Werkzeugbau des Jahres 2023 baut die Umformwerkzeuge für Fahrzeuge von BMW
Trotz großer Herausforderungen für den Werkzeug- und Formenbau im deutschsprachigen Raum gab es diese Woche Grund zum Feiern. Die Branche kürte in Aachen ihre besten Unternehmen.

Foto: BMW Group
Wie schwierig das Jahr 2023 für die Werkzeugbaubetriebe im deutschsprachigen Raum war, konnten die Organisatoren des Wettbewerbs „Excellence in Production“ miterleben. Gemeinsam ermittelten das Werkzeugmaschinenlabor WZL der RWTH Aachen und das Fraunhofer-Institut für Produktionstechnologie IPT seit Anfang 2023 mit einer fachkundigen Jury die besten Werkzeug- und Formenbaubetriebe im deutschsprachigen Raum. Zum bereits 20. Mal hatten sie Unternehmen der Branche befragt und die Filialisten sogar vor Ort besucht, um den Werkzeugbau des Jahres zu küren.
Hier gibt es eine Bildgalerie mit Hintergrundinfos zu allen nominierten Unternehmen
Die starke Konkurrenz aus dem asiatischen Raum und ein enormer Preisdruck bei gleichzeitig hohen Kundenanforderungen haben laut den Veranstaltern allen Betrieben zu schaffen gemacht, vor allem jedoch den externen Werkzeugbaubetrieben. Umso herausragender sei die Leistung der Unternehmen, die dieses Jahr im Finale standen. Die internen Werkzeugbaubetriebe zeigten im Teilnehmerfeld der Finalisten gleichermaßen starke Leistungen und stellten schließlich auch den Gesamtsieger.
Gesamtsieger sind die Umformer von BMW in München und Dingolfing
Aus einem Teilnehmerfeld von insgesamt 305 Unternehmen setzte sich der gemeinsame Münchner und Dingolfinger Werkzeugbau von BMW als Gesamtsieger durch. Im Jahr zuvor hatte sich das Team im Finale noch knapp geschlagen geben müssen. In vier Kategorien – jeweils unterschieden nach internem und externem Werkzeugbau sowie der Unternehmensgröße unter bzw. ab 50 Beschäftigten – waren zwölf Finalisten angetreten. Vorgestern konnte das Team der BMW-Umformer sich bei der Preisverleihung im Aachener Rathaus von rund 300 Gästen für den Erfolg feiern lassen. Ausschlaggebend waren für die Jury insbesondere die starke strategische Positionierung des Werkzeugbaus als Wegbereiter für das Fahrzeugdesign innerhalb des Konzerns und der stringente Einsatz von Industrie-4.0-Technologie und Digitalisierung. Als herausragendes Beispiel dafür hob die Jury die konsequente Nutzung von Augmented Reality in der Qualitätsprüfung und zur Digitalisierung des Fachwissens der Mitarbeitenden hervor.
