Kunstleder für Möbel und Autositze endlich recycelbar
Weil aus verschiedenen Materialien verschweißt, konnte Kunstleder nach der Nutzung bisher nur verbrannt werden. Nun aber hat ein Team an den DITF Kunstleder biobasiert und recycelbar hergestellt.
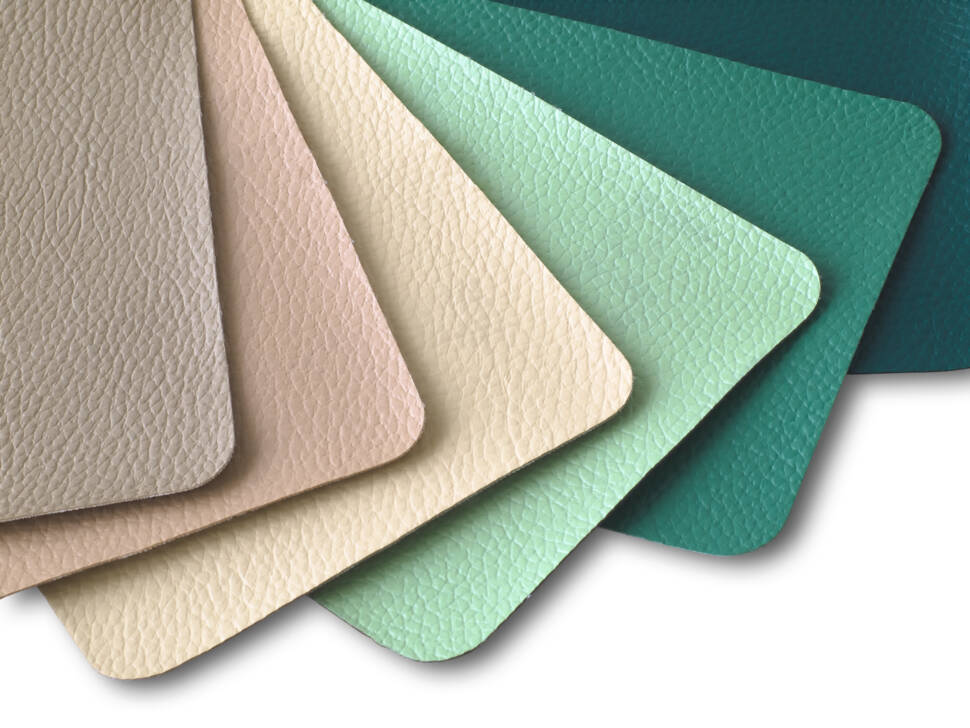
Foto: PantherMedia / Ann Bastarache
Es war beim Kunstleder ähnlich wie bei Getränkekartons für Milch und Saft: Verschiedene Materialien sind dort hauchdünn miteinander verschweißt, um die jeweiligen Funktionen optimal zu verbinden. Da sich diese aber nicht mehr trennen lassen, war an Recycling nicht zu denken. Nach der Nutzung ging es deshalb in die Müllverbrennungsanlage. Nun aber hat ein Team der Deutschen Institute für Textil- und Faserforschung Denkendorf (DITF) ein biobasiertes und biologisch abbaubares Kunstleder entwickelt, das die hohen Anforderungen der europäischen Ökodesignverordnung erfüllt.
Kunstleder ist nicht nur eine vegane Alternative für Taschen und Schuhe aus Tierhaut. Es wird auch für Sportgeräte sowie für Möbel und Autositze verwendet. In der Regel besteht es aus einem Trägergewebe aus Polyamid, Baumwolle oder einem Gemisch mit PET. Darauf aufgebracht ist eine Kunststoffschicht aus zwei Materialien – einem Haft- und einem Deckstrich, der dann auf die typische Weise wie Rindleder geprägt ist. Üblicherweise werden für diese Beschichtungen PVC oder verschiedene Polyurethane eingesetzt.
Kreislaufwirtschaft und Ökodesign-Verordnung der EU waren ausschlaggebend
Einen solchen Materialverbund sortenrein aufzuspalten und wiederzuverwenden, ist nahezu unmöglich. Von biologischer Abbaubarkeit gar nicht zu reden. Dabei sind Ressourcenschutz und Nachhaltigkeit von Produkten in der sogenannten Sustainable Products Initiative (SPI) der Europäischen Union festgeschrieben. Um den Anforderungen der Ökodesign-Verordnung gerecht zu werden, wurde jetzt im Rahmen eines AiF-Vorhabens in enger Kooperation der DITF mit der Freiberg Institute gGmbH (FILK) ein Kunstleder entwickelt, bei dem Fasermaterial und Beschichtungspolymer identisch sind. Die Arbeitsgemeinschaft industrieller Forschungsvereinigungen „Otto von Guericke“ (AiF) ist ein Netzwerk aus ca.a 100 Forschungsvereinigungen aus Industrie und Dienstleistungsunternehmen, das angewandte Forschung und Entwicklung der mittelständischen Wirtschaft fördert.
