Flutkatastrophe: Wie aus dem Schmutzwasser wieder Wertstoffe werden
Hochwasser: Mit viel Verfahrenstechnik und hartgesottenen Bakterien verwandelt ein niederrheinisches Unternehmen die braune, teils hochbelastete Flut in klares Wasser und Basisöl.

Foto: KS-Recycling
Hier muss niemand daran erinnert werden, einen Mund/Nasen-Schutz zu tragen. In manchen Kellern stinkt es erbärmlich nach Öl und Fäkalien. Der Instinkt mahnt: Nichts wie raus hier!
Aber die Mitarbeiter der KS-Recycling GmbH & Co. KG bleiben standhaft, arbeiten unermüdlich. Sie fahren ihre Tanklaster sogar am Wochenende in die Hochwassergebiete – eine Sondergenehmigung des Bundesverkehrsministeriums macht es möglich. Selbst einige Disponenten des Unternehmens steigen auf den Bock, um zu helfen. „Wenn sich bei dir ein älterer Herr mit Tränen in den Augen von Herzen bedankt, sind alle Strapazen vergessen“, sagt Fahrer Rene van Bebber. Sein Chef, Geschäftsführer Guido Schmidt, ist stolz auf sein Team. „Die Jungs geben wirklich alles!“
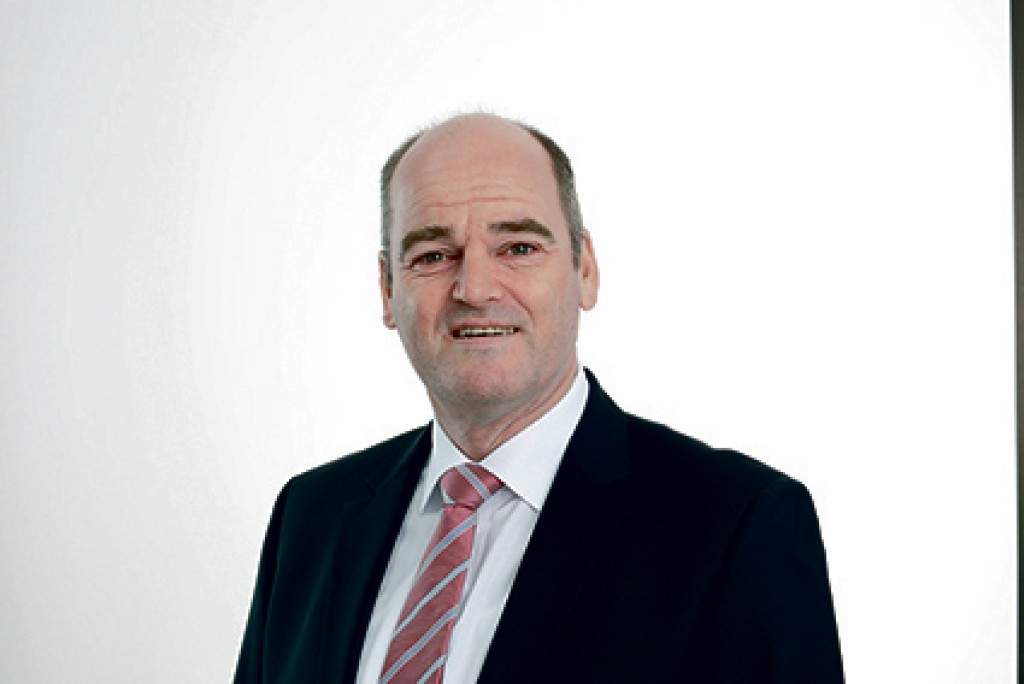
Im Einsatzgebiet suchen die Mitarbeiter zuerst einen festen Standort für ihre gewichtigen Fahrzeuge. Dann rollen sie den Schlauch aus, setzen eine geeignete Lanze auf und versenken sie im belasteten Wasser.
Ausgehärtete Ablagerungen werden „angefluxt“
Nach dem Abpumpen wird verbliebener Restschlamm, der regelmäßig mit Kohlenwasserstoffen belastet ist, mittels Abzieher zusammengeschoben und ebenfalls abgesaugt. Bereits ausgehärtete Ablagerungen werden „angefluxt“, also per Wasserstrahl wieder verflüssigt.
Erster Schritt ist die Eingangsanalyse
Ist der Tankwagen zurück am Hauptsitz des Unternehmens in Sonsbeck, wird zunächst eine Probe entnommen. Dies geschieht mit einem langen Rohr, Durchmesser: 2,5 cm. Dieser „Stechheber“ wird langsam bis auf den Boden des Tanks durchgestochen, um sämtliche Phasen des Inhalts aufnehmen zu können.

Im Labor wird zunächst der Flammpunkt der Probe bestimmt. Das ist die Temperatur, bei der eine Flüssigkeit unter Normaldruck brennbare Gase abgibt. „Wir wollen schließlich keine explosionsgefährlichen Stoffe in Anlagenteile überführen, die dafür nicht geeignet sind“, erläutert Technikchef Wilhelm Schilling.
