Kohlenstoffkreislauf bei Kunststoffen schließen
Mit einer neuen Technik lassen sich über 40 % aller im Plastik gebundenen Kohlenstoffatome für die Synthese neuer Kunststoffe wiedergewinnen.
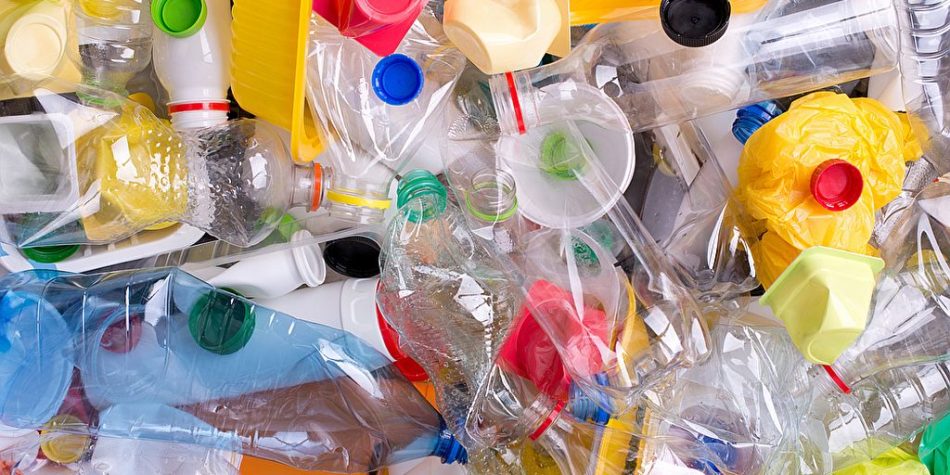
Foto: panthermedia.net/photkas
Eine TU und drei Firmen wollen das Plastikrecycling umkrempeln. Ihr Plan: den Kohlenstoff im Abfall, der heute thermisch entsorgt wird, als Rohstoff für Chemikalien zu verwenden. „Wir wollen mehr als 40 % der Kohlenstoffatome im Wirtschaftskreislauf halten“, sagt Bernd Meyer, Direktor des Instituts für Energieverfahrenstechnik und Chemieingenieurwesen an der TU Bergakademie Freiberg. Mit dabei sind das Abfallunternehmen Remondis in Lünen, die britische Chemiefirma Ineos sowie RWE Power in Essen. Alle vier firmieren als Arbeitsgemeinschaft Kohlenstoffkreislaufwirtschaft NRW (Arge K2 NRW).
Vorprozessierte Kunststoffabfälle wird Remondis liefern. Die Bergakademie wiederum kennt Wege, um daraus Kohlenmonoxid (CO), Kohlendioxid (CO2) und Wasserstoff (H2) zu gewinnen. Den Kohlenstoff im Gasgemisch will Ineos zur Herstellung chemischer Produkte nutzen. RWE steuert Braunkohle als weitere heimische Kohlenstoffquelle bei. Zurzeit sucht die Arge mögliche Standorte in NRW für eine solche Kohlenstoffkreislaufanlage, in der mehrere 100 000 t Abfälle und Braunkohle pro Jahr chemisch recycelt werden können.
Im Fokus stehe jener kunststoffhaltiger Abfall, betont Verfahrenstechniker Meyer, der sich werkstofflich nicht wirtschaftlich recyceln lässt. Es sind Mischkunststoffe, Sortierreste, Schredderleichtfraktionen sowie thermisch nicht verwertbare Verbundwerkstoffe wie carbon- oder glasfaserhaltige Materialien.
In Deutschland fallen davon rund 2 Mio. t/Jahr an. Das meiste landet in Müllverbrennungsanlagen. Sie nutzen die in den Abfällen enthaltene Energie thermisch, wandeln damit aber jedes Kohlenstoffatom in CO2 um. Für Meyer ist das Verschwendung. „Die Kohlenstoffrecyclingquote beträgt Null.“ Das verdiene den Namen Recycling nicht. 2015 wurde gut die Hälfte der gesammelten 5,9 Mio. t Kunststoffabfälle verbrannt.
Die Vision der Arge ist die Kohlenstoffkreislaufwirtschaft. Es braucht dafür eine technische Brücke zwischen Abfällen und reinen Produkten. Eine solche könnte die Vergasung sein. Plastik- und Holzabfall, Biomüll sowie Kohle werden bei über 1000 °C in Synthesegas zerlegt. Dies passiert bereits großtechnisch.
