Thyssen setzt auf Wasserstoff
Deutschlands größter Stahlkonzern will in Zukunft vermehrt in Wasserelektrolyse investieren und sich langfristig vom Hochofen verabschieden.
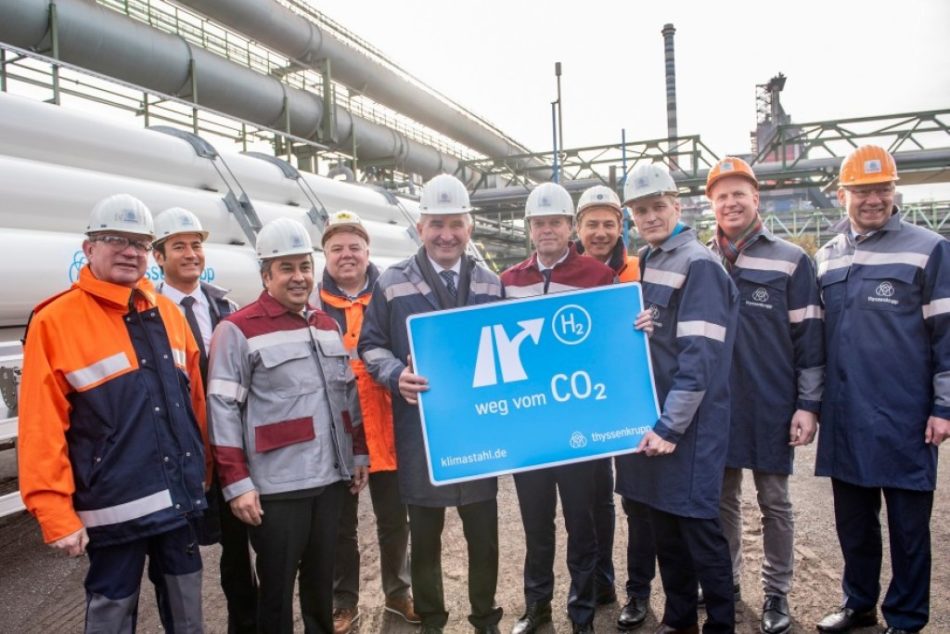
Foto: thyssenkrupp
Deutschlands Stahlprimus Thyssenkrupp will verstärkt in die Produktion „grünen“ Wasserstoffs einsteigen. Ab sofort könnten pro Jahr Elektrolysezellen mit einer Gesamtleistung von bis zu 1 GW gefertigt werden, teilte der Essener Konzern am Montag mit. Je mehr Wasserstoffprojekte man verfolge, desto stärker würden die Kapazitäten ausgebaut.
„Grüner“ Wasserstoff bezeichnet Wasserstoff, der nicht aus der erdgasbasierten Dampfreformation gewonnen wird, sondern aus der theoretisch CO2-freien Wasserelektrolyse. Dabei wird Wasser unter Stromeinsatz in seine Bestandteile Wasserstoff und Sauerstoff gespalten.
Wasserstoffstrategie der GroKo
Die schwarz-rote Koalition will eine Wasserstoffstrategie vorlegen. Ziel sei es, Deutschland auf diesem Feld zum „Ausrüster der Welt“ zu machen, heißt es im Eckpunktepapier für das Konjunkturpaket. Die Entwicklung von Produktionsanlagen soll gefördert werden. Bis 2030 sollen zunächst Anlagen von bis zu 5 GW Gesamtleistung entstehen, bis 2035 sollen weitere Kapazitäten dazukommen. Für die Förderung von Wasserstoff-, Brennstoffzellen- und Batterietechnologie sind Finanzmittel in Höhe von 7 Mrd. € vorgesehen.
Thyssenkrupp setzt auf vorgefertigte Standardmodule, um den Bau neuer Elektrolyseure so einfach und kostengünstig wie möglich zu gestalten, heißt es in der Mitteilung des Unternehmens. Das Prinzip: Hunderte und Tausende solcher Zellen können zu einem großen Elektrolyseur verschaltet werden. Auf diese Weise können die Zellen in Serie produziert werden.
Der bisherige Weg: Hochofenroute
Hochofenroute nennen sie in der Stahlbranche den klassischen Weg der Stahlproduktion. Zunächst wird in der Kokerei aus Kokskohle Koks erzeugt. Im Hochofen entsteht anschließend aus Koks und Eisenerz (Fe2O3) Roheisen. Die Eisenatome werden durch Kohlenstoffatome und Kohlenmonoxidmoleküle (CO) ihrer Sauerstoffatome beraubt, oder in der Fachsprache der Metallurgie: sie werden „reduziert“. Deshalb fallen in der Roheisenproduktion gigantische Mengen CO2 an. Allein im integrierten Hüttenwerk Salzgitter, einem der großen deutschen Standorte, sind das annähernd 8 Mio. t pro Jahr. Anschließend gelangt das flüssige Eisen zum Konverter, wo unter Zugabe der Legierungselemente der Stahl erzeugt wird.
Die Wasserstoffroute
In Zukunft könnte die Wasserstoffroute der Branchenstandard sein. An deren Anfang steht die Elektrolyse. In einer Direktreduktionsanlage – sie trägt diesen Namen, weil das Eisen reduziert wird, ohne verflüssigt zu werden – reagieren Eisenerz und Wasserstoff zu Roheisen und Wasser. Im letzten Schritt wird das Roheisen im Elektrolichtbogenofen zu Stahl legiert.
Vereinfacht gesagt weichen also die Kokereien den Elektrolyseuren, die Hochöfen den Direktreduktionsanlagen und die Konverter den Elektrolichtbogenöfen.
Der Elektrolichtbogenofen findet sich schon heute in jedem Elektrostahlwerk. Auch Direktreduktionsanlagen sind im großtechnischen Maßstab bereits vereinzelt in Betrieb. Ob die Wasserstoffroute wirklich gangbar ist, steht und fällt deshalb mit der Wasserelektrolyse. Anlagen, die den Wasserstoffdurst eines ganzen Stahlwerks stillen könnten, gibt es heute noch nicht.