Stahl: Diese Anlagentechnik wird bei Thyssenkrupp und Co. den Hochofen ablösen
Jahrzehntelang war der Hochofen das Kernaggregat zur Erzeugung von Stahl, nun wollen ihn die Stahlkonzerne unbedingt loswerden. Die Zukunft gehört der Direktreduktion mit Erdgas und Wasserstoff. Ein Techniküberblick.
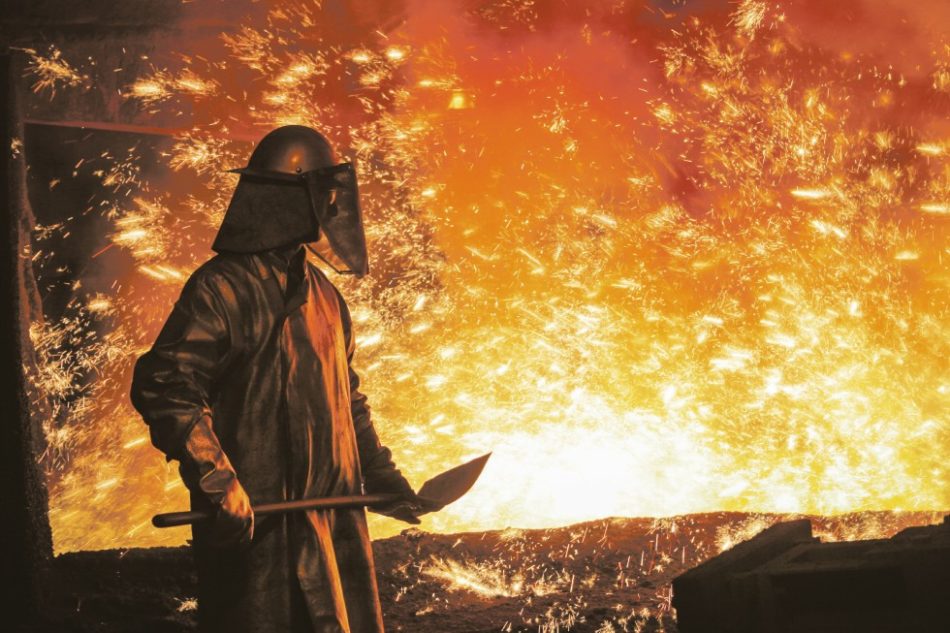
Foto: Salzgitter AG
Inhaltsverzeichnis
- Salzgitter, Voestalpine & Co. – Stahlhersteller unter Druck
- So funktioniert Direktreduktion
- Der Marktführer: Midrex
- Die Nummer 2: Energiron
- Höhere Drücke im Energiron-Reaktor
- Der Trick mit der Dichtung
- Hauptunterschied: Reformer vs. Prozessgaserhitzer
- Direktreduktion mit Wasserstoff
- Jahrhundertinvestitionen in der Stahlindustrie
- Subventionen für grünen Stahl: Warten auf Brüssel
- 2025 könnten die ersten Hochöfen abgeschaltet werden
- Knappheit beim Eisenerz befürchtet
- Wie wird grüner Stahl auf DRI-Basis hergestellt?
- Zusätzliches Schmelzaggregat
- Tata Steel: Vorteil Seehafen
Die Stahlindustrie hat ein Kohlendioxidproblem. Im Jahr 2019 emittierten die Eisenhütten in Deutschland 37,2 Mio. t CO2, was einem Anteil von 4,6 % an den Gesamtemissionen entsprach. Das meiste davon entfiel auf die Hochöfen, in denen der Rohstoff Eisenerz (Fe2O3) zu Eisen reduziert wird.
Und das Problem verschärft sich. Wenn die Hütten zunehmend für ihre CO2-Emissionen zahlen müssen – bislang sind sie in großem Stile davon befreit –, reduziert der Hochofen nicht mehr nur Eisenerz, sondern auch Betriebsvermögen. Der Hochofen, seit jeher der Taktgeber, nach dem sich die Stahlproduktion richtet, ist zur Zumutung geworden.
Salzgitter, Voestalpine & Co. – Stahlhersteller unter Druck
Noch betreiben sieben Konzerne in Deutschland, Österreich und den Niederlanden neun integrierte Hüttenwerke: Standorte mit Hochofen und angeschlossenem Stahlwerk. Jetzt ist die Perspektive, dass die drei Staaten im Jahr 2045, vielleicht früher, hochofenfrei sind. In einer Branche, in der Investitionen leicht in den dreistelligen Millionenbereich gehen, ist das nicht viel Zeit; die europäischen Stahlkonzerne stehen unter Druck.
