Direktreduktion: Diese Technik wird bei Thyssenkrupp den Hochofen beerben
Für das Kernaggregat der wasserstoffbasierten Stahlproduktion, die Direktreduktionsanlage, gibt es nur zwei maßgebliche Anlagentypen. Ein Technikvergleich.
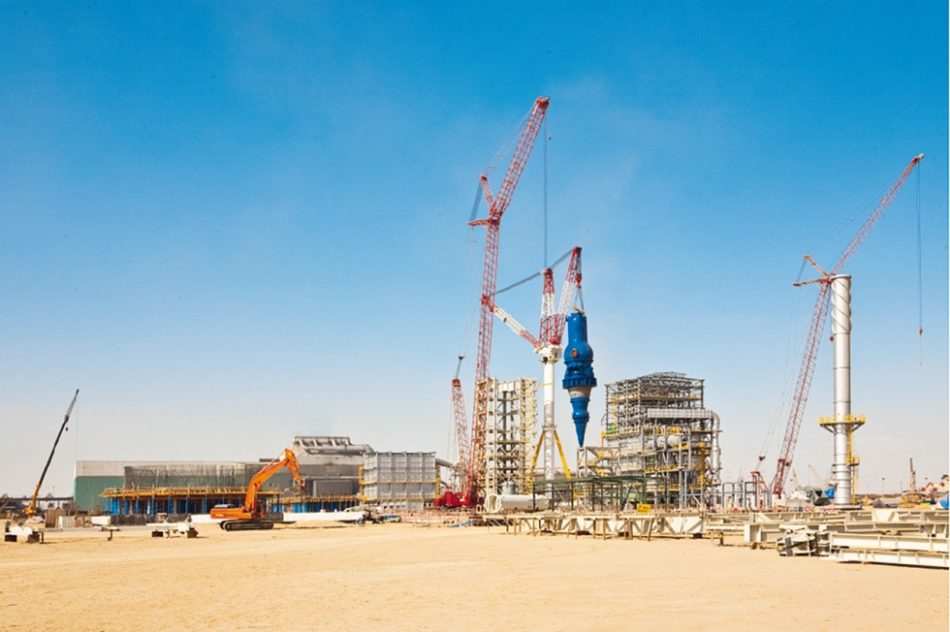
Foto: Energiron
Inhaltsverzeichnis
Die Stahlkonzerne in Deutschland stehen vor kolossalen Investitionen. Die Umstellung auf die Direktreduktion kostet die die Nummer 1, Thyssenkrupp 7 Mrd. €, Salzgitter spricht von 3 Mrd. € bis 4 Mrd. €, ebenso wie die Stahl-Holding-Saar. Hinzu kommen ArcelorMittal und die Hüttenwerke Krupp-Mannesmann. Insgesamt veranschlagen die Hersteller mindestens 15 Mrd. € für den Aufbau einer CO2-ärmeren Stahlproduktion bis 2045.
Der Großteil davon wird für Direktreduktionsanlagen (DRI-Anlagen) benötigt. Das sind großindustrielle Aggregate, in denen aus Eisenerz (Fe2O3) Eisen hergestellt wird. Weltweit gibt es davon nur zwei maßgebliche Typen: Midrex und Energiron. Midrex ist zugleich der Name des US-Unternehmens, das die Anlagen plant. Energiron ist eine Gemeinschaftsentwicklung der italienischen Anlagenentwickler Tenova und Danieli. In einigen wesentlichen Punkten unterscheiden sich die beiden Prozesse voneinander.
Warum ist die Direktreduktions-Technologie wichtig?
Die Direkreduktions-Anlage kann den Hochofen als zentrales Aggregat der Stahlbranche ablösen. Der Hochofen ist industrieübergreifend einer der großen CO2-Emittenten. Im Jahr 2019 emittierten die Eisenhütten in Deutschland 37,2 Mio. t CO2, was einem Anteil von 4,6 % an den Gesamtemissionen entsprach.