Im Rahmen der Eingangsanalyse wird außerdem nach PCB (polychlorierten Biphenylen), Halogenen, Schwermetallen, Schwefel und Stickstoff gesucht.

Explosionsgefahr muss auf null gesenkt werden
Ist der Flammpunkt im kritischen Bereich – etwa, weil Benzine enthalten sind –, kommt die mechanisch vorgefilterte Flüssigkeit zunächst in die „Strippkolonne“. Schilling erklärt das Prozedere: „Das Gemisch wird vorsichtig auf 90 °C erwärmt und in einen hohen, schmalen Behälter gegossen.“ Hier trifft das Material auf eine Füllkörperschicht. Es entstünden Tropfen. „In diesen Regen speisen wir von unten Dampf ein. Dieser sorgt für eine Partialdruckabsenkung in der Kolonne. Dadurch verdampfen die Benzine. Sie steigen auf, kondensieren und können aufgefangen werden“, so der promovierte Agraringenieur.
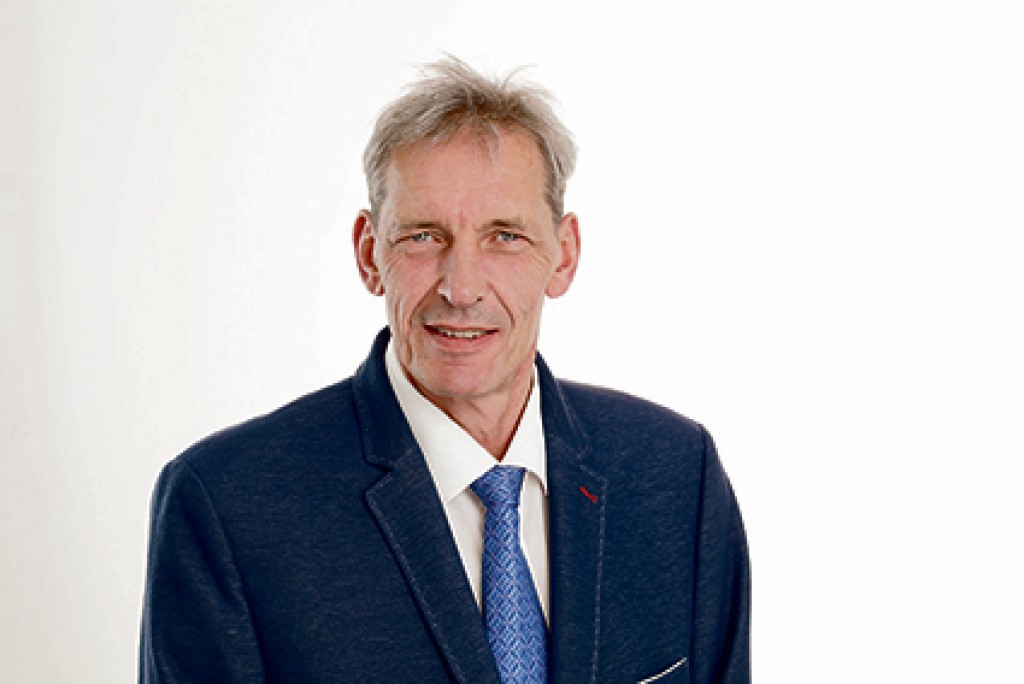
Grober Dreck bleibt vorerst im Dekanter
Sämtliche Anlieferungen ohne kritischen Flammpunkt kommen im ersten Schritt in den „Dekanter“. Hier arbeiten Rotationssiebe und Industriezentrifugen im Durchlaufverfahren. Der Output ist derart frei von Feststoffen, dass sich innerhalb von 24 Stunden nichts mehr absetzt.
„Das Dekantat besteht nur noch aus Wasser sowie allen Flüssigkeiten, die eine geringere Dichte aufweisen – also aufschwimmen“, so Schilling.
Das nun von unten abgesaugte Wasser ist aber noch lange nicht rein. „Aufgrund von Lösungsvermittlern wie Alkoholen und Tensiden sind noch Spuren von Ölen enthalten“, so der 59-Jährige. Um sie zu entfernen, wird die Strippkolonne abermals bemüht.

Restwasser wird totalverdampft
Das resultierende Wasser wird anschließend totalverdampft. Das Destillat hat dann keine wassergefährdenden Eigenschaften mehr. Bevor es in den Rhein geleitet werden darf, muss es aber noch biologisch nachgeklärt werden. Dies passiert im unternehmenseigenen Industrieabwasserklärwerk in Wesel.