Darüber, wie das Kohledioxidproblem zu lösen sei, sind sich alle einig – mittlerweile. Noch vor vier Jahren wollten die einen das Hochofengas auffangen und zu Chemikalien verarbeiten, andere wollten es im Boden verpressen. Nur eine Minderheit hatte schon 2018 den Plan, den heute alle haben: Direktreduktion.
So funktioniert Direktreduktion
Im Hochofen wird Kokskohle genutzt, um aus Eisenerz Roheisen zu machen. Und wo Kohle eingesetzt wird, entsteht Kohlenstoffdioxid. Eine Direktreduktionsanlage (DRI-Anlage) kommt hingegen ohne Kokskohle aus. Heutige Aggregate nutzen für die Reduktion vor allem Erdgas und emittieren deshalb grob gerechnet nur halb so viel CO2 pro Tonne Stahl wie ein Hochofen. Auch für die deutschen Hüttenwerke ist zunächst der Erdgasbetrieb geplant – zumindest war das vor dem Ukrainekrieg der Plan. Mit der Zeit soll immer mehr Wasserstoff eingesetzt werden. Unterm Strich sind die Emissionen deutlich CO2-ärmer und wasserreicher.
Völlig neue Anlagen werden für diese Art der Stahlproduktion benötigt (s. Infokasten). Im Hochofen wird das Eisen aufgeschmolzen und beim Abstich ausfließen gelassen. Direktreduktion bedeutet demgegenüber, dass das Eisen nie flüssig ist. Eine Direktreduktionsanlage ist ein Schachtofen. Oben werden Eisenerz-Pellets eingefüllt, die kontinuierlich hinuntersacken. Zeitgleich strömt Reduktionsgas – Kohlenmonoxid (CO) und Wasserstoff (H2) – den Ofen hinauf. Das Gas beraubt das Eisen der Sauerstoffatome. So wird aus Fe2O3 erst Fe3O4, dann FeO und schließlich Fe, also Eisen mit ein bisschen Kohlenstoff, das unten als fester, kugelförmiger Eisenschwamm herausfällt. Dieses reduzierte Eisen wird im Stahlwerk anschließend zu Stahl legiert.
Das Direktreduktionsverfahren ist nicht neu; in vielen Staaten sind bereits Anlagen in Betrieb. ArcelorMittal betreibt zum Beispiel im Elektrostahlwerk Hamburg eine DRI-Anlage mit einer Kapazität von 600 000 Jahrestonnen. Durchgesetzt hat sich das Verfahren aber vor allem dort, wo Erdgas günstig ist, etwa in Russland, in den USA und auf der arabischen Halbinsel. Der Anlagenbauer SMS group schätzt die weltweit installierte Kapazität auf annähernd 100 Mio. t. Zum Vergleich: Weltweit wurden 2021 1,9 Mrd. t Stahl produziert.
Bis heute gibt es nur zwei maßgebliche Typen von Direktreduktionsanlagen: Midrex und Energiron. Midrex ist zugleich der Name des US-Unternehmens, das die Anlagen plant. Energiron ist eine Gemeinschaftsentwicklung der italienischen Anlagenplaner Tenova und Danieli.
