Gerettet? Recycling von faserverstärkten Kunststoffen
Haben Bauteile aus faserverstärkten Kunststoffen ausgedient, beginnen die Probleme. Ein Recycling der Fasern in brauchbarer Qualität ist schwierig, aber möglich.
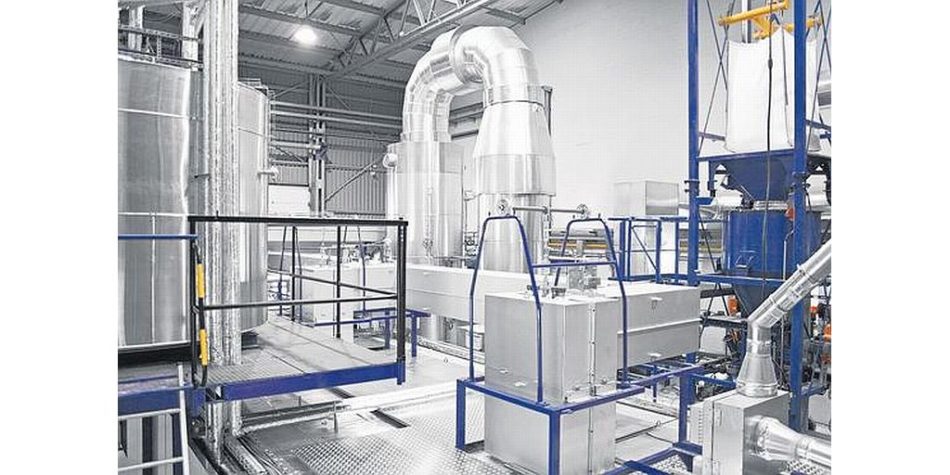
Foto: CFK Valley Stade Recycling GmbH & Co. KG
Fantastische Werkstoffeigenschaften, katastrophales Recyclingverhalten: Auf diese einfache Formel könnte man carbon- (CFK) und glasfaserverstärkte Kunststoffe (GFK) bringen. Was also tun, wenn Elektronikgehäuse, Karosseriebauteile, Flugzeugrümpfe und sogar ganze Rotorblätter von Windkraftanlagen aufs Altenteil müssen?
Klar ist: Weder CFK noch GFK dürfen in der EU auf die Deponie. Also ab in die Müllverbrennungsanlage? Das nutzt nichts, denn Carbon wird in der Hitze kaum verändert und landet dann in der Schlacke, wo es nichts verloren hat. „Carbonfaserabfälle sind definitiv ungeeignet für die Müllverbrennung“, urteilt Carsten Spohn, Geschäftsführer der Interessengemeinschaft der thermischen Abfallbehandlungsanlagen in Deutschland (ITAD). Sie könnten sogar technische Schäden verursachen. „Deshalb sollten sie nicht in unsere Anlagen gelangen.“
Wie sich Carbon im Verbrennungsprozess verhält, untersucht Peter Quicker an der RWTH Aachen. Der Chemieingenieur bestätigt: „Eine vollständige Zerstörung ist mit den üblichen Verbrennungsverfahren für Abfälle nicht möglich.“ Im Experiment fand er extrem kleine Faserbruchstücke, die das Lungengewebe durchdringen können und daher als krebserregend einzustufen seien.
Die Recyclingwirtschaft ist sensibilisiert: „Die Entsorgungssicherheit ist in Gefahr. Hohe Mengen Shredderfraktionen etwa aus Altfahrzeugen können bald nicht mehr entsorgt werden“, warnt Klaus Hauschulte, CEO der Scholz Recycling GmbH in Essingen.
Es müssen deshalb Recyclingkonzepte her, die ihrem Namen gerecht werden, die also statt Zerstörung neue Verwendungszwecke finden. Doch die Suche ist schwierig. Das Problem: Carbonfasern sind schon extrem langlebig. Eingebettet in eine Matrix aus thermoplastischen Kunststoffen – etwa Polyamid, Polypropylen und Peek – oder aus Duromeren wie Epoxid- und Phenolharzen, sind sie nahezu unzerstörbar.
Dennoch zählt die Pyrolyse, also die Verbrennung, neben der Solvolyse, der Abtrennung mit speziellen Flüssigkeiten, zu den wenigen Verfahren, mit denen man die Fasern überhaupt aus der Matrix herauskriegt.
Verfahren zum Faserrecycling
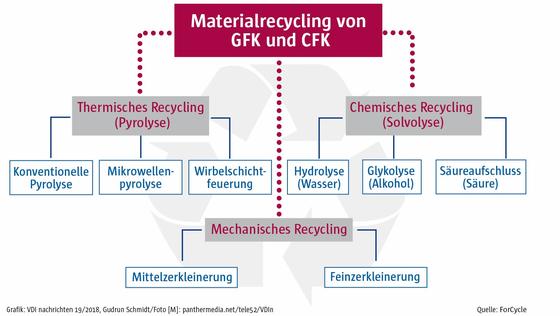
Thermisches Recycling: Benetzte Carbonfasern, unausgehärtet oder als fertiges CFK-Bauteil, werden der Pyrolyse ausgesetzt. Bei bis zu 600 °C verbrennt die Matrix und gibt die Carbonfaser frei. Um dabei eine Oxidation der Fasern zu vermeiden, erfolgt dies unter Schutzgasatmosphäre.