Direktreduktionsanlagen kommen – anders als Hochöfen – ohne Kokskohle aus. Heutige Aggregate nutzen vor allem Erdgas und emittieren deshalb grob gerechnet nur halb so viel CO2. Auch für die deutschen Hüttenwerke ist zunächst der Erdgasbetrieb geplant – zumindest war das vor dem Ukrainekrieg der Plan. Mit der Zeit soll immer mehr Wasserstoff eingesetzt werden.
Was bedeutet Direktreduktion?
Unter Reduktion versteht man den Prozess, Eisen aus Eisenerz zu gewinnen. Im Hochofen wird das Eisen aufgeschmolzen und beim Abstich ausfließen gelassen. Direktreduktion bedeutet demgegenüber, dass das Eisen nie flüssig ist.
Eine Direktreduktionsanlage ist ein Schachtofen. Oben werden Eisenerz-Pellets eingefüllt, die kontinuierlich hinunter sacken. Zeitgleich strömt Reduktionsgas – Kohlenmonoxid (CO) und Wasserstoff (H2) – den Ofen hinauf. Das Gas beraubt das Eisen der Sauerstoffatome. So wird aus Fe2O3 erst Fe3O4, dann FeO und schließlich Fe, also Eisen mit ein bisschen Kohlenstoff, das unten als fester, kugelförmiger Eisenschwamm herausfällt. Dieses reduzierte Eisen wird im Stahlwerk anschließend zu Stahl legiert.
Gibt es schon Direktreduktions-Anlagen?
ArcelorMittal betreibt im Elektrostahlwerk Hamburg eine Direkreduktions-Anlage mit einer Kapazität von 600 000 Jahrestonnen. Durchgesetzt hat sich das Verfahren aber vor allem dort, wo Erdgas günstig ist, etwa in Russland, in den USA und auf der arabischen Halbinsel. Der Anlagenbauer SMS group schätzt die weltweit installierte Kapazität auf annähernd 100 Mio. t. Zum Vergleich: Weltweit wurden 2021 1,9 Mrd. t Stahl produziert.
Zentrale Unterschiede der Verfahren von Midrex und Energiron
Wie funktioniert Midrex?
Das Midrex-Verfahren ist auf einen externen Reformer angewiesen, in dem Methan (CH4) in die Reduktionsgase Wasserstoff und Kohlenstoffmonoxid gecrackt wird. Das Reduktionsgas wird bei einem vergleichsweise moderaten Druck von 2,5 bar und bei einer Temperatur um 950 °C in den Reaktor eingebracht. Oben am Schachtofen wird das CO2– und wasserreiche Abgas aufgefangen und abgekühlt, sodass das Wasser heraustropfen kann. Das CO2 gelangt in den Reformer und der Prozess beginnt von vorn.
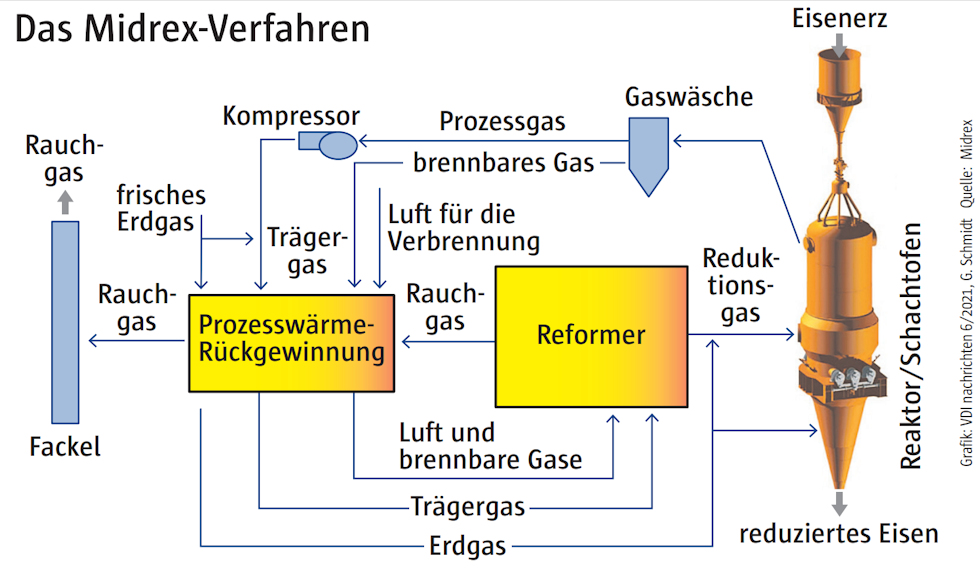
Wie funktioniert Energiron?