Der Marktführer: Midrex
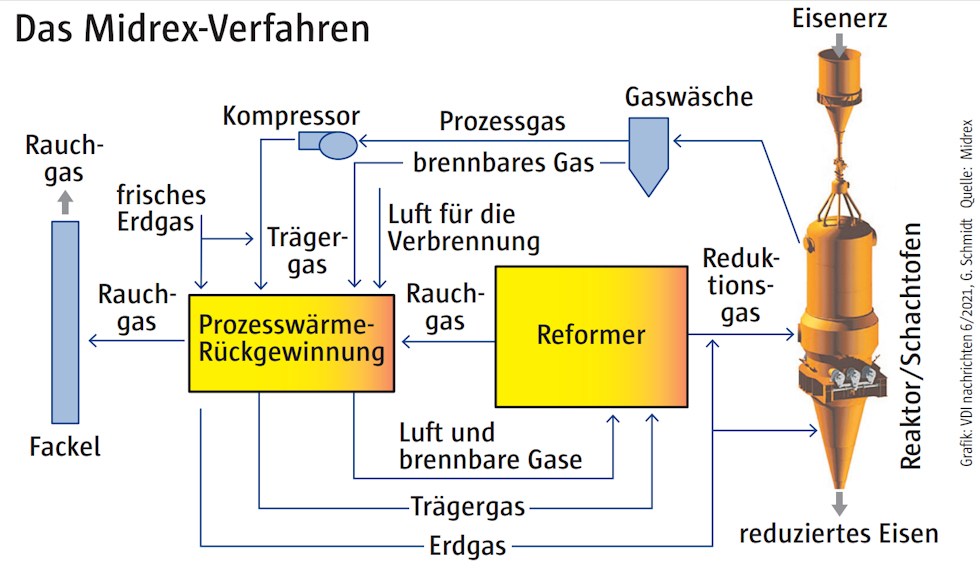
Das Midrex-Verfahren ist auf einen externen Reformer angewiesen, in dem Methan (CH4) in die Reduktionsgase Wasserstoff und Kohlenstoffmonoxid gecrackt wird. Das Reduktionsgas wird bei einem vergleichsweise moderaten Druck von 2,5 bar und bei einer Temperatur um 950 °C in den Reaktor eingebracht. Oben am Schachtofen wird das CO2– und wasserreiche Abgas aufgefangen und abgekühlt, sodass das Wasser heraustropfen kann. Das CO2 gelangt in den Reformer und der Prozess beginnt von vorn.
Die Nummer 2: Energiron
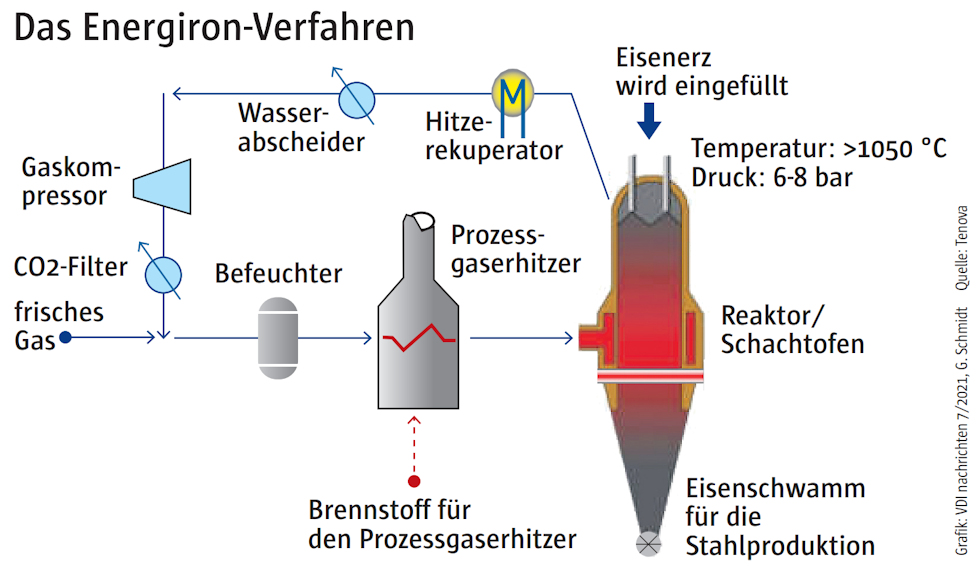
Im Energiron-Reaktor sind die Drücke höher – 6 bar bis 8 bar – und es ist mit 1050 °C bis 1080 °C auch etwas heißer. Das CO2 wird chemisch aus dem Abgas herausgewaschen und kann vermarktet werden. Der restliche Gasstrom wird befeuchtet, mit frischem Erdgas versetzt, in einem Prozessgaserhitzer erwärmt und schließlich in den Reaktor gebracht.
Es gibt einige wesentliche Unterschiede (s. Tabelle). Dazu zählen neben den Reaktordrücken und -temperaturen das Erdgas-Reforming, die Abdichtung des Reaktors, die CO2-Abscheidung und die Umrüstbarkeit auf Wasserstoffbetrieb.