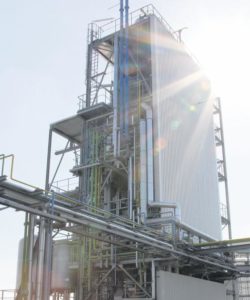
In Edmonton, Kanada, betreibt Anlagenbauer Enerkem einen Wirbelschichtvergaser, der täglich bis zu 350 t Kunststoff aus Hausmüll in Synthesegas umwandelt, um daraus Methanol und Ethanol zu gewinnen. In Kawasaki bei Tokio arbeitet bei der Chemiefirma Showa Denko ein Wirbelschichtvergaser von Ebara Environment. Er verwertet täglich knapp 200 t Plastikabfälle aus den Vorstädten Tokios. Showa Denko verflüssigt das CO2 und verkauft es an Getränkehersteller. Aus Wasserstoff und Luftstickstoff stellt es täglich rund 175 t Ammoniak her.
Dieses Abfallrecycling findet Interesse. Air Liquide, AkzoNobel, Enerkem und der Rotterdamer Hafen wollen so bis zu 1000 t Kunststoff- und Mischabfälle in bis zu 600 t Methanol pro Tag umwandeln. Enerkem vereinbarte zudem mit der Firma Sinobioway der Uni Peking den Bau von 100 Wirbelschichtvergasern in den nächsten 17 Jahren.
Die Technik der Vergasung wurde vor 100 Jahren in Deutschland erfunden. Sie hat sich weltweit dynamisch weiterentwickelt. Drei Vergasertypen haben sich etabliert. Zwei seien für dieses Recycling jedoch wenig geeignet, so Meyer: In Flugstromvergasern müsse das Material staubförmig sein, damit eine heiße Vergasungsflamme entsteht. Kunststoffabfälle so fein zu mahlen, sei aufwendig. Auch für Wirbelschichtvergaser müssen Abfälle fein verteilt werden. „Dies senkt die Wirtschaftlichkeit, wie Ebaras und Enerkems Erfahrungen zeigen“, sagt Meyer.
Er setzt auf Festbettvergaser mit Schlackeabzug: „Bei denen ist weniger wichtig, wie das Material im Reaktor verteilt ist.“ Theoretisch könnten Abfälle in einer Stückgröße von bis zu 20 cm verwertet werden. Mit diesem neuesten Stand der Technik erwartet er Kohlenstoffrecyclingquoten von mehr als 40 %.
Ob sich die Arge für einen solchen Festbettvergaser entscheidet, ist offen. Es fehle der Praxistest, weiß Meyer. In dem Versuchsvergaser der Bergakademie könnte zwar 1 t Abfall pro Stunde aufgegeben werden – aber nur in einer Körnung bis zu 3 cm Größe. Das will Meyer ändern. Er möchte das Beschickungssystem des Vergasers umbauen, um großformatige Abfälle durch eine größere Schleuse einbringen zu können.
Meyers Hoffnung: einen für Abfälle konzipierten Festbettvergaser mit einer Jahreskapazität von 20 000 t in Freiberg bauen und testen zu können. Funktioniert dieser, soll er im Chemiepark Leuna seine Betriebsreife nachweisen. Wie in NRW kann dann auch in Sachsen-Anhalt Plastikabfall allein oder gemischt mit Braunkohle vergast werden.
Die Klimabilanz der Vergasung sei selbst dann positiv, wenn Braunkohle mitverwendet wird, betont Meyer. Er verweist auf eine Studie der Bergakademie und des Instituts für Technikfolgenabschätzung und Systemanalyse am Karlsruher Institut für Technik (KIT) im Auftrag des Bundesforschungsministeriums.
Darin geht es um Ethen, die Grundsubstanz des Polyethylens (PE). Berechnet wurde, wie viel CO2 frei wird, wenn Ethen aus Erdöl oder wenn es aus Plastikmüll und Braunkohle hergestellt wird. Berücksichtigt wurde, dass bei PE aus fossilem Ethen, das am Ende des Lebenszyklus verbrannt wird, mehr CO2 entsteht, als wenn PE aus Ethen aus Plastikabfall und Kohle am Lebensende vergast wird. Das Ergebnis freut Meyer: „Wird jeweils 50 % Plastikmüll und Braunkohle eingesetzt, ist die CO2-Bilanz um 25 % besser als die der Erdölchemie.“