Neues Verfahren soll Recyclinganteil von Autoreifen steigern
Lediglich 5 % alter Autoreifen landen bisher in der Produktion neuer Reifen. Ein neues Verfahren zur Devulkanisierung soll das ändern.
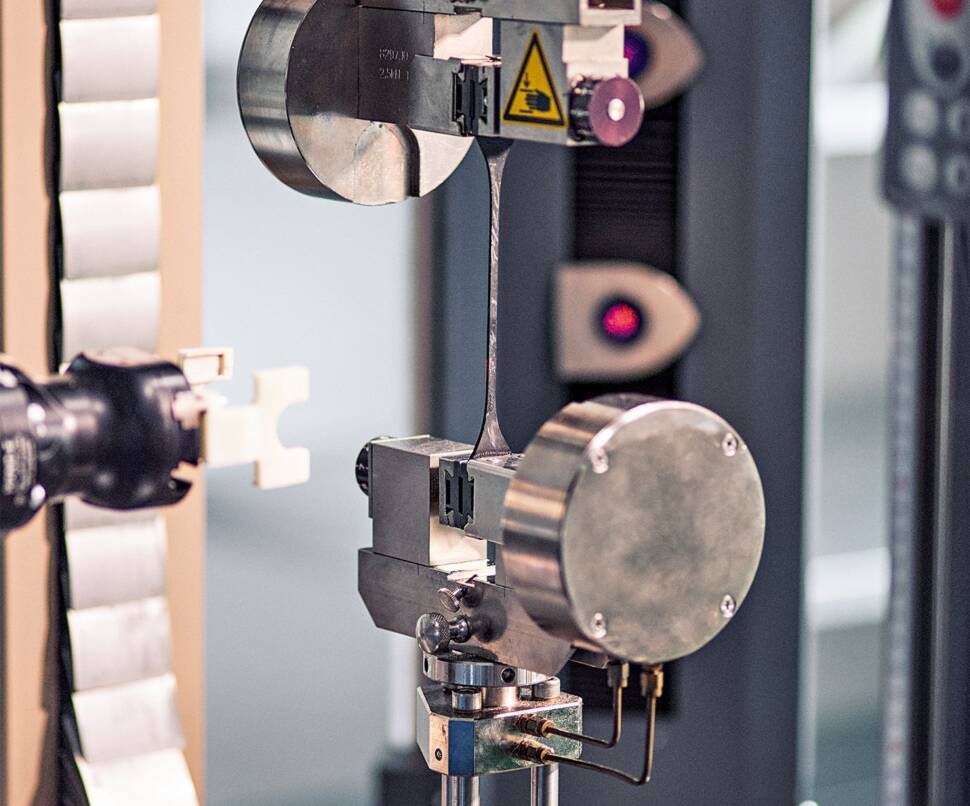
Foto: Evonik Industries AG
Inhaltsverzeichnis
Ein höherer Anteil an recyceltem Material kann auch in der Reifenproduktion zu Schonung von Ressourcen beitragen. Bisher war dieser Anteil allerdings verfahrensbedingt eher gering. Nur etwa 5 % an gemahlenem Altmaterial geben Fachverbände der Reifen-Recyclingbranche bisher als Obergrenze für die Beimischung an. Im Verhältnis zu vielen Kunststoffen ist das wenig. Laut der Gesellschaft für Verpackungsmarktforschung erhalten z. B. PET-Einwegflaschen für Getränke im bundesweiten Durchschnitt 45 % Recyclingmaterial.
Die Herstellung von Autoreifen erschwert bisher höhere Recyclinganteile. Denn dabei werden Kautschuk, Schwefel und andere Bestandteile durch Vulkanisation vernetzt. Unter Hitze und Druck bildet Schwefel dabei Bindungen mit langen Kohlenstoffketten des Kautschuks. Es entsteht ein robustes, dreidimensionales Netz, das dem Reifen seine Stabilität verleiht.
Gemahlenes Altgummi ist durch Vulkanisierung bereits vernetzt
Das Problem bisher: Als bereits vulkanisiertes Material besitzt gemahlenes Altgummi andere Eigenschaften als nicht vulkanisierter Kautschuk. Seine chemische Struktur erschwert deshalb das Zusammenwirken mit dem neuen Reifenmaterial im Produktionsprozess. Ein Großteil des Altgummis geht deshalb in die Herstellung von Schutzelementen auf Spielplätzen oder landet auf Laufbahnen von Sportplätzen. Viele Altreifen enden weiterhin in der thermischen Verwertung und dienen als Brennstoff. Christian Mani, Projektmanager Circularity bei Evonik, ist jedoch überzeugt: „Gummi ist ein zu wertvoller Rohstoff, um ihn nur einmal im Reifen zu nutzen. Wir wollen ihn in einen Kreislauf einbinden.“
Ein Forscherteam des Unternehmens hat dazu ein Verfahren weiterentwickelt, bei dem die Schwefelbrücken im Altmaterial zunächst aufgebrochen werden. Es erfolgt also eine Devulkanisierung. Bis zu viermal so viel Altmaterial wie bisher soll damit in neue Reifen eingebracht werden können. „Damit rücken die wichtigen Ziele Nachhaltigkeit und Ressourcenschonung auch für die Branche ein ganzes Stück näher“, sagt Christian Mani, Projektmanager Circularity bei Evonik.
Evonik macht die Vulkanisation alter Gummireifen rückgängig
Ihm und seinem Team ist es nach Unternehmensangaben gelungen, die Vulkanisation in Gummimaterial zu großen Teilen rückgängig zu machen. „Durch Zugabe einer speziellen Formulierung mit Vinylsilanen lässt sich die feste Vernetzung im Recyclingmaterial wieder auftrennen. Wir lösen die Schwefelbrücken im Gummi, lassen dabei aber gleichzeitig möglichst viele der langen Kohlenstoffketten unangetastet“, erläutert der Experte dazu.
Bei den bisherigen Versuchen mit Vinylsilanen zur Devulkanisation ließ sich der Anteil des Recyclingmaterials in der Gummimischung laut dem Entwicklungsteam auf bis zu 20 % erhöhen. Damit wird die bisherige technische Schwelle von 5 % deutlich übertroffen.
Verfahren soll bald in großem Maßstab für die Produktion von Reifen funktionieren
In weiteren Testreihen und Erprobungen will Evonik eine Lösung entwickeln, die Reifenhersteller in absehbarer Zeit in der industriellen Produktion einsetzen können. „Am Ende muss unser Ansatz auch in großem kommerziellem Maßstab überzeugen“, sagt Mani.
Das Nachhaltigkeitspotenzial einer solchen Kreislauflösung ist nach Berechnungen von Evonik enorm: Weltweit gibt es mehr als 1,3 Mrd. Personenwagen. Dafür werden Minute für Minute mehr als 2000 neue Pkw-Reifen produziert. Das gilt unabhängig von der Antriebsart. Denn auch Autos mit Elektro- oder Wasserstoffantrieb rollen auf Gummireifen. Wie groß das Potenzial ist, lässt auch der Jahresumsatz der Hersteller erahnen. Mit Pkw-Reifen werden weltweit mehr als 100 Mrd. € umgesetzt.