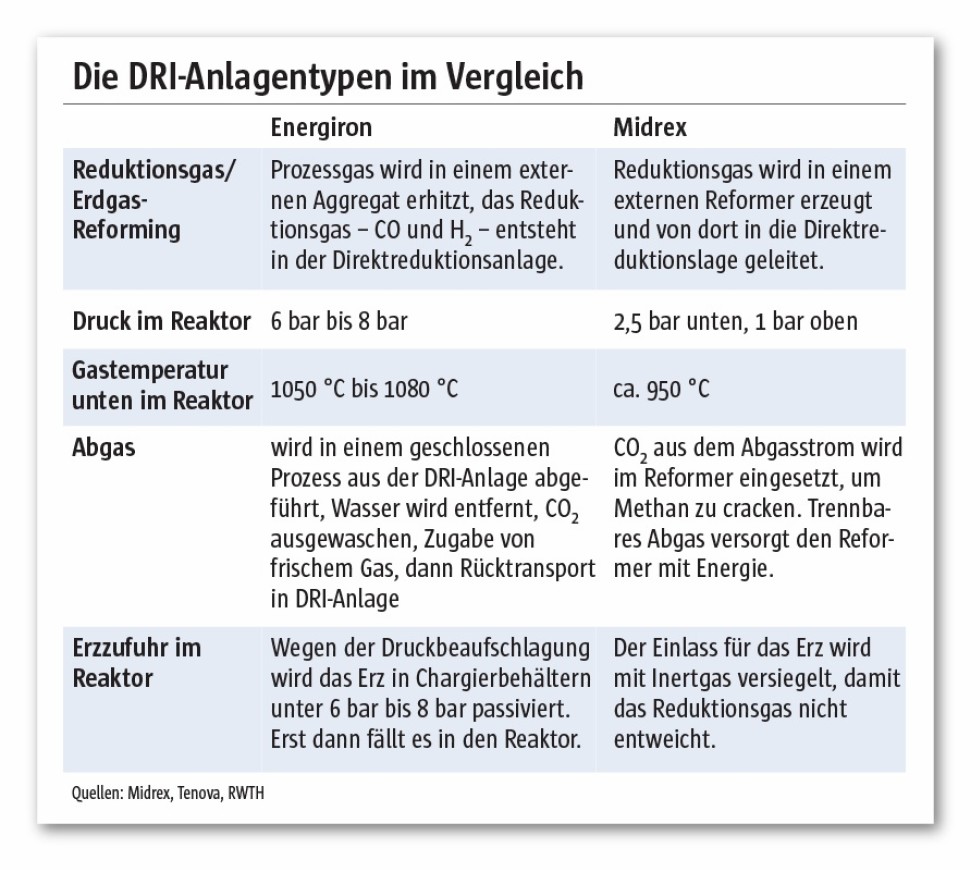
Höhere Drücke im Energiron-Reaktor
Durch den hohen Druck im Reaktor ist nach Tenova-Angaben die Strömungsgeschwindigkeit des Gases niedrig. Viel Reduktionsgas ist also lange im Reaktor – mit positiven Effekten für die Durchgasung und die Reduktion des Eisens.
Zudem wirken sich die hohen Drücke auf den Kohlenstoffgehalt des Eisens aus. Eisen hat einen Schmelzpunkt von 1538 °C. Wenn sich 4,3 % Kohlenstoff in der Matrix einlagern, sinkt der Schmelzpunkt auf 1147 °C. Ein hoher Kohlenstoffgehalt des Eisens ist auch im Stahlwerk erwünscht, genauer: im Elektrolichtbogenofen. Hier entsteht mit eingeblasenem Sauerstoff CO, das die Schlacke im Ofen aufgehen lässt, wie einen Hefeteig. Die Schaumschlacke hüllt den Lichtbogen ein, wodurch sich die Wärmeenergie besser verteilt. Laut Tenova ist Energiron der einzige DRI-Prozess, der mehr als 2,5 % Kohlenstoffgehalt ermöglicht.
Der Trick mit der Dichtung
Midrex nutzt rund um den Erzeinlass und den Eisenauslass Inertgassiegel. Ähnlich den Warmluftschleusen an Kaufhaustüren sorgen sie dafür, dass das Reduktionsgas nicht entweicht.