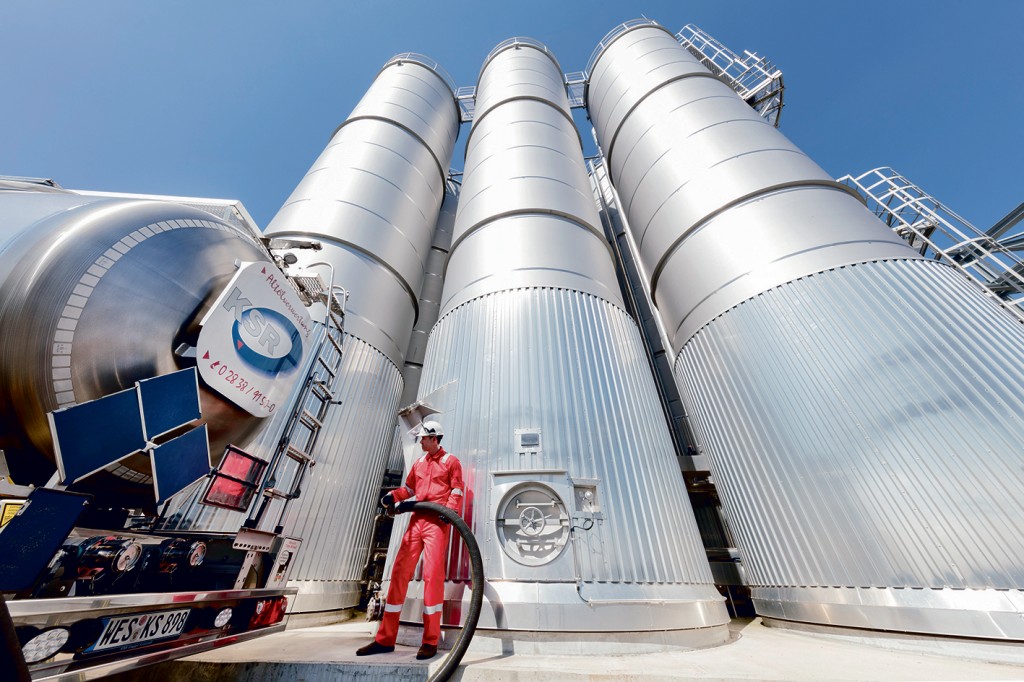
Destillat kommt in fünfstufige Kläranlage
Die aerob betriebene Anlage ist fünfstufig. Zunächst durchläuft das Wasser vier Becken, die nach dem Festbettverfahren funktionieren. In allen schwimmen also Kunststoffkörper, auf denen unterschiedliche Mikrobenpopulationen leben.
Die Bakterien im ersten Becken haben sich spezialisiert auf alles, was schnell abbaubar ist. „Für die sind die Restölverunreinigungen ein ernährungsphysiologischer Supercocktail“, so Schilling. Im zweiten Becken haben sich die Bakterien auf schwere verdauliche Bestandteile spezialisiert. „Diese Kaskade wird bis in die vierte Stufe fortgesetzt“, so der Techniker.
Theoretisch trinkbar
Abschließend kommt das Wasser in ein Belebtschlammbecken, wie man es aus kommunalen Klärwerken kennt. „Die hier lebenden Bakterien kümmern sich um alle Reste. Sie verdauen zu Ende, was ihre winzigen Kollegen zuvor schon anverdaut haben“, erläutert Schilling. Theoretisch sei das Wasser nun trinkbar. Über eine Standleitung wird es in den fließenden Rhein gespeist.
„Unsere Bakterien sind hohe Belastungen mit Altöl, Kühler- und Bremsflüssigkeiten gewohnt“, so Firmenchef Schmidt. „Deshalb konnten wir im Katastrophengebiet so schnell helfen.“
Dekanterinhalt wird erhitzt
Und was passiert mit den hochbelasteten Restflüssigkeiten aus dem Dekanter? „Diese Mischung, bei der es sich vornehmlich um Öle handelt, wird im Vakuum erhitzt“, erklärt Schmidt. Dabei verdampfen das Restwasser und alle leichtflüchtigen Inhaltsstoffe wie etwa Benzine. Das gewonnene Destillat geht im folgenden denselben Weg wie das zuerst aus dem Dekanter abgesaugte Wasser.
Zuerst wird Heizöl abdestilliert
Der im Vakuum zurückbleibende Stoff, das sogenannte Trockenöl, wird nun stufenweise erhitzt. Bei atmosphärischen Temperaturen von 350 °C wird beispielsweise Heizöl abdestilliert. Bei noch höherer Temperatur werden die „Flash-Öle“ gewonnen. „Das ist der Teil, der mal als Motor- und Schmieröl genutzt wurde“, so Schmidt.
Bleicherde sorgt für die richtige Optik
Um das Flash-Öl von letzten Unreinheiten zu befreien, wird es bei hohen Temperaturen mit stark absorbierender Bleicherde versetzt. Dieses wie Katzenstreu wirkende Material wird später abgefiltert und ausgepresst. Übrig bleibt das Zielprodukt: reines Basisöl.
„Das verkaufen wir an Finisher. Die machen daraus – je nach zugegebenen Additiven – etwa Motor- oder Getriebeöl“, erklärt Schmidt. Die zuerst abgeschiedene Heizölphase wird in Großmotoren oder in industriellen Heizanlagen verfeuert.
„Höchstens 2 % sind für die Tonne“
Auch der Bodensatz aus der Vakuumkammer ist noch nutzbar. „Der geht als Bitumen in den Straßenbau“, so Schmidt. Richtiger Abfall entsteht also kaum. „Von allem, was wir abpumpen und aufkehren, sind am Ende höchstens 2 % für die Tonne“, so Schmidt.