Im Energiron-Reaktor sind die Drücke höher – 6 bar bis 8 bar – und es ist auch etwas heißer: 1050 °C bis 1080 °C. Das CO2 wird chemisch aus dem Abgas herausgewaschen und kann vermarktet werden. Der restliche Gasstrom wird befeuchtet, mit frischem Erdgas versetzt, in einem Prozessgaserhitzer erwärmt und schließlich in den Reaktor gebracht.
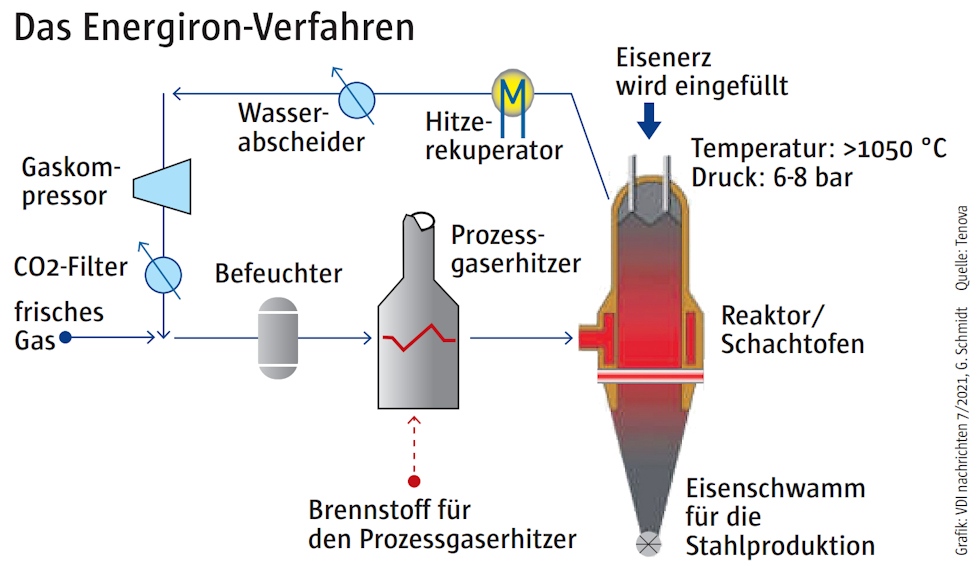
Wo liegen die Unterschiede?
Es gibt einige wesentliche Unterschiede (s. Tabelle). Dazu zählen neben den Reaktordrücken und -temperaturen das Erdgas-Reforming, die Abdichtung des Reaktors, die CO2-Abscheidung und die Umrüstbarkeit auf Wasserstoffbetrieb.