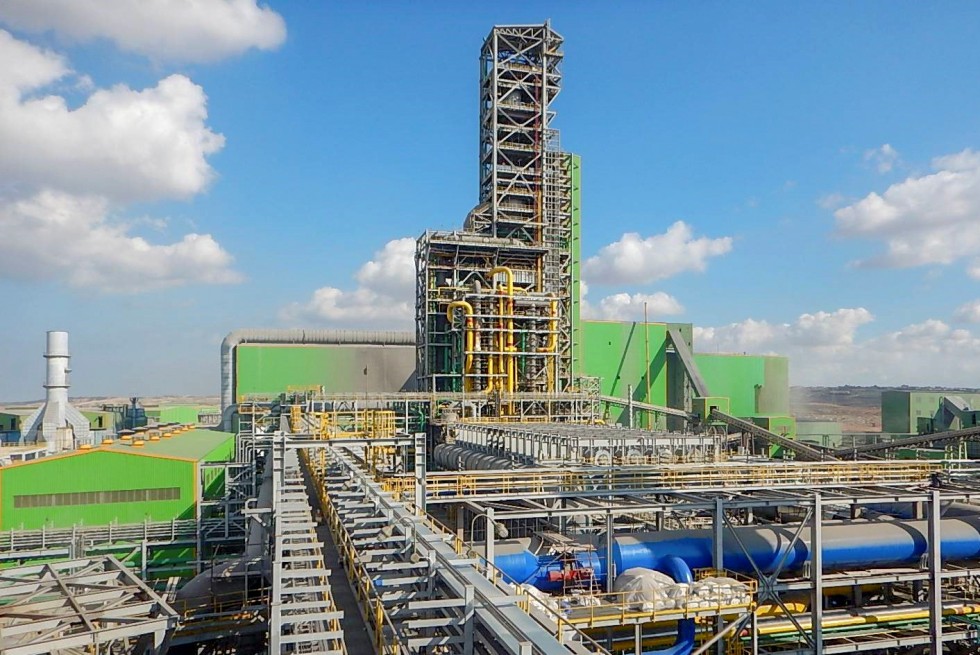
Im Energiron-Prozess kommen mechanische Dichtungen zum Einsatz. Die Erzpellets werden in einem Chargierbehälter unter Druck gesetzt und erst dann in den Reaktor gegeben. Markus Dorndorf, Vice President Iron & Steel Making bei Tenova, spricht von einem „Schleusenprinzip ähnlich wie auf einer Raumstation“.
Hauptunterschied: Reformer vs. Prozessgaserhitzer
Bei Midrex ist der Reformer ein externes Aggregat, das auf CO2 aus dem Abgasstrom des Reaktors als Sauerstoffquelle angewiesen ist. Das Reforming ist ein endothermer Prozess: Es muss also Wärmeenergie hineingesteckt werden. Dadurch, dass dieser Prozess außerhalb des Reaktors stattfindet, sind die Reaktortemperaturen laut Midrex niedriger; die Gefahr, dass die Eisenpellets verkleben, sinkt.
Bei Energiron gibt es keinen eigenen Reformer, sondern einen Prozessgaserhitzer. Das eigentliche Reforming des Erdgases geschieht im Reaktor, der dafür nötige Sauerstoff stammt aus dem Eisenerz. Laut Markus Dorndorf ist das beim Umstieg auf Wasserstoff ein Vorteil. Energiron biete „die Flexibilität, mit demselben Anlagenaufbau jede Art von Reduktionsgas in verschiedenen Mischungsverhältnissen zu verwenden, von Erdgas über Koksofengas bis hin zu Wasserstoff“.
Direktreduktion mit Wasserstoff
Für den Energiron-Prozess gilt: Wenn der Anteil des Wasserstoffs am Reduktionsgas über einen Schwellenwert klettert, wird die CO2-Wäsche für den Abgasstrom nur noch im Standby betrieben. Auch Midrex würde für den Wasserstoffbetrieb einen Prozessgaserhitzer nutzen – oder mit dem Reformer heizen. Der RWTH-Metallurge Dieter Senk sieht Energiron im Vorteil: Das Verfahren biete „die große Chance, mit mehr Wasserstoff und weniger Erdgas zu arbeiten“.
