Chemisorption fängt das Quecksilber ab
Abfallverbrennungsanlagen setzen Aktivkohle und Bromsalze ein, um Rauchgas von Quecksilber zu befreien. US-Kohlekraftwerke nutzen diese zum Teil in Deutschland entwickelten Methoden bereits, um ihr Rauchgas von dem giftigen Metall zu verhältnismäßig geringen Kosten zu reinigen.
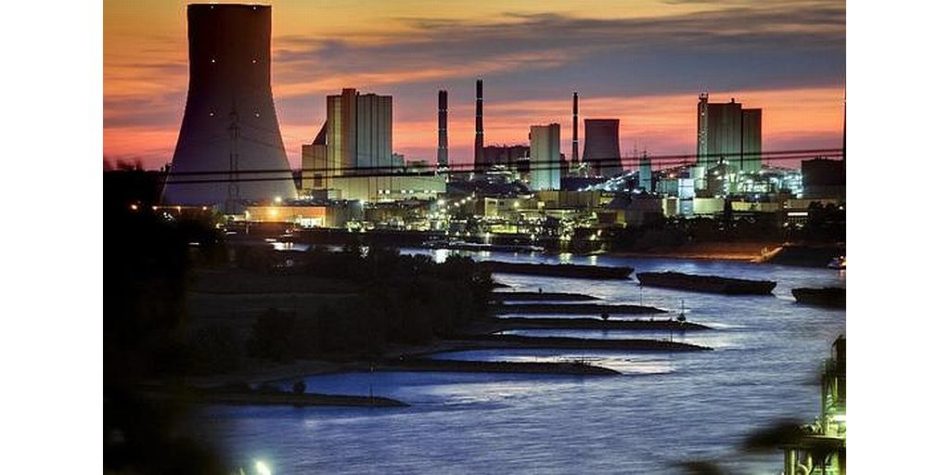
Foto: Thomsa Pflaum/VISUM
Das giftige Schwermetall, das sich in der Nahrungskette anreichern kann, steht derzeit im Mittelpunkt der Umweltpolitik. So haben Vertreter von mehr als 140 Staaten im Januar das Minamata-Übereinkommen mit dem Ziel unterzeichnet, die Emissionen von Quecksilber zu senken.
Gleichzeitig suchen und finden Firmen Wege, den Eintrag von Quecksilber aus Industrieanlagen zu senken. So entwickelt der Essener Energiekonzern Steag in seinem Kraftwerk Herne ein Verfahren, Quecksilber aus dem Waschwasser der Rauchgasreinigung auszufällen und in einem Filterkuchen der Abwasseraufbereitungsanlage anzureichern. Und der Konzern E.on sammelt Erfahrungen mit einem Ionenaustauscher am Kraftwerk Staudinger und mit einer Ultrafiltration am Kraftwerk Heyden.
Abfallverbrennungsanlagen wiederum nutzen seit Jahren Bromsalze wie Kalziumbromid, um den Quecksilberausstoß zu senken. Die Bromide oxidieren metallisches Quecksilber, so dass es sich mit der Rauchgaswäsche aus dem Abgasstrom entfernen lässt. Chemieparkbetreiber Currenta geht diesen Weg in vier Sonderabfallverbrennungsanlagen, ebenso die Emschergenossenschaft in Bottrop und das Tiefbauamt Karlsruhe in Neureut mit jeweils zwei Anlagen zur Klärschlammverbrennung.
Ein anderer Weg ist die Chemisorption mit Aktivkohle. Etwas Theorie: Lagern sich Moleküle an Aktivkohle oder anderen Festkörpern an, sprechen Fachleute von Adsorption. Deshalb wird Aktivkohle eingesetzt, um Rauchgase aus Müllverbrennungsanlagen, Kraftwerken für Ersatzbrennstoffe oder Stahlwerken von Dioxinen, Furanen oder Schwermetallen zu reinigen. Diese Substanzen oder Metalle haften dabei unterschiedlich fest an der porösen Aktivkohle. Steigt die Temperatur, „verdampfen“ einige wieder. Das gilt insbesondere für das leichtflüchtige Quecksilber.
„Diese Rückreaktion lässt sich unterbinden“, weiß Wolfgang Esser-Schmittmann. Der Maschinenbauer ist Geschäftsführer der Firma Carbon Service & Consulting (CSC), einem Hersteller von Aktiv- und Filterkohle aus Vettweiß bei Düren. Der Trick ist, die anhaftende Substanz mit einer weiteren Chemikalie reagieren zu lassen, so dass eine jeweils neue Substanz entsteht, die jedoch nicht von der Kohle verdampft. So wird aus der Adsorption eine Chemisorption.
Um Quecksilber aus den Abgasen zu entfernen, „haben sich Aktivkohlen, die mit 5 % bis 25 % Schwefelsäure benetzt sind, bewährt“, erklärt Esser-Schmittmann. Vermehrt wird auch Aktivkohle eingesetzt, die bis zu 10 % an Bromsalzen enthält. Wird schwefelsäurehaltige Kohle genutzt, entsteht Quecksilbersulfat, bei bromidhaltiger Kohle bildet sich Quecksilberbromid. Beide Salze bleiben an der Aktivkohle haften und werden dann in Gewebe- oder Elektrofiltern aus dem Abgasstrom entfernt.