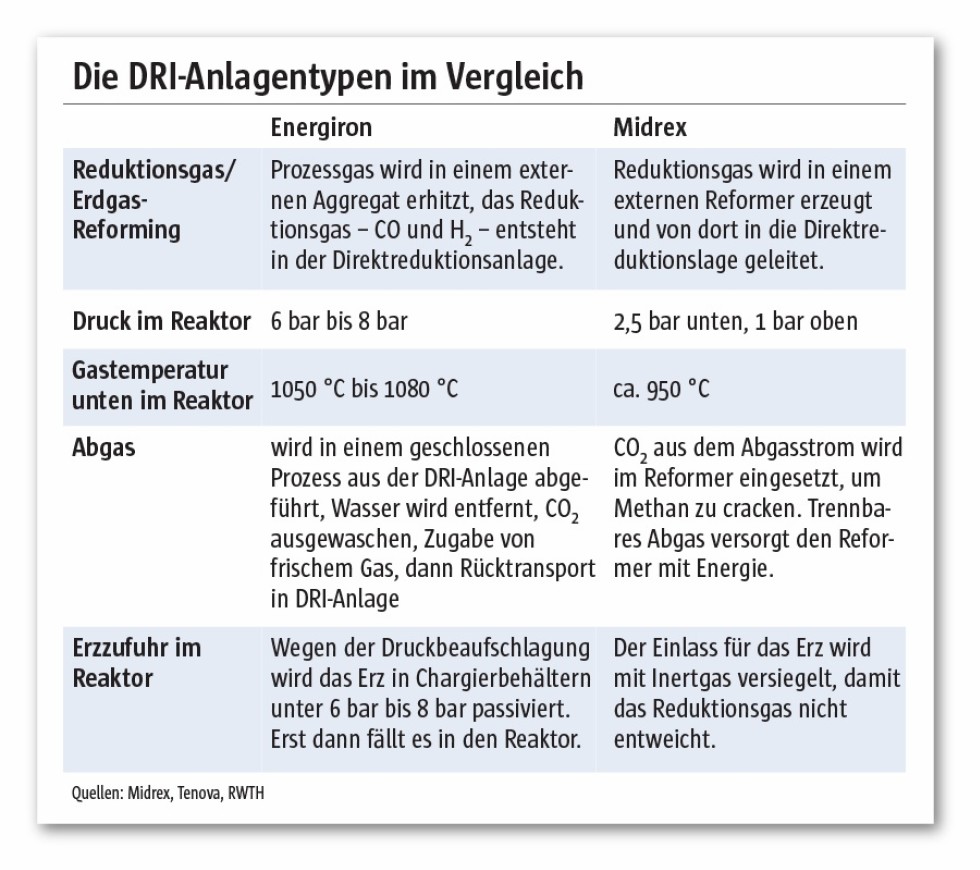
Welchen Einfluss haben die hohen Drücke bei Energiron?
Durch den hohen Druck im Reaktor ist nach Tenova-Angaben die Strömungsgeschwindigkeit des Gases niedrig. Viel Reduktionsgas ist also lange im Reaktor – mit positiven Effekten für die Durchgasung und die Reduktion des Eisens.
Zudem wirken sich die hohen Drücke auf den Kohlenstoffgehalt des Eisens aus. Eisen hat einen Schmelzpunkt von 1538 °C. Wenn sich 4,3 % Kohlenstoff in der Matrix einlagern, sinkt der Schmelzpunkt auf 1147 °C. Ein hoher Kohlenstoffgehalt des Eisens ist auch im Stahlwerk erwünscht, genauer: im Elektrolichtbogenofen. Hier entsteht mit eingeblasenem Sauerstoff CO, das die Schlacke im Ofen aufgehen lässt, wie einen Hefeteig. Die Schaumschlacke hüllt den Lichtbogen ein, wodurch sich die Wärmeenergie besser verteilt. Laut Tenova ist Energiron der einzige Direktreduktions-Prozess, der mehr als 2,5 % Kohlenstoffgehalt ermöglicht.
Wie sind die Reaktoren abgedichtet?
Midrex nutzt rund um den Erzeinlass und den Eisenauslass Inertgassiegel. Ähnlich den Warmluftschleusen an Kaufhaustüren sorgen sie dafür, dass das Reduktionsgas nicht entweicht.
Im Energiron-Prozess kommen mechanische Dichtungen zum Einsatz. Die Erzpellets werden in einem Chargierbehälter unter Druck gesetzt und erst dann in den Reaktor gegeben. Markus Dorndorf, Vice President Iron & Steel Making bei Tenova, spricht von einem „Schleusenprinzip ähnlich wie auf einer Raumstation“.