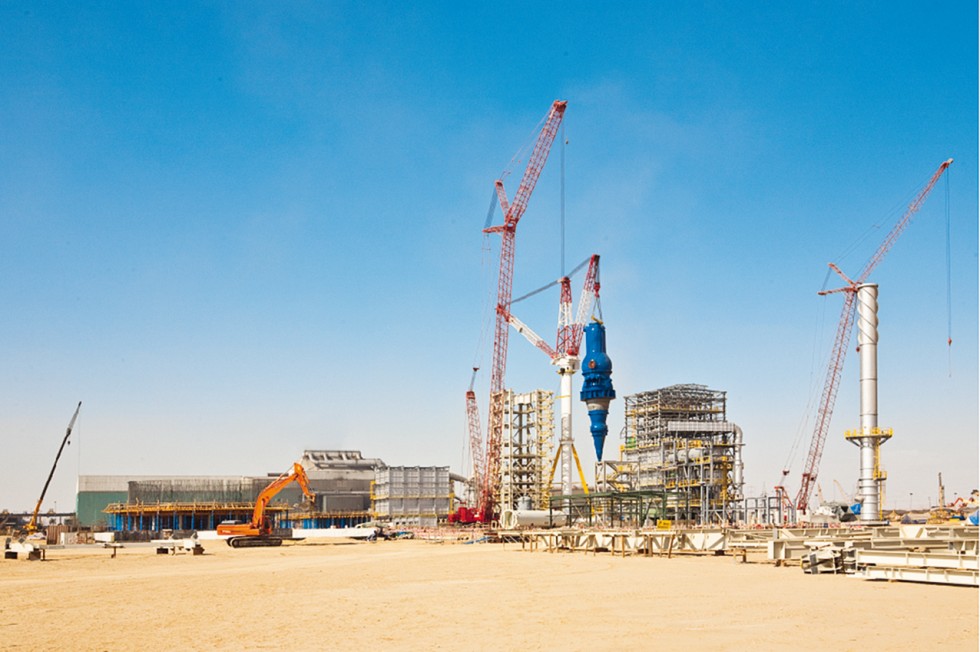
Die größten Hochöfen produzieren zwischen 3,6 Mio. t und 4 Mio. t Roheisen pro Jahr. Solche Größenordnungen zeichnen sich bei den DRI-Anlagen noch nicht ab. Die größten Anlagen beider Typen rangieren um 2,5 Mio. t Jahreskapazität. „Wir haben ein Design für 3 Mio. Jahrestonnen, aber das größte kommerziell bewährte Design schafft etwas weniger“, sagt Will Dempsey, Midrex-Marketingchef.
Bei Energiron ist das Maximum bei annähernd 2,7 Mio. t erreicht. „Viel größer zu bauen macht technisch wenig Sinn“, sagt der Tenova-Manager Markus Dorndorf. Jenseits dessen müssten die Nebenaggregate doppelt oder größer ausgeführt werden, was zu Ineffizienzen führe. Außerdem bestehe die Gefahr, dass die Eisenpellets im Reaktor unter großen Scherkräften zerbrechen, wenn der Durchmesser des Schachtofens erhöht werde.
Jahrhundertinvestitionen in der Stahlindustrie
Der Run auf die Anlagen hat begonnen. Midrex rechnet mit 50 % Marktwachstum bis 2030. Auch die Hüttenwerke in Deutschland wollen umrüsten.
Das Problem aus der Perspektive der Stahlunternehmen ist nur: Die Umrüstung der Hüttenwerke ist teuer. Als Faustregel gilt: Pro 1 Mio. t Roheisenkapazität eines Hochofens würde der Aufbau der DRI-Route 1 Mrd. € kosten. Thyssenkrupp veranschlagt für den Gesamtumbau seiner Duisburger Standorte annähernd 7 Mrd. €. Die deutsche Nummer zwei, Salzgitter, spricht von 3 Mrd. € bis 4 Mrd. € für ihr Hüttenwerk – ebenso wie die Stahl-Holding-Saar. Insgesamt veranschlagen die Hersteller mindestens 15 Mrd. € für den Aufbau einer CO2-ärmeren Stahlproduktion bis 2045. In der Darstellung der Stahlkonzerne ist dieses Geld nicht vorhanden. Ihre Umbaupläne basieren auf Subventionen.
Subventionen für grünen Stahl: Warten auf Brüssel
Matthias Weinberg dreht die Kamera seines Computers weg von seinem Gesicht, hin zum Besprechungstisch in seinem Büro. Darauf steht das maßstabsgetreue, filigrane Modell einer DRI-Anlage. „Können Sie das erkennen?“, fragt er im Videointerview. „Wir sind startklar. Ich glaube, viel mehr brauche ich nicht zu sagen.“
Matthias Weinberg leitet das Kompetenzzentrum Metallurgie bei Deutschlands größtem Stahlkonzern: Thyssenkrupp. Und auf dem Tisch steht die fertig geplante, 3D-gedruckte Miniatur genau der Anlage, die sein Unternehmen bis 2025 bauen will. Thyssenkrupp hat sich – wie andere Stahlhersteller auch – auf Fördergelder der EU beworben, um die Installationskosten bezahlen zu können. Nun liegen die Anträge laut Schilderungen aus der Stahlindustrie bei der Kommission. Und liegen. Und liegen. „Unser Vorschlag ist längst fertig. Jetzt muss auch der regulatorische und finanzielle Rahmen fertig werden“, sagt Weinberg.
