Maschinenbauer treiben Energieeffizienz voran
Das Thema Energieeffizienz hat für die Firmen des deutschen Maschinen- und Anlagenbaus eine doppelte Bedeutung. Kunden fordern, dass die Produkte im Gebrauch immer weniger Energie benötigen. Durch die steigenden Energiekosten wird die Energieeffizienz auch bei den Herstellern zu einem strategischen Faktor, der über deren Wettbewerbsfähigkeit entscheidet.
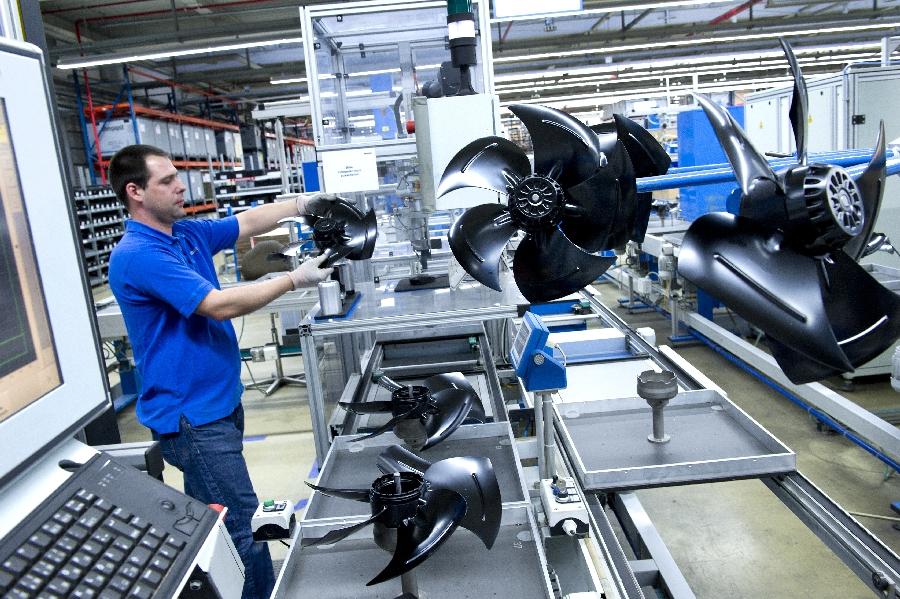
Foto: EBM-Papst
Der Maschinenbau versteht sich als Vorreiter bei der Realisierung energiesparender Lösungen. Verglichen mit dem Verbrauch im Jahr 2000 erzielen nach Aussagen des Branchenverbandes VDMA Produkte des Maschinen- und Anlagenbaus bereits heute Energieeinsparungen, die dem Strombedarf aller 48 Millionen Haushalte in Deutschland, Österreich und der Schweiz entsprechen. Darüber hinaus sieht die Branche gute Chancen, mit ihrer Blue-Competence-Initiative in den nächsten zehn Jahren noch einmal so viel Energie einzusparen.
Um dieses Ziel zu erreichen, kommt es darauf an, die eigenen Mitarbeiter möglichst früh auf die Bedeutung des Energiesparens aufmerksam zu machen. Wie das gelingen kann, zeigt die Initiative des Ventilatoren- und Motorenherstellers EBM-Papst an seinem Stammsitz im württembergischen Mulfingen: Seit vier Jahren spüren dort Auszubildende – sogenannte Energiescouts – Druckluftverluste und andere ineffiziente Stellen im Produktionsprozess auf und beseitigen diese fachkundig. Die jungen Leute sind ein Jahr lang dafür zuständig, dass in der Produktion möglichst keine Druckluft verloren geht und kein Motor zu heiß läuft und Wärme verliert. Danach übernimmt ein neues Team ihre Aufgabe.
Die Aufgabe motiviert die jungen Menschen nicht nur für den Umwelt- und Ressourcenschutz, sondern spart EBM-Papst jede Menge Energie und damit Kosten. Im Gegensatz zu anderen Unternehmen wird also keine Spezialfirma damit beauftragt, die Lecks zu finden. Ein weiterer Vorteil: Die Energie-
scouts wirken als Multiplikatoren. Sie geben ihr Wissen und ihre Erfahrung auch an Kollegen an anderen Standorten der Unternehmensgruppe weiter – spätestens, wenn sie nach der Ausbildung den Standort wechseln.
Dass man durch Einsatz von innovativer Technik Produkte nicht nur energieeffizienter, sondern gleichzeitig auch bei deren Herstellung Energie einsparen kann, zeigt der Hersteller von Industrieöfen Linn aus Eschenfelden in der Oberpfalz. Mit dem Einsatz von Mikrowellentechnik bei der Herstellung von hochisolierenden Hightech-Isolierpaneelen ist es dem mittelständischen Unternehmen gelungen, die Isolationswirkung der Paneele weiter zu verbessern und gleichzeitig sowohl die Zeit für den Herstellungsprozess als auch den Energieaufwand zu minimieren.