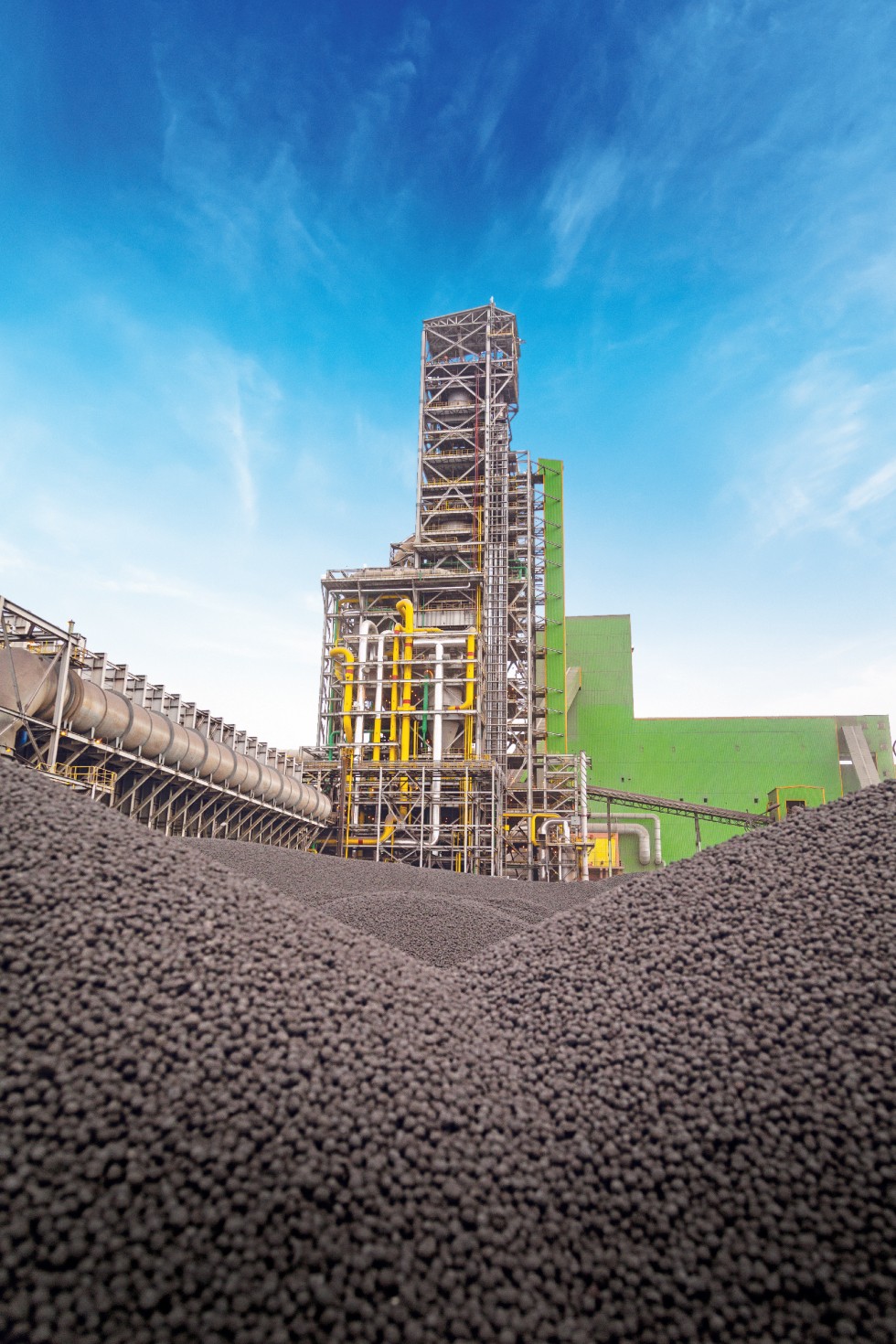
Hauptunterschied: Reformer vs. Prozessgaserhitzer
Wie unterscheidet sich das Erdgas-Reforming?