Ein zweites Beispiel ist das weltgrößte Stahlunternehmen, ArcelorMittal, das je ein Hüttenwerk in Bremen und Eisenhüttenstadt betreibt. Laut André Körner, Mitglied der Geschäftsführung von ArcelorMittal Deutschland, liegt der CO2-Preis aktuell bei 85 €/t; ab 2026 werde die freie Zuteilung von Emissionszertifikaten an die Stahlhersteller abschmelzen. „Wir sind bereit, die Transformation schnell anzugehen. Die Signale der EU-Wettbewerbshüter deuten jedoch auf große Verzögerungen hin“, sagt Körner.
Seine Botschaft – oder ist es eine Drohung? – an die Adresse der EU-Kommission: „Die Projekte müssen in die Umsetzung kommen, bevor das Management in Zugzwang gerät und andere Entscheidungen treffen muss.“ Würde heißen: Ofen aus, und kein Ersatz.
2025 könnten die ersten Hochöfen abgeschaltet werden
Die DRI-Pläne der Stahlhersteller sind mitunter schon sehr konkret. Thyssenkrupp will – Subventionen vorausgesetzt – bis 2025 seinen kleinsten Hochofen stilllegen und parallel eine DRI-Anlage aufbauen. Bis 2030 soll einer der drei großen Hochöfen folgen. Dann will Thyssenkrupp – in Übereinstimmung mit den bundespolitischen Zielvorgaben – mindestens 30 % weniger CO2 ausstoßen als heute.
Salzgitter plant ebenfalls einen stufenweisen Umbau. Auch hier soll der erste Hochofen 2025 abgeschaltet werden. Mitte der 2030er-Jahre soll der dritte und letzte an der Reihe sein.
ArcelorMittal will bis 2027 den Hochofen in Eisenhüttenstadt sowie einen von zweien in Bremen stilllegen. Bis dahin soll in Bremen eine DRI-Anlage mit einer Jahreskapazität von 2,4 Mio. t entstehen. Das Unternehmen beziffert die Kosten mit über 1 Mrd. €.
Knappheit beim Eisenerz befürchtet
Bereits jetzt zeichnet sich ab: Die Eisenerzrohstoffe werden kapp. Die Anforderungen an das Erz sind auf der DRI-Route hoch. Es muss erstens Reduktionsgas durchströmen lassen und zweitens mechanisch belastbar sein, sodass es auch bei Temperaturen knapp unter 1000 °C nicht erweicht. „Normalerweise liegt das Eisen in haselnussgroßen Kugeln vor. Wenn daraus lauter kleine Pfannkuchen werden, kann kein Gas mehr hindurchströmen“, sagt der Thyssenkrupp-Metallurge Matthias Weinberg.
Noch sind die benötigten Erzqualitäten rar. „Das heutige Angebot an DRI-Pellets würde nie reichen, um die deutschen Hüttenwerke umzustellen“, sagt ArcelorMittal-Manager André Körner. Wenn allerdings eine Nachfrage bestehe, gäbe es auch ein Angebot. „Wir sind das viertgrößte Mining-Unternehmen der Welt, natürlich bereiten wir uns auf diese Nachfrage vor.“
Wie wird grüner Stahl auf DRI-Basis hergestellt?
So einig sich die Stahlkonzerne in der groben Linie sind – Hochofen stilllegen –, so unterschiedlich sind die Pläne im Detail. Auf die Frage, wie sich die Prozesskette hinter der DRI-Anlage fortsetzt, gibt es zwei alternative Antworten. Ein Teil der Hüttenwerke wird künftig Stahl in Elektrolichtbogenöfen produzieren, die schon heute in Elektrostahlwerken genutzt werden. Der andere Teil hält die Struktur des heutigen Stahlwerks intakt: Stahl wird weiterhin im Konverter produziert.
Ein Beispiel für die Elektrostahlvariante ist ArcelorMittal. Der Konzern will mit den Hochöfen auch seine Konverter abschaffen. Das direkt reduzierte Eisen soll im Elektrolichtbogenofen (EAF, electric arc furnace) aufgeschmolzen und zu Stahl legiert werden. In der Branche gilt Elektrostahl häufig noch als qualitativ minderwertig. Laut ArcelorMittal liegt das nicht am Aggregat selbst, sondern an den Einsatzstoffen, heute in der Regel Schrotte. Im DRI-Betrieb „sind die Elektrolichtbogenöfen ebenbürtig, sonst würden wir diesen Weg nicht gehen“, sagt Körner.