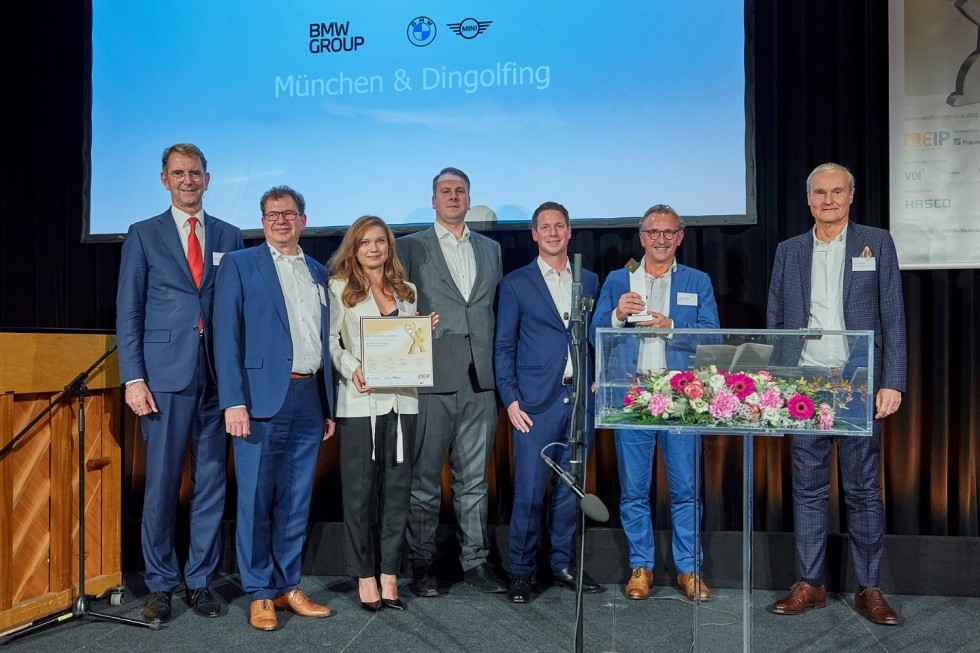
Der Umformwerkzeugbau ist Teil des weiten Produktionsnetzwerks der BMW Group und beschäftigt 480 Mitarbeitende, dazu zählen auch 68 Auszubildende. Der Münchner und Dingolfinger BMW-Werkzeugbau legt dabei einen starken technologischen Fokus auf seine Kernkompetenz des Fräsens und verfügt in dieser Technologie über einen hohen Automatisierungsgrad. Mit seiner technologischen Ausstattung und dem dazugehörigen Know-how ist der Werkzeugbau außerordentlich gut in die vor- und nachgelagerten internen Kundenprozesse integriert und stellt darüber hinaus ein breites Dienstleistungsangebot bereit, zu dem auch datenbasierte Dienstleistungen zählen, beispielsweise die Sensorüberwachung des Werkzeugs am Einsatzort.
Der Unternehmensbereich des Automobilbauers hatte sich zuvor auch in seiner Kategorie „Interner Werkzeugbau ab 50 Mitarbeitende“ durchgesetzt.
Sieger in der Kategorie „interner Werkzeugbau bis 50 Mitarbeitende“ überzeugte mit hoher Prozesskompetenz
Bei den Betrieben mit weniger als 50 Beschäftigten durfte sich die Technoform Insulation Solutions Tooling GmbH aus Kassel freuen. Als deutsches Familienunternehmen ist Technoform international tätig und spezialisiert auf die Extrusion thermoplastischer Kunststoffprofile für thermische Trennungen in Fensterprofilen und Isolierprofilen. Das Team des Werkzeugbaus besteht aktuell aus 47 Mitarbeitenden, sechs davon sind Auszubildende. Insgesamt beschäftigt Techform an mehr als 45 Vertriebs- und Produktionsstandorten weltweit rund 1600 Mitarbeiterinnen und Mitarbeiter.