„Derart imprägnierte Aktivkohle wird vielfach eingesetzt“, weiß Esser-Schmittmann. Enthalten Abfälle oder Sonderabfälle Quecksilber, so werden dem Rauchgas bis zu 100 mg mit Brom oder Schwefelsäure benetzte Aktivkohle pro m³ hinzugegeben. Der Quecksilbergehalt im Abgas lässt sich damit von mehr als 500 µg/m³ auf unter 10 µg/m3 senken. Nach diesem Verfahren arbeiteten mehr als 100 Anlagen in Europa, so Esser-Schmittmann. Auch beim Aufarbeiten schwermetallhaltiger Filterstäube aus dem Altmetallrecycling ist es üblich, mit Aktivkohle den hohen Gehalt an Schwermetallen im Abgasstrom zu verringern.
Sowohl Aktivkohle als auch Bromsalze lassen sich auch in Kohlekraftwerken nutzen. Preiswert sei etwa die Chemisorption, so Esser-Schmittmann. Nötig dazu seien ein Aktivkohlesilo, eine Dosieranlage und eine Einblasvorrichtung. Das alles koste rund 800 000 €. Um 95 % des Quecksilbers aus dem Rauchgas eines Braunkohlekraftwerks zu entfernen, bräuchte es pro m³ etwa 30 mg Aktivkohle, die 5 % Schwefelsäure enthält.
Ein 1000-MW-Braunkohlekraftwerk könnte so 500 t Aktivkohle im Jahr benötigen. Damit entstünden jährliche Betriebskosten von bis zu 400 000 €. Der Strompreis würde sich dann nach Berechnung des CSC-Geschäftsführers um etwa 0,005 ct/kWh erhöhen. „Das liegt im Bereich des Vernachlässigbaren.“ Für eine vierköpfige Familie würde die Stromrechnung bei einem Verbrauch von 4000 kWh/Jahr um 20 Cent teurer.
Mit Aktivkohle oder Bromsalzen schaffen es in den USA bereits rund 100 Kraftwerke, den Quecksilbergehalt im Rauchgas auf unter 1 µg/m³ zu drücken. Rund zwei Drittel dieser Kraftwerke erreichen dies durch kleine Dosiereinrichtungen, mit denen sie Bromidsalze der Kohle vor der Verbrennung zugeben, erklärt Bernhard Vosteen vom Kölner Ingenieurbüro Vosteen Consulting. Das andere Drittel bläst hingegen Aktivkohle vor dem Staubfilter ins Abgas. Das sind oftmals Kraftwerke ohne nasse Rauchgasreinigung, von denen es in den USA einige gibt.
Preiswerter scheint die Bromidzugabe zu sein. Das US-Energieministerium prüfte 2008, wie teuer die jeweilige Methode wäre. Dabei erwies sich die bromgestützte Quecksilberabscheidung als deutlich günstiger. Zum gleichen Ergebnis kommt eine Doktorarbeit aus 2012 von Mark Simpson Berry, Entwicklungsleiter des Energieversorgers Southern Company Services, Alabama/USA.
Doch Quecksilber verschwindet auch so nicht völlig. Wird das Metall an Aktivkohle gebunden, landet es im Filterstaub. Und als Bromid landet es im Abwasser der Rauchgaswäsche, aus dem Gips gewonnen wird. Gips und die Flugasche werden in Deutschland verwertet: Gips etwa in Gipskartonplatten, Flugasche als Klinkerersatz im Zement.
„Hier muss man abwägen“, meint Christian Tebert vom Hamburger Beratungsinstitut Ökopol. Er hält das Emittieren in die Luft für das größere Übel. Werden die mit Quecksilber angereicherten Rückstände als Baustoff verwendet, wäre dieses eine Verbesserung, da das giftige Metall fixiert ist.
Doch jetzt stellen sich neue Fragen: Wird das eingebundene Quecksilber bei Zementkorrosion, beim Abbruch, beim Recycling beziehungsweise der Deponierung wieder frei? Weitere Studien sind also nötig.
Neue Obergrenzen für Quecksilberemissionen
Die EU-Kommission legt in den BVT-Schlussfolgerungen (BVT = beste verfügbare Techniken) für Quecksilber (Hg) „Emissionsbandbreiten“ anstelle von Grenzwerten fest. Diese sollen 2015 verabschiedet werden. Kohlekraftwerke hätten dann vier Jahre Zeit, diese Vorgaben umzusetzen.
Vier Beispiele:
- In bestehenden Steinkohlekraftwerken mit einer Feuerungswärmeleistung von mehr als 300 MW sollen die Betriebswerte bei höchstens 6 µg Hg/m³ liegen.
- Für neue Steinkohlekraftwerke liegt diese Obergrenze bei 2 µg Hg/m³.
- In bestehenden Braunkohlekraftwerken mit einer Feuerungswärmeleistung von mehr als 300 MW sollen die Betriebswerte höchstens 10 µg Hg/m³ betragen.
- Für neue Braunkohlekraftwerke soll die Obergrenze bei 5 µg Hg/m³ liegen.
Zurzeit beraten Fachleute aus Industrie, Behörden und Umweltverbänden über die Werte.