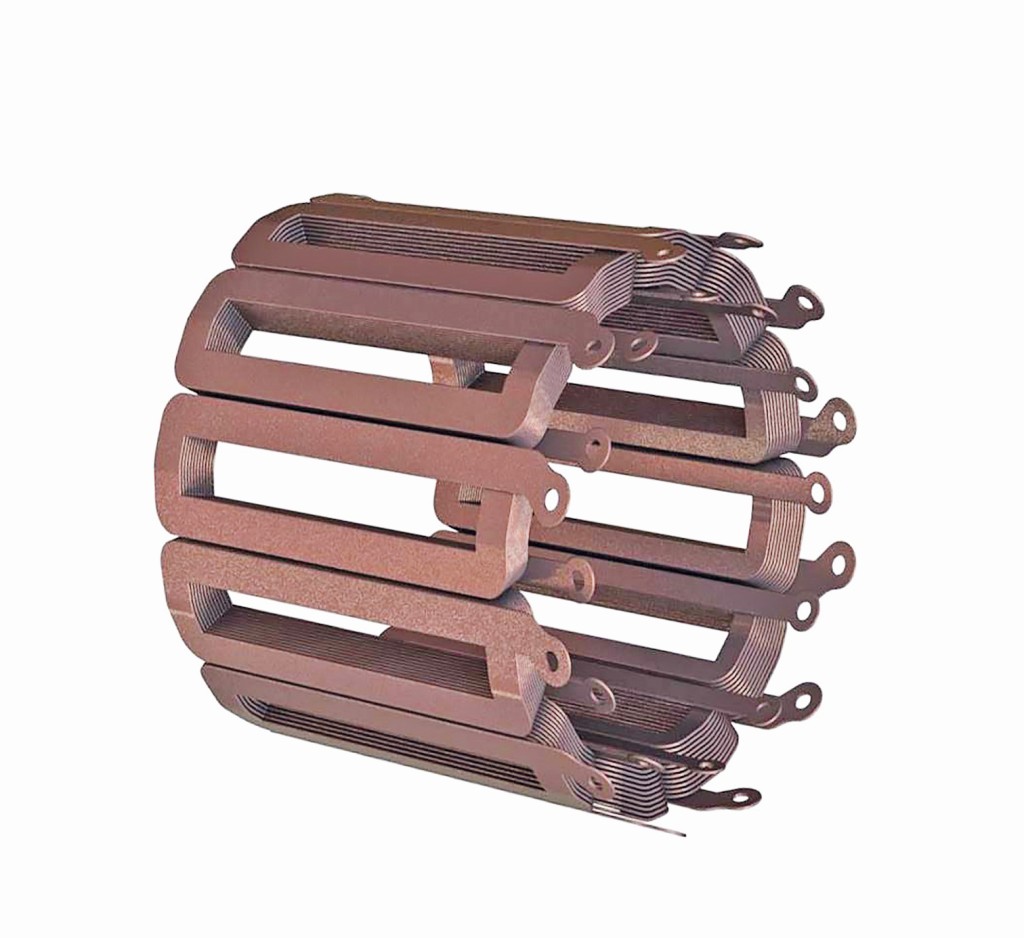
Fertige Spulen können dank einer Statorsegmentierung ganz einfach auf die Zähne des Blechpakets aufgeschoben werden. Derzeit werden benachbarte Spulen noch miteinander verschraubt (s. Grafik). „Wir arbeiten aber an formschlüssigen Lösungen“, so Jung. „Die Enden werden dann nach einem Stecker/Buchse-Prinzip miteinander verbunden.“
Potenzial über den Rennsport hinaus
Zur Zielgruppe von Additive Drives zählen Hersteller und Entwickler hochkompakter E-Motoren. „Das geht weit über den Rennsport hinaus“, so Jung. „Wir sehen großes Potenzial auch bei More-Electric-Aircraft-Anwendungen und im E-Bike-Bereich.“ Die jeweiligen Produkte müssten noch nicht mal teurer sein als klassische Lösungen. „Das ist eine Frage der Losgröße. Bei kleinen Stückzahlen spart man sich das Wickelwerkzeug. Außerdem können wir einen Extra-Benefit beim Kunden generieren – etwa durch mehr Leistung.“ Der Ingenieur ist überzeugt: „Bei E-Bikes wären wir im dreistelligen Stückzahlbereich sogar billiger.“
Ein weiteres Geschäftsfeld sieht Jung im Prototypenbau von klassischen E-Motoren. Hier zielt sein Unternehmen vor allem ab auf Hairpin-Lösungen. Entsprechende Wicklungen haben sich bei E-Traktionsmotoren auf breiter Front durchgesetzt. „Aus eigener Erfahrung weiß ich, dass die Entwicklung eines solchen Motors langwierig ist. Auf die Erstrealisierung von Mustern wartet man sechs Monate und mehr.“ Ursache dafür seien neben der Drahtbeschaffung komplexe Biege- und Schweißwerkzeuge, die es einzurichten gelte. „Mit diesen Werkzeugen kann man daraufhin eine Serie darstellen, jedoch zahlt man den Preis der langen Wartezeiten und der Inflexibilität in der Entwicklungsphase. Wir schließen die Lücke und gestatten es Entwicklern, zeitnah ihr Motordesign anhand echter Hardware zu testen.“