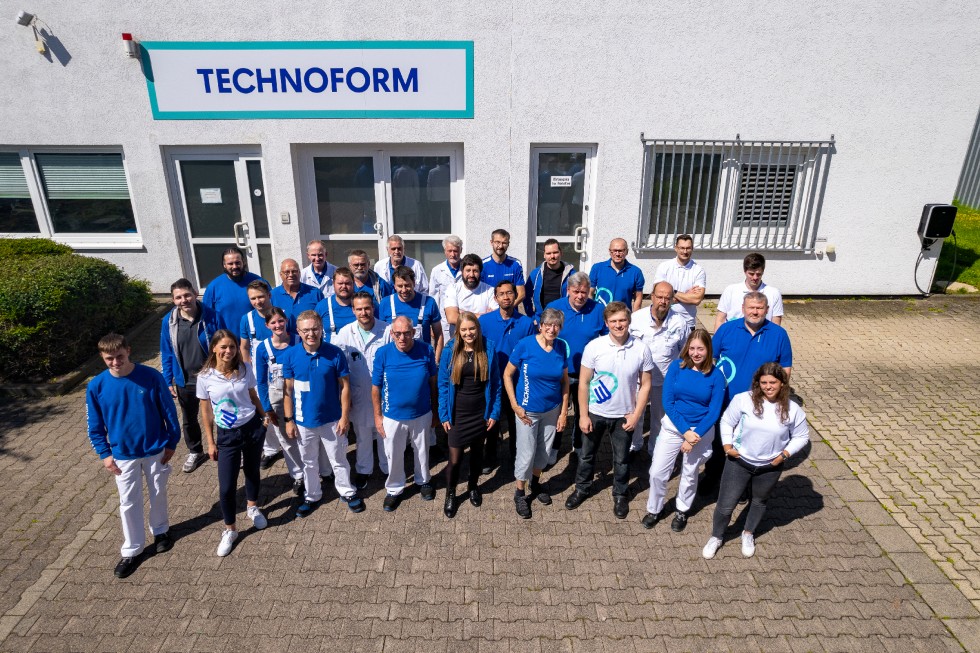
Der interne Werkzeugbau fertigt jährlich mehrere Hundert Muster- und Serienwerkzeuge für den Eigenbedarf. Die Jury hob bei Technoform besonders die hohe Prozesskompetenz in der Drahterosion hervor. Das Unternehmen nutzt dafür eine 4-Achs-Bearbeitung sowie selbst hergestellte Aufspannungen zur Reduktion von Rüstaufwänden. Zwei redundante Hallen für Serien und Musterwerkzeuge bilden laut dem Urteil der Jury eine schlüssige Segmentierung des Werkzeugbaus. Einen ausgezeichneten Eindruck hinterließ bei der Jury auch die starke Mitarbeitendenorientierung in Form flacher Hierarchien, hoher Eigenverantwortung der Mitarbeitenden und flexibler Arbeitszeitgestaltung.
Sieger im „externen Werkzeugbau ab 50 Mitarbeitende“ beeindruckte durch seine organisatorische Exzellenz
Bei den größeren Unternehmen mit externen Kunden konnte sich die 1956 gegründete Giebeler GmbH aus Eschenburg bei Gießen durchsetzen. Das Familienunternehmen beschäftigt insgesamt 180 Mitarbeitende in den Bereichen Werkzeugbau und Kunststofftechnik. Etwa 11 000 Werkzeuge wurden dort über die Jahre hergestellt. Neueste Technologien, digitale Prozesse und die strategisch nachhaltige Ausrichtung des Werkzeugbaus bestimmen die Entwicklung kundenindividueller Lösungen vom Design bis zur Herstellung von Werkzeugen mit einem Gewicht von bis zu 15 Tonnen. Zur Erprobung der Werkzeuge stehen Spritzgießmaschinen mit bis zu 16 000 kN Zuhaltekraft bereit. Der unternehmensinterne 24-Stunden-Werkzeugservice steht Kunden von Giebeler bei Bedarf schnell zur Seite. Das Unternehmen nutzt zudem eigene Datenbanksysteme wie die „Giebeler Sphere“, um über eine eigene App jederzeit Zugriff auf aktuelle Projektdaten zu erhalten.