Mechanisches Recycling: Trockene Carbonfasern, die noch nicht mit Kunststoff imprägniert sind, werden gemahlen oder geschnitten. Sie lassen sich als Verstärkungsfaser oder Füllstoffe in Spritzgussgranulaten, Pressmassen und Bauprodukten einsetzen.
Chemisches Recycling: Bei der Solvolyse werden superkritische Flüssigkeiten zur Trennung von Faser und Matrix eingesetzt. Beim Übergang von der flüssigen in die gasförmige Phase ist z. B. Propanol in der Lage, die Matrix fast vollständig von der Faser zu lösen.ber
Dafür aber braucht es Spezialöfen. Die CFK Valley Stade Recycling GmbH in Wischhafen betreibt eine Anlage, die das kann. Carbonfaserhaltige Produktionsreste sowie ausrangierte Bauteile aus ganz Europa werden hier in hochwertige Fasern zurückgeführt.
Trockene Faserreste, vorimprägnierte Strukturen, die sogenannten Prepregs, und sogar vollständig ausgehärtete CFK-Bauteile landen zerkleinert im Pyrolyseofen. Bei über 500 °C und unter Sauerstoffabschluss werden die organischen Moleküle der Teile mit Kunststoffmatrix zerlegt. Sie entweichen als Gas, die Fasern bleiben zurück – mit nahezu unbeschädigter Oberfläche.
Das Gas wird aufgefangen, einer Rauchgaswäsche unterzogen und nachverbrannt. So treibt es die Pyrolyse zusätzlich an. „Im stabilen Prozess ist keine zusätzliche Energie nötig“, heißt es dazu bei CFK Valley Stade Recycling. Die Anlage arbeitet im großtechnischen Maßstab. Der Andrang sei gewaltig, man habe die Kapazitätsgrenzen längst erreicht.
Die isolierten Fasern können nun zu Pellets oder Fasermehl zermahlen und als Füllstoffe in Spritzgussgranulaten oder Bauprodukten eingesetzt werden. Oder die Fasern erhalten eine spezielle Beschichtung, mit der sie sich in eine andere Matrix einbinden lassen. So werden CFK-Abfälle erneut zum Rohstoff für die Kunststoffindustrie.
Am Kunststoff-Institut Lüdenscheid zum Beispiel mischen Ingenieure das Fasermehl einem geschmolzenen Polyamidgranulat bei, ziehen daraus Stränge und schneiden diese wieder zu Granulat. Erneut aufgeschmolzen geht es in die Spritzgussmaschine – etwa um Gehäuse für Elektronikgeräte mit hoher Stabilität, aber geringer Wandstärke herzustellen.
Aus dem Verschnitt von Carbonmatten wiederum, dessen Fasern vorsichtig aus dem Gewebe vereinzelt werden, hat Henrik Dommes vom Faserinstitut Bremen Organofolien entwickelt. Gemeinsam mit der TU Clausthal wurde eine Rüttelmaschine gebaut, die die Fasern der Länge nach ordnet, ohne sie zu beschädigen. Nebeneinander fallen sie auf eine selbstklebende Folie. Mehrere Lagen werden zur Organofolie gepresst, die sich wie Carbonmatten verarbeitet lässt. Die Uni Bremen hat die Folie zum Patent angemeldet. „Damit können kostengünstig hochwertige Artikel für unterschiedliche Märkte gefertigt werden“, ist Dommes überzeugt.
Bleibt die Frage, ob sich glasfaserverstärkte Kunststoffe (GFK) im Recyclingprozess ähnlich verhalten wie CFK oder ob sie andere Technologien erforderlich machen. „Der Verbund, der mit Harzen hergestellt worden ist, muss aufgelöst werden. Das ist bei beiden Werkstoffen so“, erklärt Henning Albers von der Hochschule Bremen. Dafür brauche es thermische Verfahren.
Erste Versuche, GFK mithilfe von Pyrolyse aufzuspalten, hatten vor Jahren dänische Forscher gestartet. Sie seien aber nicht weiterverfolgt worden, sagt der Experte für Kreislaufwirtschaft und Abfallbehandlungstechnologien. „Die University of Strathclyde im schottischen Glasgow forscht aktuell im Labormaßstab an dieser Thematik. Großtechnisch verwertbare Ergebnisse liegen aber noch nicht vor“, sagt Albers.
GFK werden oft in großen Bauteilen wie Rotorblättern von Windkraftanlagen verbaut. Die Zerkleinerung dieser riesigen Strukturen sei eine technische Herausforderung. Das Hauptproblem aber, so Albers, sei die fehlende Nachfrage. „Glasfasern werden so kostengünstig hergestellt, dass am Recyclingprodukt niemand echtes Interesse hat.“
Das ist bei CFK anders. Ist die Ursprungsfaser erst von der Matrix getrennt, eröffnen sich gegenwärtig immer neue Wege zu einer sinnvollen Verarbeitung. Viele, davon sind Branchenkenner überzeugt, seien heute schon erfolgversprechend.