Zusätzliches Schmelzaggregat
Thyssenkrupp und Tata Steel im niederländischen IJmuiden wollen Stahl weiterhin im Konverter produzieren und sind deshalb auf eine anlagentechnische Krücke angewiesen: ein zusätzliches Aufschmelzaggregat, das in der Nichteisen-Metallurgie unter dem Namen Submerged Arc Furnace (SAF) firmiert. Dieses ist nötig, weil der Konverter mit flüssigem Material befüllt werden muss, die DRI-Anlage aber festen Schwamm liefert. Heute erfüllt der Hochofen zwei Funktionen: Erstens reduziert er im oberen Teil das Eisenerz zu Roheisen und zweitens verflüssigt er im unteren Teil das Eisen für den Konverter. Die DRI-Anlage wird nur die erste Funktion erfüllen können. Für die zweite braucht es ein Aufschmelzaggregat.
Thyssenkrupp plant noch aus einem anderen Grund mit dem SAF. Die Konverter in den Stahlwerken, die Stranggussanlagen und alle folgenden Aggregate sind auf die Abstichgewichte der Hochöfen ausgerichtet. Elektrolichtbogenöfen wären im Vergleich dazu unterdimensioniert. „Unser Oxygenstahlwerk 1 verarbeitet mit jedem Abstich 380 t Roheisen. So große Elektroöfen gibt es gar nicht“, sagt Weinberg. „Wir können nicht einfach mit kleineren Chargen fahren. Dann müsste man ein komplett neues Stahlwerk bauen.“
Auch in anderen Aspekten steht der SAF für Konstanz. Wie beim Hochofen wird das Eisen erstens per Abstich entnommen. Zweitens liefert er ähnliche Schlacken. Die dabei anfallenden Produkte wie Hüttensand können weiterhin in der Zementindustrie verwendet werden.
Ein letztes Argument für den SAF betrifft den Rohstoffeinsatz. Laut Thyssenkrupp benötigen Elektroöfen schäumende Schlacken mit ganz bestimmter Chemie, damit die Energieabstrahlung des Ofens die Stromkosten nicht in die Höhe schnellen lässt. Das Prozessfenster ist eng, die Anforderung an die Reinheit der Erzpellets hoch. Der SAF mit angeschlossenem Konverter kann größere Schlackenmengen verarbeiten: Die Metallurgie wird gutmütiger, es können auch weniger teure Erze verwendet werden. „Wir wollen beim gleichen Rohmaterialmix landen wie bisher“, sagt Annemarie Manger, die die Dekarbonisierung im Tata-Steel-Hüttenwerk IJmuiden verantwortet.
Tata Steel: Vorteil Seehafen
Voraussetzung für die DRI-Route ist die Verfügbarkeit von Wasserstoff in großen Mengen. ArcelorMittal veranschlagt 250 000 t pro Jahr, Tata Steel 400 000 t und Thyssenkrupp 700 000 t. „Diese Mengen können nur aus einer Pipeline kommen“, sagt ArcelorMittal-Manager André Körner.
Annemarie Manger bezeichnet die Wasserstoffversorgung als „Henne-Ei-Problem“. Die Wasserstoffproduzenten der Niederlande warten auf Kunden, die Kunden auf eine garantierte Versorgung. „Wir können der Ankerkunde sein und große Mengen Wasserstoff abnehmen“, sagt Manger.
Die aktuellen Pläne der niederländischen Regierung sehen den Ausbau der Offshore-Windenergie auf 21 GW bis 2030 vor. Tata will sowohl den damit produzierten Wasserstoff abnehmen als auch den Windstrom direkt, um das Gas vor Ort per Elektrolyse herzustellen. Der Konzern plant, bis 2025 einen 100-MW-Elektrolyseur in Betrieb zu nehmen; parallel entsteht ein 2-GW-Transformator für die Stromnutzung gleich neben dem Werksgelände.
Bleibt die Frage, ob sich auf der DRI-Route so viel Geld verdienen lässt, dass sich die Milliardeninvestitionen amortisieren. Oder anders formuliert: Ist die DRI-Route in Europa überhaupt wirtschaftlich? Brancheninsider gehen für den fertigen Stahl von annähernd 100 €/t Mehrkosten im Vergleich zur Hochofenroute aus. Bislang sind integrierte Hüttenwerke zudem weitgehend energieautark, abgesehen vom Kokseinkauf. In Zukunft sind sie deutlich stärker vom Strompreis abhängig – mit ungewissem Ausgang.
Fest steht nur: Den Hochofen können sich die Stahlhersteller garantiert nicht mehr leisten.