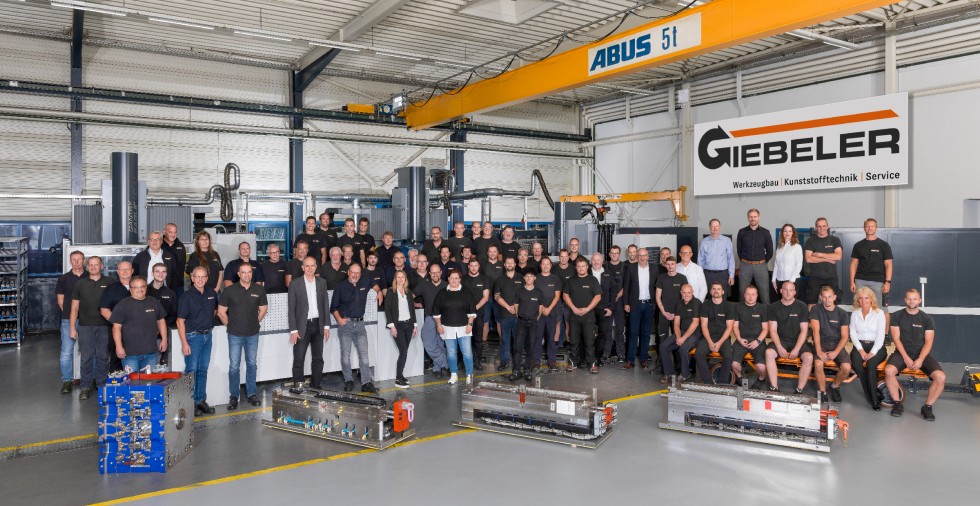
Die Jury beeindruckte vor allem die organisatorischen Exzellenz des Unternehmens: Diese äußert sich besonders in der effizienten Kalkulation anhand einer eigens entwickelten App mit geometrischer Ähnlichkeitsanalyse. Die App versetzt das Unternehmen in die Lage, ähnliche Werkzeuge zu identifizieren und die Aufwände schon im Vorfeld der Herstellung auf Basis von Nachkalkulationen zu bestimmen. Hinzu kommt ein hoher Anteil an fertiggestellten Aufträgen ohne Budget- oder Fristüberschreitung – trotz häufiger später Änderungen durch den Kunden. Eine Besonderheit ist auch das Pay-per-Use-Geschäftsmodell, das Giebeler vorantreibt. Was bei einigen Maschinen im Maschinenpark bereits zum Einsatz kommt, wird jetzt auch bei ersten Werkzeugen getestet. Für die Umsetzung des neuen Geschäftsmodells arbeitet Giebeler eng mit Banken und Start-ups im Bereich der Blockchain-Technologie zusammen.
Mit Investitionen in neue Technologien überzeugt der Sieger der Kategorie „externer Werkzeugbau unter 50 Mitarbeitende“
Als Gewinner in der Kategorie „externer Werkzeugbau unter 50 Mitarbeitende“ kann sich die Primaform AG mit Sitz in Thun in der Schweiz freuen. Das Unternehmen beschäftigt 43 Mitarbeitende und neun Auszubildende. Kerngeschäft des Unternehmens sind komplexe Ein-, Mehrkomponenten- und Hybridwerkzeuge für den Spritzguss in der Medizintechnik- und Healthcare-Branche. Jedes Jahr verlassen 50 bis 60 Werkzeuge mit bis zu 96 Formnestern (Kavitäten) sowie einem Maximalgewicht von 5 t und Seitenlängen von 1 m das Werk in Thun. Der hoch automatisierte Maschinenpark umfasst neben den klassischen Fertigungstechnologien des Werkzeugbaus auch spezielle Prozesse wie das Texturieren von Oberflächen und die Herstellung kleinster Strukturen mit dem Laser. Außerdem stellt die Primaform AG Spritzgießwerkzeuge mit elektrischen Antrieben und eigener Steuerungssoftware her.