Bei Midrex ist der Reformer ein externes Aggregat, das auf CO2 aus dem Abgasstrom des Reaktors als Sauerstoffquelle angewiesen ist. Das Reforming ist ein endothermer Prozess: Es muss also Wärmeenergie hineingesteckt werden. Dadurch, dass dieser Prozess außerhalb des Reaktors stattfindet, sind die Reaktortemperaturen laut Midrex niedriger; die Gefahr, dass die Eisenpellets verkleben, sinkt.
Lesetipp: Dossier zu den Direktreduktionsplänen der europäischen Hüttenwerke
Bei Energiron gibt es keinen eigenen Reformer, sondern einen Prozessgaserhitzer. Das eigentliche Reforming des Erdgases geschieht im Reaktor, der dafür nötige Sauerstoff stammt aus dem Eisenerz. Laut Markus Dorndorf ist das beim Umstieg auf Wasserstoff ein Vorteil. Energiron biete „die Flexibilität, mit demselben Anlagenaufbau jede Art von Reduktionsgas in verschiedenen Mischungsverhältnissen zu verwenden, von Erdgas über Koksofengas bis hin zu Wasserstoff“.
Was ändert sich in den DRI-Anlagen im Wasserstoffbetrieb?
Für den Energiron-Prozess gilt: Wenn der Anteil des Wasserstoffs am Reduktionsgas über einen Schwellenwert klettert, wird die CO2-Wäsche für den Abgasstrom nur noch im Standby betrieben. Auch Midrex würde für den Wasserstoffbetrieb einen Prozessgaserhitzer nutzen, oder den Reformer zum Heizen nutzen. Der RWTH-Metallurge Dieter Senk sieht Energiron im Vorteil: Das Verfahren biete „die große Chance, mit mehr Wasserstoff und weniger Erdgas zu arbeiten“.
Größte Direktreduktions-Anlagen mit 2,5 Mio. t Jahreskapazität
Erreichen Direktreduktions-Anlagen die Kapazitäten großer Hochöfen?
Die größten Hochöfen produzieren zwischen 3,6 Mio. t und 4 Mio. t Roheisen pro Jahr. Solche Größenordnungen zeichnen sich bei den Direktreduktions-Anlagen noch nicht ab. Die größten Anlagen beider Typen rangieren um 2,5 Mio. t Jahreskapazität. „Wir haben ein Design für 3 Mio. Jahrestonnen, aber das größte kommerziell bewährte Design schafft etwas weniger“, sagt Will Dempsey, Midrex-Marketingchef.
Bei Energiron ist das Maximum bei annähernd 2,7 Mio. t erreicht. „Viel größer zu bauen macht technisch wenig Sinn“, sagt der Tenova-Manager Markus Dorndorf. Jenseits dessen müssten die Nebenaggregate doppelt oder größer ausgeführt werden, was zu Ineffizienzen führe. Außerdem bestehe die Gefahr, dass die Eisenpellets im Reaktor unter großen Scherkräften zerbrechen, wenn der Durchmesser des Schachtofens erhöht werde.
Wann steigen die Stahlhersteller in Deutschland auf die DRI-Route um?
Der Run auf die Anlagen hat begonnen. Midrex rechnet mit 50 % Marktwachstum bis 2030. Auch die Hüttenwerke in Deutschland wollen umrüsten. Aber es gibt ein Problem. Die Direktreduktions-Technologien sind teuer. Als Faustregel gilt: Je 1 Mio. t Roheisenkapazität in den Hochöfen fallen bis 1 Mrd. € Umbaukosten an. Ohne Subventionen können die Hüttenwerke die Investitionen nicht stemmen – zumindest nach eigener Darstellung. Thyssenkrupp und Co. haben deshalb Förderanträge in Brüssel eingereicht, aber vor Ende des Jahres – so ist zu hören – wird darüber nicht entschieden.
Gleichzeitig tickt die Uhr, weil absehbar die Gratiszuteilungen für CO2-Zertifikate abschmelzen. Die Stahlkonzerne bereiten deshalb die Anlagenplanung vor, so weit sie können, um später die Zeit zwischen Auftragsvergabe und Inbetriebnahme zu verkürzen.