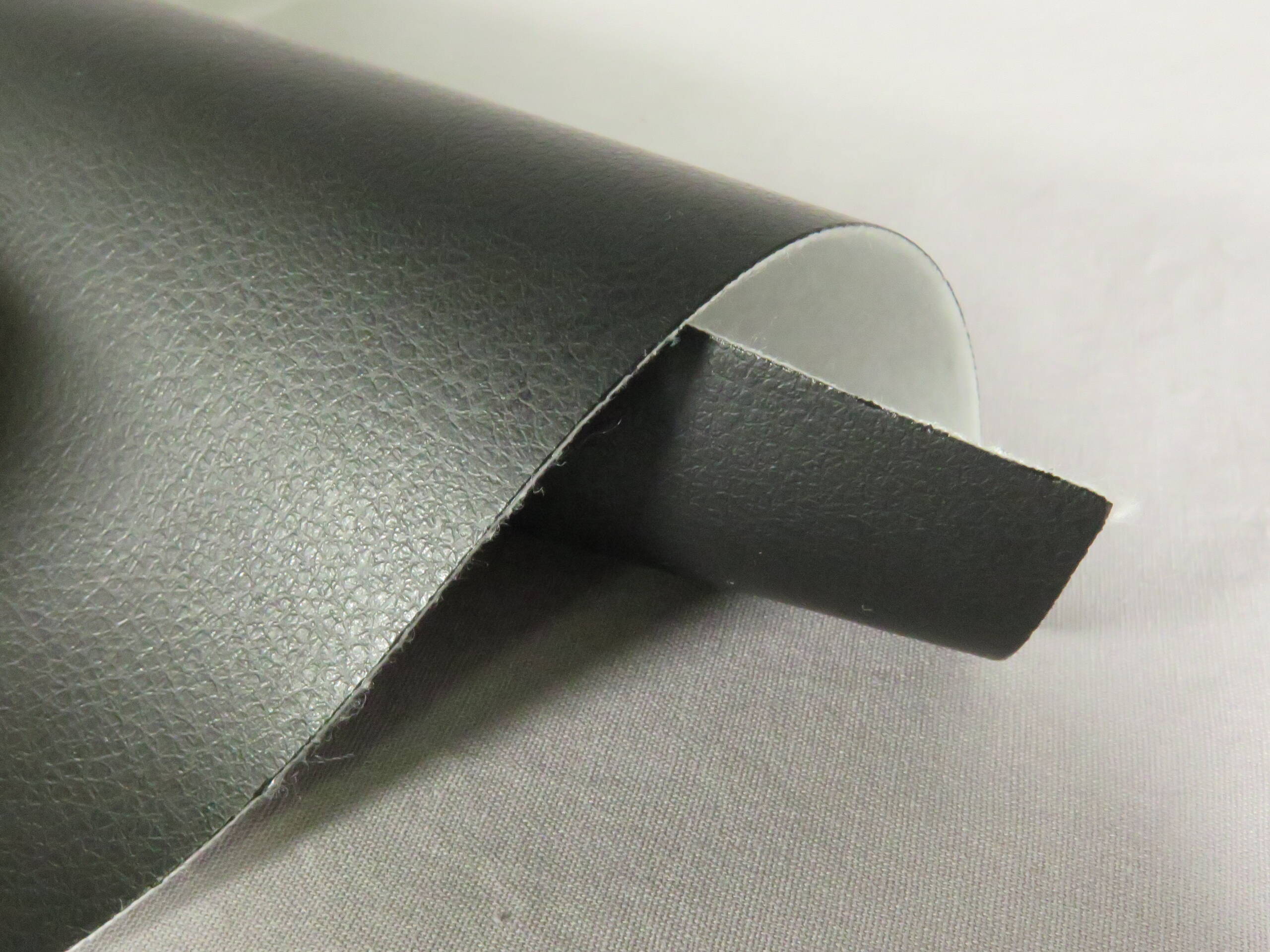
Das Team nahm Polybutylensuccinat (PBS), das sich aus nachwachsenden Rohstoffen gewinnen lässt, als Grundmaterial. Es ist ein Polyester, das heutzutage in verschiedenen Qualitäten und vor allem größeren Mengen am Markt zu haben ist. Seine biologische Abbaubarkeit hat es bereits mehrfach unter Beweis gestellt. Ein Vorteil: PBS lässt sich thermoplastisch verarbeiten, sowohl als Fasermaterial für das Trägergewebe als auch für die Beschichtung. Die thermoplastischen Eigenschaften begünstigen zudem das spätere Recycling.
Anpassung im Spinnprozess
Das Team an den DITF hat das übliche Verfahren für den Primärspinnprozess so angepasst, dass bei relativ hohen Geschwindigkeiten PBS-Filamente mit guten textilmechanischen Eigenschaften produziert werden. Wie die Fachleute sagen, ließen sich bis zu 3000 m Garn pro Minute ausspinnen. Verstreckt weisen sie eine Festigkeit von knapp 30 cN (CentiNewton) auf. Die Verstreckung ist nötig, weil die Moleküle in Chemiefasern nach dem Spinnen noch nicht optimal ausgerichtet sind. Resümee der Textilforscher: Die Garne ließen sich problemlos zu Geweben aus reinem PBS verarbeiten, die am FILK als textiles Grundsubstrat für die Extrusionsbeschichtung ebenfalls aus PBS genutzt wurden.
Lesetipp: Dünnwandige Joghurtbecher aus PET werden recyclingfähig
Mit optimierten Fertigungsschritten ließen sich so PBS-Verbundmaterialien mit dem typischen Aufbau für Kunstleder herstellen. Sortenreinheit und biologische Abbaubarkeit erfüllen die Voraussetzung für einen geschlossenen Recyclingprozess.