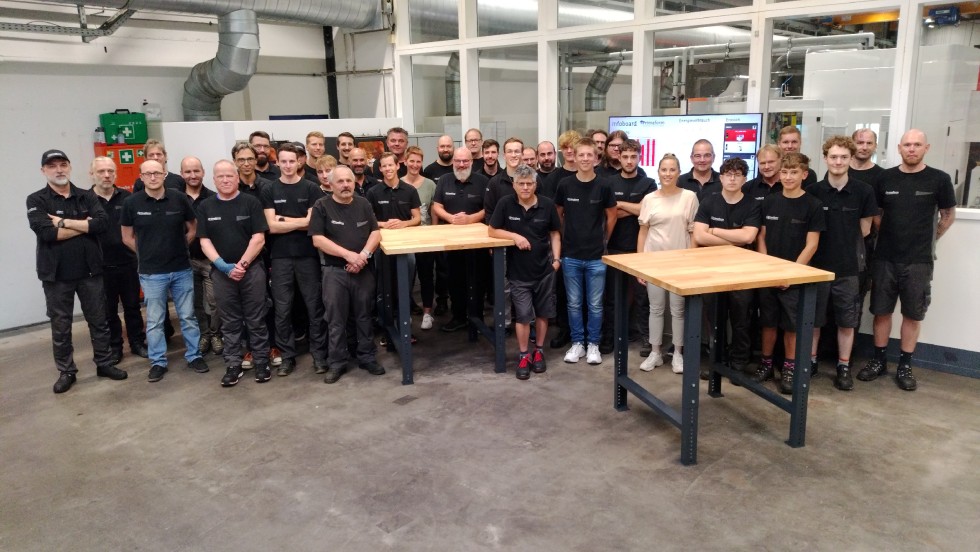
Besonders positiv bewertete die Jury bei Primaform die gezielten Investitionen in neue Technologien wie die Laserstrukturierung und das Nass-Fräsen von Grafitelektroden. Zudem verfüge der Werkzeugbau über ein sehr gutes Montagekonzept nach dem Prinzip der Fließfertigung mit aufgabenbezogenen Arbeitsplätzen, höhenverstellbaren Tischen und Betrachtungslösungen (Viewern) an jedem Arbeitsplatz. Durch hohe Prozesskompetenzen im Fräsen und Erodieren mit hohem Automationsgrad erreicht Primaform sehr hohe Präzisionsbereiche.
Hier erfahren Sie mehr über den Gesamtsieger des Vorjahres
Sonderpreise für den besten Erstteilnehmer und die beste Nachhaltigkeitsinitiative
Zum 20. Jubiläum des Wettbewerbs Excellence in Production (EiP) vergaben die Veranstalter in diesem Jahr erstmals Preise in den Sonderkategorien „EiP-Newcomer des Jahres“ und „beste Nachhaltigkeitsinitiative“. Denn viele Unternehmen sind regelmäßig beim Benchmarkwettbewerb dabei. Bester Newcomer 2023 ist laut Jury die Voss Werkzeugtechnik GmbH, der interne Werkzeugbau der Voss Automotive GmbH. Das Team überzeugte die Jury durch gezielte Investitionen in Maschinen mit hoher Leistungsfähigkeit und hohem Automatisierungsgrad sowie durch den Aufbau einer neuen, komplett klimatisierten Fertigungshalle. Beim Besuch vor Ort glänzte die Voss Werkzeugtechnik auch durch einen hohen Standard an Ordnung und Sauberkeit in der Lagerhaltung sowie auf der gesamten Werkstattebene.
Der Preis für die „beste Nachhaltigkeitsinitiative“ ging an den BMW Werkzeugbau am Standort Landshut. Die Jury sieht den Standort des Automobilbauers als Pionier der Kreislaufwirtschaft. Bereits heute zeichne sich dieser durch hohe Quoten bei der Wiederverwendung der Werkzeugkomponenten aus. Auffällig sei die hohe Präsenz des Themas in den Werkshallen, beispielsweise durch beschriftete Trennbehälter oder das teilweise Energiemonitoring von Maschinen und Anlagen. Besonders lobte die Jury die soziale Komponente der Nachhaltigkeit, die in Form ansprechender Sozialräume, sehr guter Ergonomie an allen Arbeitsplätzen und eines umfangreichen Gesundheitsprogramms für die Mitarbeitenden sowie hoher Inklusionsquote gelebt wird.
Bewerbungsphase für den Wettbewerb 2024 beginnt am 1. Dezember 2023
Auch im kommenden Jahr sollen sich die besten Werkzeug- und Formenbaubetriebe im deutschsprachigen Raum wieder untereinander messen. Ab dem 1. Dezember 2023 können sich interessierte Unternehmen dafür bewerben. Unabhängig davon, ob sie das Finale erreichen, erhalten alle Teilnehmenden des Wettbewerbs eine individuelle Auswertung über ihre Stärken und Verbesserungspotenziale. Detaillierte Informationen zum Wettbewerb und zur Anmeldung gibt es unter: www.excellence-in-production.de