Die Isolationswirkung von solchen Vakuum-Isolierpaneelen, die unter anderem bei energieeffizienten Elektrogeräten oder aber auch bei Passiv-Energiehäusern verwendet werden, hängt maßgeblich vom Feuchtigkeitsgehalt des Paneelkernes ab. Um eine optimale Isolationswirkung zu erreichen, müssen Feuchtigkeitswerte mit weniger als 0,1 % erreicht werden. Mit herkömmlicher Trocknertechnik waren derart niedrige Feuchtigkeitswerte nur durch lange Behandlungszeiten realisierbar, da die Isolierplatten aufgrund ihrer niedrigen Wärmeleitfähigkeit nur sehr schwer und unter hohem Energieaufwand erwärmt werden können.
Mit der Entwicklung des neuen Verfahrens ermöglicht Linn seinen Kunden eine effizientere, schnellere Produktion und verringert gleichzeitig die Kosten bei der Herstellung der Vakuum-Isolierpaneele. Der Vorteil der Mikrowellentechnik liegt im Vergleich zu anderen Erwärmungsmethoden darin, dass die Mikrowellen in die Produkte eindringen und die Wärme quasi im Inneren des Bauteils erzeugen. Auf diese Weise lassen sich in Minutenschnelle selbst diese sehr geringen Feuchtigkeitswerte erzielen.
Auch die Werkzeugbauer, die in Baden-Württemberg stark vertreten sind, bemühen sich seit Jahren intensiv um eine höhere Energieeffizienz bei ihren Anlagen. Die meisten Werkzeugmaschinen arbeiten energieintensiv: Eine durchschnittliche Dreh-, Fräs- oder Schleifmaschine stößt jährlich indirekt so viel CO2 aus wie zehn Pkw. Energie und Medien verursachen bis zu 40 % der Betriebskosten einer Maschine. Besonders hoch ist der Energiebedarf der Hauptspindel, dem Herzstück einer jeden Werkzeugmaschine. Diese verbraucht nicht nur viel Strom, sondern benötigt für ihren Betrieb zusätzlich Druckluft und Kühlleistung.
Um ihren Kunden die Investition in energieeffiziente Technik schmackhaft zu machen, suchen viele Hersteller nach Lösungen, die neben dem Energiesparen einen zusätzlichen Nutzen bieten. Die Firma Grob aus Mindelheim im Allgäu, hat daher von vornherein eine komplett hydraulikfreie Maschine entwickelt. Diese sei aufgrund von hochdynamischen Servomotoren mit Hochgenauigkeitsgetrieben, welche die Werkstückspannung sowie das Lösen der Werkzeuge in der Spindel übernehmen, nicht nur energieeffizient, sondern biete gleichzeitig eine höhere Flexibilität und höhere Verfügbarkeit.
„Das Lösen der Werkzeuge geschieht zudem deutlich leiser, verhindert harte Schläge, die bei jedem Werkzeugwechsel auch das Spindellagersystem treffen und reduziert noch einmal die Nebenzeiten“, erläutert Alfred Höbel, Bereichsleiter der Grob-Entwicklung, einen weiteren entscheidenden Vorteil, der mit der konsequenten Weiterentwicklung verbunden ist.
Hersteller wie MAG in Eislingen oder Heller in Nürtingen greifen nicht ganz so stark in die Maschine ein. Sie schnüren für ihre Kunden Energieeffizienzpakete, die diese nach Bedarf kombinieren und mit denen sie den Energieverbrauch gegenüber vergleichbaren CNC-Maschinen um bis zu 30 % reduzieren können.
So erlaubt beispielsweise das Paket „Blue smartsupply“ das Abschalten aller Verbraucher beziehungsweise den Schlafmodus für Funktionseinheiten wie Kühler, Pumpen, Beleuchtungen, Späneförderer, Antriebe oder die Sperrluft. Oder bei dem Paket „coolant“ passt sich durch einen zusätzlichen Frequenzumrichter der Volumenstrom der Hochdruck-Kühlmittelpumpe und damit auch der Energieverbrauch an die Anforderungen ihrer Bearbeitungsaufgabe an.
„Unsere Automotive-Kunden schreiben Energieeffizienz seit einiger Zeit sogar in die Lastenhefte“, berichtet Heller-Geschäftsführer Lang. Dabei werden Bauteile und Baugruppen von Werkzeugmaschinen wie zum Beispiel Motoren und Pumpen über die Bauteilfreigabe vorgeschrieben. Auch softwareseitige Anforderungen würden gestellt und maximale Drücke für die pneumatischen Systeme vorgegeben, sagt der Heller-Geschäftsführer. Mit den Energieeffizienzpaketen könnten die Anwender ganz individuell entscheiden, welche Lösungen für sie in Frage kommen und wie viel Geld sie ausgeben wollen, so Lang.